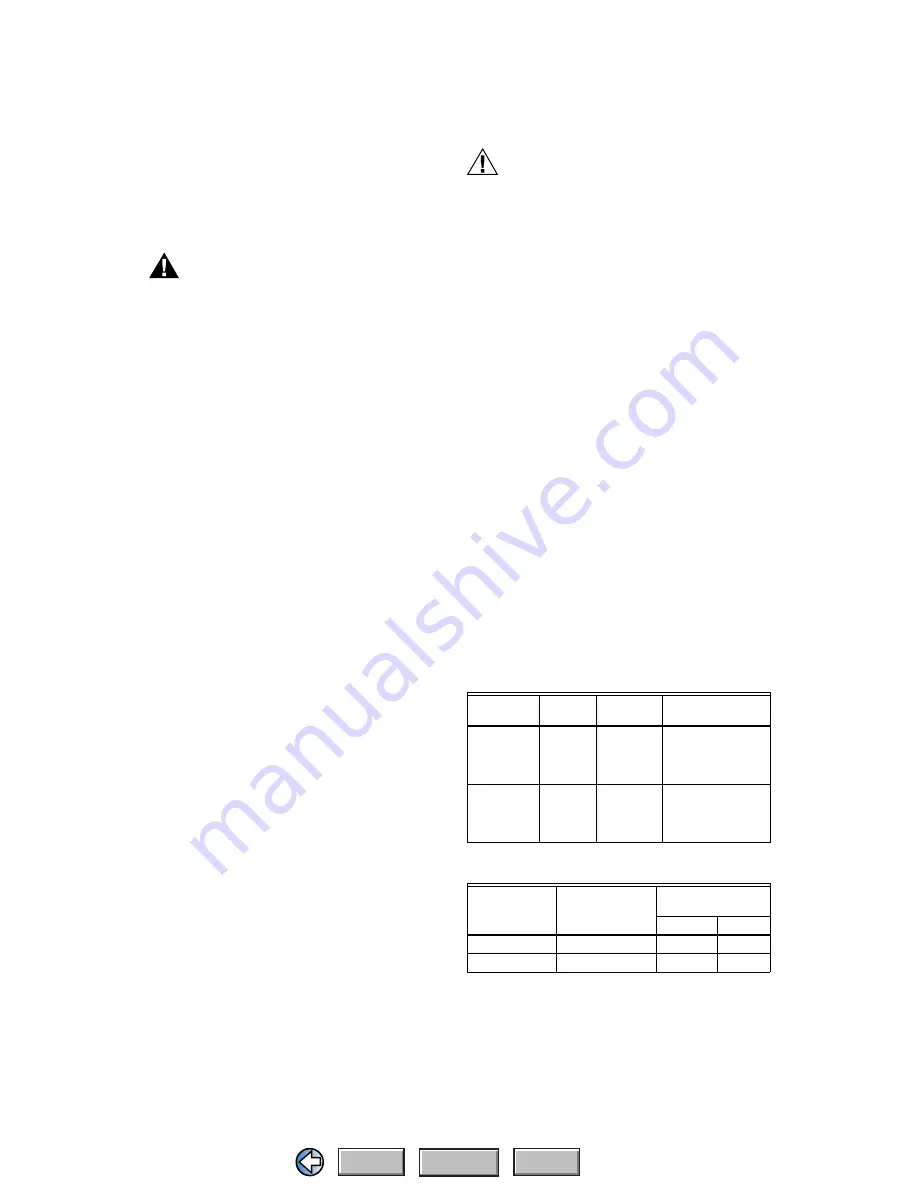
S8600, S8610, S8660, S8670 INTERMITTENT PILOT MODULE
3
69-0463—01
2.
Exposure to water, dirt, chemicals, and heat can
damage the module or the gas control and shut
down the control system. A NEMA 4 enclosure can
reduce exposure to environmental contaminants.
See Electronic Ignition Service Manual, form
70-6604.
The maintenance program should include regular
checkout of the system as outlined under CHECKOUT,
page 11.
WARNING
Fire or Explosion Hazard. Can cause severe
injury, death or property damage.
Do not attempt to take the module apart or to
clean it. Improper reassembly and cleaning may
cause unreliable operation.
Maintenance frequency must be determined individually
for each application. Some considerations are:
•
Cycling frequency.
Appliances that may cycle more
than 20,000 times annually should be checked
monthly.
•
Intermittent use.
Appliances that are used seasonally
should be checked before shutdown and again before
the next use.
•
Consequence of unexpected shutdown.
Where the
cost of an unexpected shutdown would be high, the
system should be checked more often.
•
Dusty, wet, or corrosive environment.
Since these
environments can cause the controls to deteriorate
more rapidly, the system should be checked more
often.
Any control should be replaced if it does not perform
properly on checkout or troubleshooting. In addition,
replace any module if it is wet or looks like it has ever
been wet. Protective enclosures as outlined under
"Planning the Installation" are recommended regardless
of checkout frequency.
Mount Ignition Module
Select a location close enough to the burner to allow a
short 3 ft. (0.9 m) max. direct cable route to the igniter.
