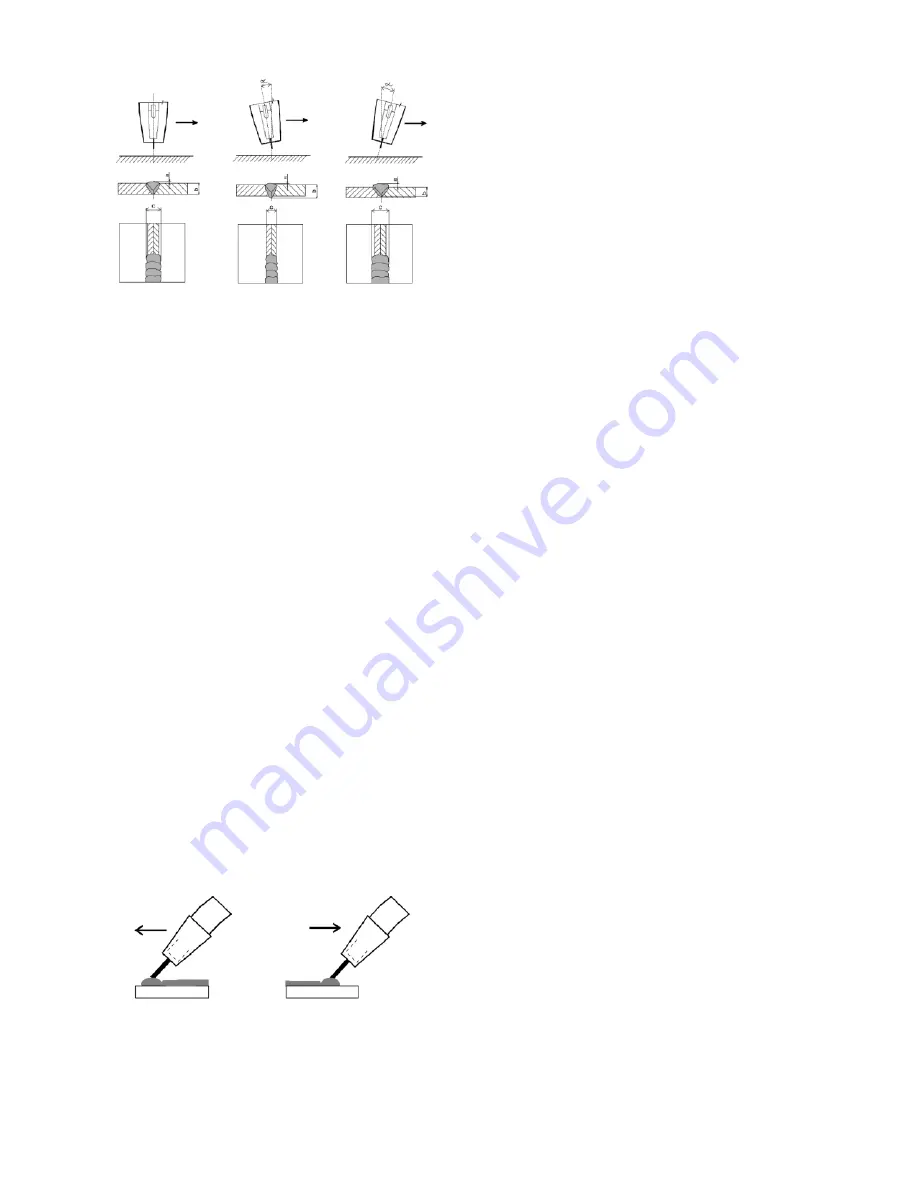
- 12 -
A
B
C
Picture 12
Gas shielded arc welding can be conducted, if the
relevant parameters are suitably selected, in all
positions
(horizontal, vertical, overhead, vertical-up
or vertical-down and across, at the same time in
these positions). In horizontal or vertical positions,
the usual gripping of the torch is in the angle of 30°.
In the case of more thick layers, the welding process
is performed by light drawing. The most suitable grip
on the torch for the optimum coverage of the weld
place by shielding gas is vertical (neutral) positioning
of the torch (Pic. 11 A). However, in this position it is
difficult to watch the welded place (it is hidden be-
hind the gas nozzle). For this reason, the torch
should be slightly tilted (Pic. 11 BC). On the other
hand, if the torch tilt is excessively off this position,
there is a danger of sucking air into the shield gas,
which might negatively influence the weld quality.
WELDING BY PRESSING AND DRAWING
Slight moves with “pressing” are used in vertical-up
welding and horizontal overhead welding (Pic. 13).
Only in vertical-down welding the torch is gripped in
the neutral or slightly “drawing” position. The verti-
cal-down welding is used mostly for thin metal
sheets, because there is a risk of a poor connection
with thick sheets; the molten metal tends to pour
down along the connection and “overtake” the weld,
particularly when the molten metal is too liquid
because of high voltage. Such method requires a
high degree of expertise and experience (Pic. 14).
Picture 13
Picture 14
Maintenance
WARNING:
Before carrying out any inspection of the
inside of the generator, disconnect the system from
the supply.
In planning of maintenance procedures, the level
and circumstances of the apparatus usage must be
taken into account. Careful handling and preventive
maintenance helps to avoid unnecessary failures and
defects.
If required by the apparatus working conditions,
the inspection and maintenance intervals must be
shortened. If the apparatus is used in a very dusty
environment (conduction dust), then intervals will
be as short as twice a month.
REGULAR MAINTENANCE AND INSPECTIONS
Conduct the inspections according to the relevant
Czech Standard (EN 60974-4.). Before any use of the
apparatus, check the conditions of the welding and
power supply cables. Do not use damaged cables!
Visual inspections include:
1.
Torch, welding current return clamp
2.
Power supply network
3.
Welding circuit
4.
Covers
5.
Controlling and indicating elements
6.
Apparatus condition in general
EVERY HALF A YEAR
Remove the plug from the socket outlet and wait for
two minutes (to allow for discharging of capacitors
inside the apparatus). Then remove the cover of the
apparatus. Clean all internal power supply connec-
tions from dust and dirt. Where they are loose,
tighten them.
Clean all internal parts of the apparatus from dust
and dirt using a soft brush of vacuum cleaner.
NOTE:
Be careful when using compressed air in order
to not damage any parts.
Never use any solvents or diluents (such as acetone,
etc.); plastic material and front panel lettering could
be damaged in such procedures.
Only sufficiently qualified technicians (electrical
engineers) may repair the apparatus.
SPARE PARTS
Original spare parts have been specially designed for
our equipment. The use of non-original spare parts
may cause variations in performance or reduce the
foreseen level of safety. We decline all responsibility
for the use of non-original spare parts.
THE GENERATOR
As these systems are completely static, proceed as
follows:
Summary of Contents for MW2040
Page 19: ...19 2080...