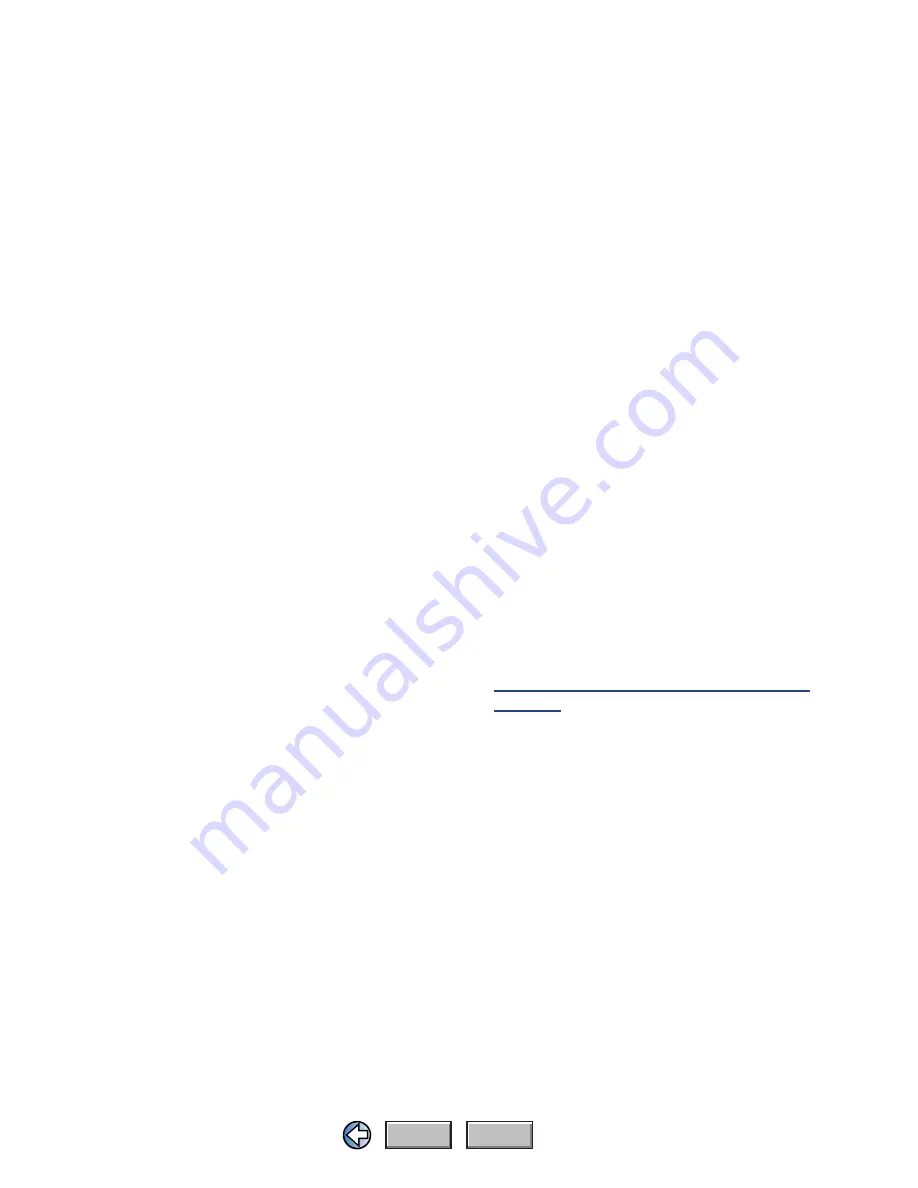
Comet Executive Gas
Operating Guidelines
3-13
Final Rinse
The final rinse can affect the quality of
flatwork finishing. It is important all flatwork be
thoroughly rinsed before entering the unit to keep
flatwork from sticking to the ironing cylinder. A
pH level of 7.2 is recommended.
Add a fabric softener to prevent static
electricity from causing the flatwork to stick.
Never use starch in the final rinse.
A warm rinse allows more water to be extracted
from the material. Thus, the unit needs to remove
less moisture from the flatwork. Additionally,
with warm flatwork, the unit does not have to
work as hard to keep at set temperature. This
produces flatwork with a dry, high quality
finish—more efficiently.
