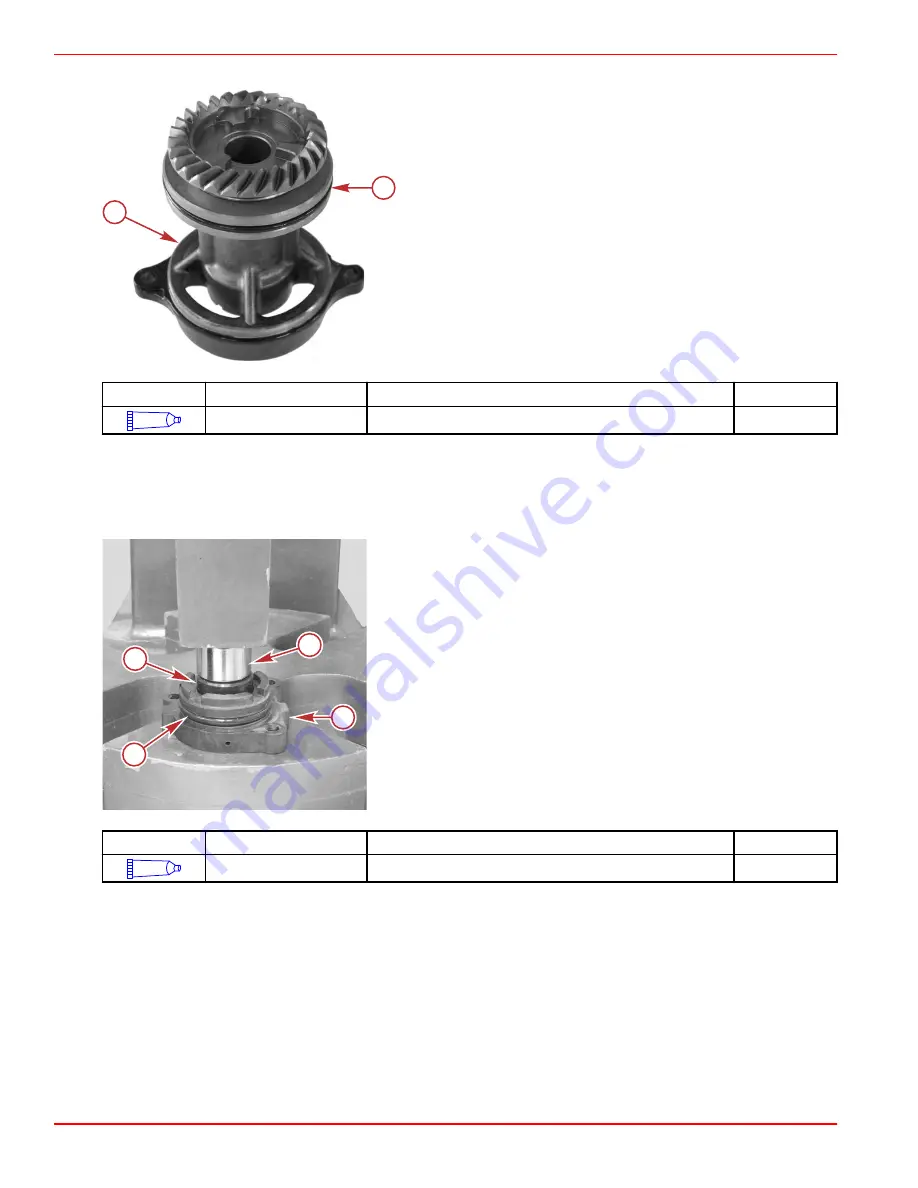
7. Apply 2‑4‑C with PTFE to the new bearing carrier O‑ring. Install the O‑ring onto the bearing carrier.
a -
Bearing carrier
b -
O‑ring
Tube Ref No.
Description
Where Used
Part No.
95
2-4-C with PTFE
Bearing carrier O-ring
92-802859A 1
Water Pump Base Assembly
1. Using a suitable mandrel, press on the face of the water pump seal until the seal is seated in the water pump base.
2. Apply 2‑4‑C with PTFE to the seal lips.
3. Apply 2‑4‑C with PTFE onto a new O‑ring and install the O‑ring onto the water pump base.
a -
Mandrel
b -
Seal
c -
O‑ring
d -
Water pump base
Tube Ref No.
Description
Where Used
Part No.
95
2-4-C with PTFE
Apply to seal lips and O-rings
92-802859A 1
a
b
62933
a
b
c
d
6831
Gear Housing (2.15:1)
Page 6A-30
© 2018 Mercury Marine
90-8M0125265 eng NOVEMBER 2017
Summary of Contents for 15 EFI FourStroke
Page 1: ...SERVICE MANUAL 15 20 EFI FourStroke...
Page 5: ...90 8M0125265 eng NOVEMBER 2017 2018 Mercury Marine Page iv...
Page 31: ...Maintenance Notes Page 1B 20 2018 Mercury Marine 90 8M0125265 eng NOVEMBER 2017...
Page 49: ...General Information Notes Page 1C 18 2018 Mercury Marine 90 8M0125265 eng NOVEMBER 2017...
Page 71: ...General Troubleshooting Notes Page 1E 14 2018 Mercury Marine 90 8M0125265 eng NOVEMBER 2017...
Page 91: ...Ignition Notes Page 2A 20 2018 Mercury Marine 90 8M0125265 eng NOVEMBER 2017...
Page 117: ...Fuel System Operation Notes Page 3A 6 2018 Mercury Marine 90 8M0125265 eng NOVEMBER 2017...
Page 124: ...Service Procedures Notes 90 8M0125265 eng NOVEMBER 2017 2018 Mercury Marine Page 3C 3...
Page 147: ...Service Procedures Notes Page 3C 26 2018 Mercury Marine 90 8M0125265 eng NOVEMBER 2017...
Page 185: ...Cylinder Block Crankcase Notes Page 4A 38 2018 Mercury Marine 90 8M0125265 eng NOVEMBER 2017...
Page 272: ...Power Tilt Notes 90 8M0125265 eng NOVEMBER 2017 2018 Mercury Marine Page 5B 3...
Page 301: ...Power Tilt Notes Page 5B 32 2018 Mercury Marine 90 8M0125265 eng NOVEMBER 2017...
Page 306: ...Gear Housing 2 15 1 Notes 90 8M0125265 eng NOVEMBER 2017 2018 Mercury Marine Page 6A 5...
Page 343: ...Gear Housing 2 15 1 Notes Page 6A 42 2018 Mercury Marine 90 8M0125265 eng NOVEMBER 2017...
Page 346: ...Throttle and Shift Linkage Notes 90 8M0125265 eng NOVEMBER 2017 2018 Mercury Marine Page 7A 3...
Page 381: ...Tiller Handle Notes Page 7B 24 2018 Mercury Marine 90 8M0125265 eng NOVEMBER 2017...
Page 384: ...Recoil Starter Notes 90 8M0125265 eng NOVEMBER 2017 2018 Mercury Marine Page 8A 3...
Page 395: ...Notes Color Diagrams Page 9A 2 2018 Mercury Marine 90 8M0125265 eng NOVEMBER 2017...
Page 396: ...Notes Color Diagrams 90 8M0125265 eng NOVEMBER 2017 2018 Mercury Marine Page 9A 3...
Page 405: ...Color Diagrams Notes Page 9A 8 2018 Mercury Marine 90 8M0125265 eng NOVEMBER 2017...