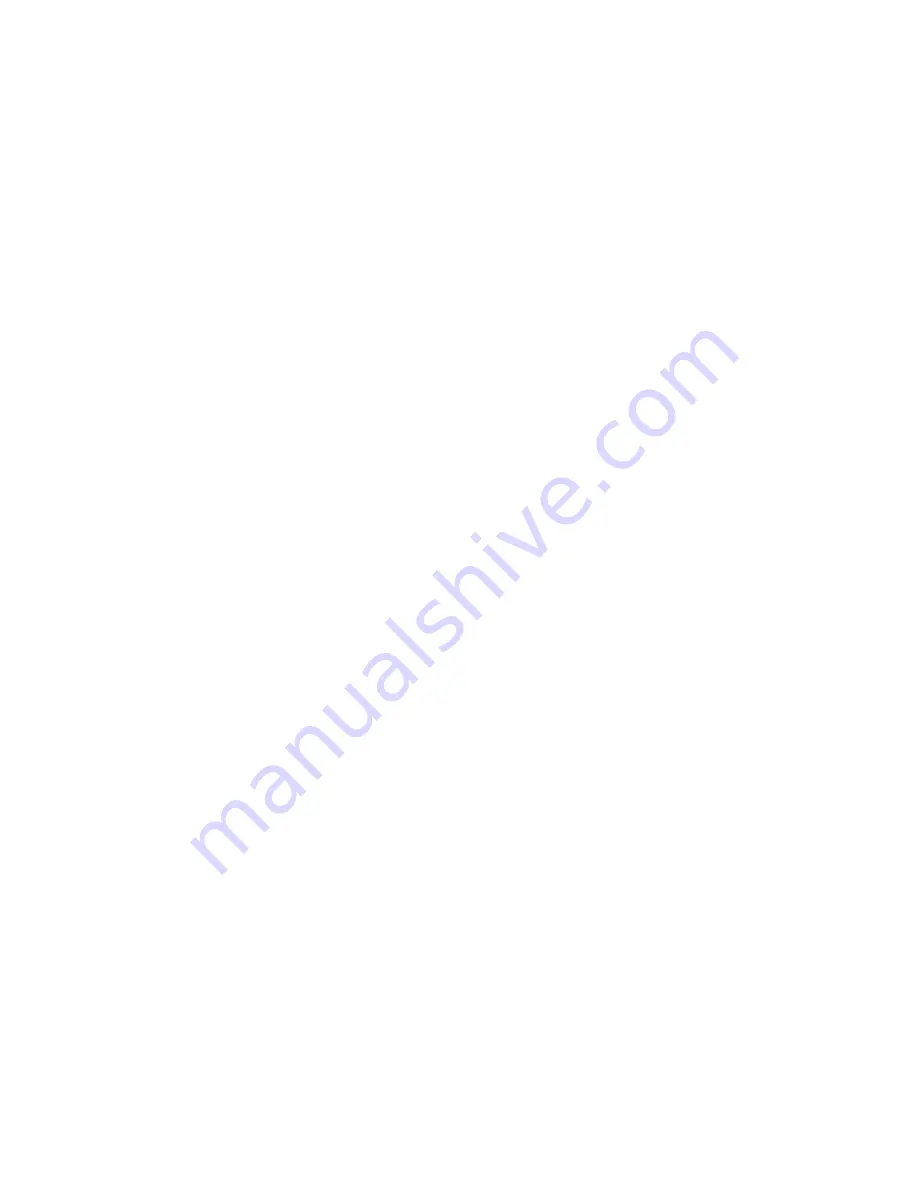
- 13 -
Periodic removal of accumulated dirt and dust
from the inside of the generator, using com-
pressed air. Do not aim the air jet directly onto
the electrical components, in order to avoid
damaging them.
Make periodical inspections in order to individ-
uate worn cables or loose connections that are
the cause of overheating.
Periodical revision inspection of the machines
has to be done once in a half of year by an au-
thorised staff in accord with EN 331500, 1990
and EN 056030, 1993.
WIRE FEED
Great attention has to be paid to the feeding mech-
anism, especially to the sheaves and the space
around them. During the wire feeding, copper coat-
ing peels off and small fillings fall off, which are
either brought into the spring or pollute the inner
space of feeding mechanism. Regularly remove and
store up dirt and dust from the inner part of wire
store and feeding mechanism.
WELDING TORCH
The welding torch has to be regularly maintained
and worn-out parts have to be exchanged on time.
The most stressed parts are the flow drawing die,
the gas tube, the pipe of the torch, the spring for
leading the wire, the coaxial cable and the button of
the torch.
The flow drawing leads welding current into wire and
at the same time wire is directed to the point of
welding. It has service life from 3 to 20 welding
hours (according to the producer), which depends on
the quality of material of drawing die (Cu or CuCr),
the quality and surface finish of wire, welding pa-
rameters and service. The exchange of drawing die is
recommended after the worning-out of drawing die
hole to 1.5 multiple of wire diameter. After each
installing and exchange it is recommended to spray
the drawing die and its thread with separating spray.
The gas tube leads gas which protects the arc and
molten pool. The spatter of metal clogs the tube and
it is necessary to clean it regularly to secure good and
uniform flow of gas and to avoid short-circuit be-
tween the drawing die and the tube. A short-circuit
can make damage to the rectifier! The speed of clog-
ging the tube depends particularly on good adjust-
ment of welding process.
The spatter of metal is easily removed after spraying
the gas tube with separating spray.
After these precautions, spatter falls out partially,
though it is necessary to remove it every 10 - 20
minutes from the space between the tube and draw-
ing die with non-metallic rod by mild pounding.
According to the current and rate of work you need
to take off the gas tube twice of 5 times during the
shift and to clear it thoroughly, including channels of
the spacer, which serve as gas inlet. You are not
allowed to pound with the gas tube since its insulat-
ing compound can be damaged.
The spacer is also exposed to the effects of the spat-
ter and heat stress. Its service life is 30 - 120 welding
hours (according to the producer).
Time intervals of changing the springs depend on the
wire purity and maintenance of the feeding mecha-
nism and adjustment of the trust of feed sheaves.
Once a week it has to be cleaned with trichloroeth-
ylene and blown through with compressive air. In the
case of high working-out or its clogging the spring
has to be exchanged.
The pointing out of any difficulties
and their elimination
The supply line is attributed with the cause of the
most common difficulties. In the case of breakdown,
proceed as follows:
1.
Check the value of the supply voltage
2.
Check that the power cable is perfectly con-
nected to the plug and the supply switch
3.
Check that the power fuses are not burned out
or loose
4.
Check whether the following are defective:
The switch that supplies the machine
The plug socket in the wall
The generator switch
NOTE
: Given the required technical skills necessary
for the repair of the generator, in case of breakdown
we advise you to contact skilled personnel or our
technical service department.
Side cover assembly and disassem-
bly procedure
Before removing the side covers, always discon-
nect the power supply cable plug from the
mains!
Remove the side cover partially covering the
wire feed mechanism.
Unscrew four screws of the right side cover,
then four upper screws and two screws fixing
the cover inside the space of the wire feed
mechanism.
In the assembly of the apparatus, proceed in the
opposite sequence of steps.
Summary of Contents for MW2040
Page 19: ...19 2080...