Moisture Retention
Another important factor in delivering a high
quality finish is the amount of moisture retained
(MR) in the flatwork. The correct MR helps to
determine the ironing speed and temperature—
drying flatwork after just one run through the ironer.
A few important factors in moisture retention
(MR) before ironing are:
•
Wash formula–write down the standard
for consistency
•
Extraction process–write down the
standard for consistency
•
Tumble dry condition time–write down
the standard for consistency
•
Type of fabric–higher percentage of
cotton, the more moisture retained
•
Thickness of fabric–thinner material
retains less moisture
With too little moisture, flatwork can cause static
buildup problems. If too much moisture is left in the
flatwork, the ironing section must work harder in
order to process the work, by either slowing down
the speed or increasing the temperature.
After extraction, the optimum MR is 30% -
35% for polyester/cotton fabrics and 45% - 50%
for cotton fabrics.
1. Use a precise scale to measure the “still
wet, but extracted” flatwork; then weigh
again after the same flatwork is “com
-
pletely dry”.
2. Subtract the weight of the “completely
dry” flatwork from the “still wet, but
extracted” flatwork. Divide the weight
difference by the “completely dry” flat
-
work weight. Finally, multiply the result
-
ing weight by 100 to determine the MR
percentage.
The optimum MR after ironing is 4% or less.
Ironing is not intended to remove 100% of the
moisture from the flatwork. Therefore, feel the
flatwork when it first comes out of the unit; there
should be a slight moisture content.
Allow the flatwork to sit for a few minutes to
allow excess steam and heat to dissipate in the
air. Check the flatwork again; it should now feel
dry to the touch.
If the flatwork does not feel dry or to improve
the quality of finish and productivity, repeat
Conditioning Flatwork Before Ironing on
.
Timing Between Washing and Ironing
The amount of time delayed between washing
and ironing/drying reduces the flatwork finish
quality due to fabric cooling and MR. Flatwork
needs to be ironed directly from the washer/
extractor whenever possible.
Start up the unit when the second load of wash
is entering the final extract cycle. Flatwork may
be put into carts from the washer and sorted out
as desired.
Be aware that flatwork that sits overnight or
longer will have uneven MR, and the operating
speed must be adjusted accordingly.
TOC
INDEX
Summary of Contents for Comet Executive Exec-56-G
Page 1: ...INSTRUCTION MANUAL COMET EXECUTIVE Gas Heated Flatwork Ironer...
Page 42: ......
Page 58: ......
Page 80: ......
Page 164: ......
Page 166: ...SC 2 Motor Circuit 115V 1 Phase SC TOC INDEX TOC...
Page 168: ...SC 4 Motor Circuit 230V 1 Phase SC TOC INDEX TOC...
Page 170: ...SC 6 Motor Circuit 230V 3 Phase SC TOC INDEX TOC...
Page 172: ...SC 8 Motor Circuit 415V 3 Phase SC TOC INDEX TOC...
Page 174: ...SC 10 Motor Circuit 460V 3 Phase SC TOC INDEX TOC...
Page 176: ...SC 12 Main Electrical Panel 115V 1 Phase SC TOC INDEX TOC...
Page 178: ...SC 14 Main Electrical Panel 230V 1 Phase SC TOC INDEX TOC...
Page 180: ...SC 16 Main Electrical Panel 230V 3 Phase SC TOC INDEX TOC...
Page 182: ...SC 18 Main Electrical Panel 460V 3 Phase SC TOC INDEX TOC...
Page 184: ......
Page 185: ...TOC INDEX...
Page 186: ......
Page 187: ...TOC INDEX...
Page 188: ......
Page 189: ...TOC INDEX...
Page 190: ......
Page 192: ......
Page 194: ......
Page 196: ......
Page 197: ...304500 1a TOC INDEX MB TOC...
Page 198: ...TOC INDEX MB TOC...
Page 199: ...TOC INDEX MB TOC...
Page 200: ...TOC INDEX MB TOC...
Page 221: ...3045069 TOC INDEX MB TOC...
Page 222: ...TOC INDEX MB TOC...
Page 223: ...TOC INDEX MB TOC...
Page 224: ...TOC INDEX MB TOC...
Page 229: ...TOC INDEX MB TOC...
Page 230: ...TOC INDEX MB TOC...
Page 231: ...TOC INDEX MB TOC...
Page 232: ...TOC INDEX MB TOC...
Page 236: ......
Page 238: ......
Page 244: ......