Ambient temperature at the module must be within the
range listed under APPLICATION, page 1. The module
must be protected from water, moisture, corrosive
chemicals and excessive dust and grease.
We recommend mounting the module with the terminals
down to protect them from dripping water and dust. It can
also be mounted with the terminals on either side. DO
NOT MOUNT with the terminals pointing up. Fasten
securely with four No. 6-32 machine or No. 8 sheetmetal
screws.
Mount the System Controls
Mount any required controls, such as the gas control,
spark igniter, flame sensor, thermostat, limit and
transformer according to manufacturer’s instructions.
Wire the System
CAUTION
Electrical Shock Hazard.
Can cause severe injury, death or property
damage.
1.
Check the wiring diagram furnished by the
appliance manufacturer, if available, for circuits
differing from the wiring hookups shown in this
publication. Carefully follow any special instructions
affecting the general procedures outlined below.
2.
Disconnect the power supply before making wiring
connections to prevent electrical shock or
equipment damage.
IMPORTANT
1. As shown in the wiring diagrams, a common
ground is required on:
• The pilot burner mounting bracket, and the GND
(BURNER) terminal on the ignition module.
• Failure to use the GND (BURNER) terminal may
result in intermittent loss of spark and/or loss of
flame current sensitivity.
2. Make sure the transformer has adequate VA.
The ignition module requires at least 0.2A at 24
Vac. Add the current draws of all other devices in
the control circuit, including the pilot and main
valves in the gas control, and multiply by 24 to
determine the total VA requirement of these
components. Add this total to 4.8 VA (for the
ignition module). The result is the minimum
transformer VA rating. Use a Class II transformer
if replacement is required.
Connect Ignition Cable
Use Honeywell ignition cable or construct an ignition
cable that conforms to suitable national standards such as
Underwriters Laboratories Inc. (See Tables 2 and 3).
Table 2. Honeywell Preassembled Ignition Cables
(UL Style 3257).
Table 3. Recommended Ignition Cable for Field
Assembly
.
Cable must be no longer than 36 in. (0.9 m). To construct
a cable, fit one end of ignition cable with ¼ in. diameter
Rajah connector receptacle and the other with a ¼ in.
female quick connect. Protect both ends with insulated
boots.
Cable Part
Number
Length
Module
End
Igniter
End
394800-30 30 in.
(762 mm)
1/4 in.
quick
connect,
insulated
Rajah connector
receptacle, 90 deg.
rubber boot
394801-30 30 in.
(762 mm)
1/4 in.
quick
connect,
insulated
Rajah connector
receptacle, straight
rubber boot
Cable Type
Voltage Rating
(rms)
Temperature
Rating
C
F
UL Style 3217 10,000
150
302
UL Style 3257 10,000
250
484
69-0463-1.fm Page 3 Wednesday, December 19, 2007 1:22 PM
TOC
INDEX
MB-TOC
Summary of Contents for Comet Executive Exec-56-G
Page 1: ...INSTRUCTION MANUAL COMET EXECUTIVE Gas Heated Flatwork Ironer...
Page 42: ......
Page 58: ......
Page 80: ......
Page 164: ......
Page 166: ...SC 2 Motor Circuit 115V 1 Phase SC TOC INDEX TOC...
Page 168: ...SC 4 Motor Circuit 230V 1 Phase SC TOC INDEX TOC...
Page 170: ...SC 6 Motor Circuit 230V 3 Phase SC TOC INDEX TOC...
Page 172: ...SC 8 Motor Circuit 415V 3 Phase SC TOC INDEX TOC...
Page 174: ...SC 10 Motor Circuit 460V 3 Phase SC TOC INDEX TOC...
Page 176: ...SC 12 Main Electrical Panel 115V 1 Phase SC TOC INDEX TOC...
Page 178: ...SC 14 Main Electrical Panel 230V 1 Phase SC TOC INDEX TOC...
Page 180: ...SC 16 Main Electrical Panel 230V 3 Phase SC TOC INDEX TOC...
Page 182: ...SC 18 Main Electrical Panel 460V 3 Phase SC TOC INDEX TOC...
Page 184: ......
Page 185: ...TOC INDEX...
Page 186: ......
Page 187: ...TOC INDEX...
Page 188: ......
Page 189: ...TOC INDEX...
Page 190: ......
Page 192: ......
Page 194: ......
Page 196: ......
Page 197: ...304500 1a TOC INDEX MB TOC...
Page 198: ...TOC INDEX MB TOC...
Page 199: ...TOC INDEX MB TOC...
Page 200: ...TOC INDEX MB TOC...
Page 221: ...3045069 TOC INDEX MB TOC...
Page 222: ...TOC INDEX MB TOC...
Page 223: ...TOC INDEX MB TOC...
Page 224: ...TOC INDEX MB TOC...
Page 229: ...TOC INDEX MB TOC...
Page 230: ...TOC INDEX MB TOC...
Page 231: ...TOC INDEX MB TOC...
Page 232: ...TOC INDEX MB TOC...
Page 236: ......
Page 238: ......
Page 244: ......