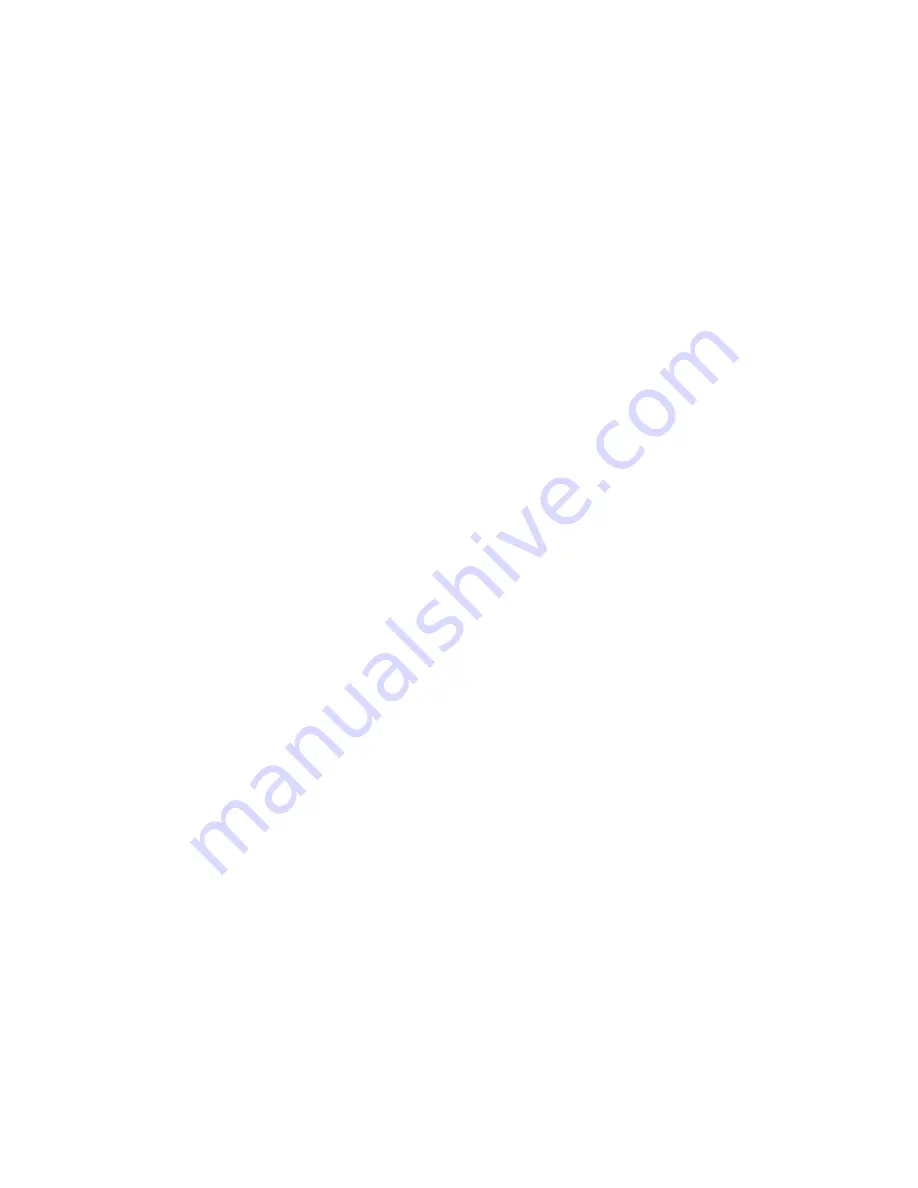
12
ASSEMBLY SUGGESTIONS
You will find the machine is easier to assemble if the set-up instructions are followed in the order
given in the manual.
Before beginning, sort the various bolt bags, hardware bags and hydraulic bags according to what
part of the unit that is being setup. Refer to the end of the parts listing in appendix B. Only open
the bag or bags that are required as the setup instructions are followed.
Whenever the terms “left” and “right” are used, it should be understood to mean when standing
behind and facing the unit. This is also known as the “driver’s left” and the “driver’s right.”
The term “field position” refers to the position the harrows are in when the unit is being used in
the field - that is, with the wings out and the harrow sections down.
The term “transport position” refers to the position the harrows would be in when the unit is
being transported from place to place - that is, with the harrows up and the wings folded and
secured with the tie-bar.
When assembling, make sure the parts are securely held before proceeding to the next step.
Bolt torque specifications are given in appendix A.
The hydraulic cylinder and hose requirements are listed in the parts listing in appendix B. It is
not recommended that other size cylinders or hoses be substituted. Hoses are marked with the
part number near the ends. The last three digits indicate the hose length in inches. Fittings with
a restrictor are marked with an ‘R’.
A dual acting hydraulics supply is required.
Tire requirements are also listed in the parts listing in appendix B.
Layout diagrams for each unit may be found in appendix C. Mark the page with the diagram that
refers to your unit, it will be referred to periodically throughout the manual.
Summary of Contents for WDL-2000
Page 47: ...APPENDIX B 47 HYDRAULIC TRANSPORT WHEEL PARTS DIAGRAM ...
Page 49: ...APPENDIX B 49 AUTO BACKUP WING PULL TUBE PARTS DIAGRAM ...
Page 52: ...APPENDIX C 52 WDL 2040 HARROW CART LAYOUT DIAGRAM ...
Page 53: ...APPENDIX C 53 WDL 2050 HARROW CART LAYOUT DIAGRAM ...
Page 54: ...APPENDIX C 54 WDL 2060 HARROW CART LAYOUT DIAGRAM ...
Page 55: ...APPENDIX C 55 WDL 2070 HARROW CART LAYOUT DIAGRAM ...