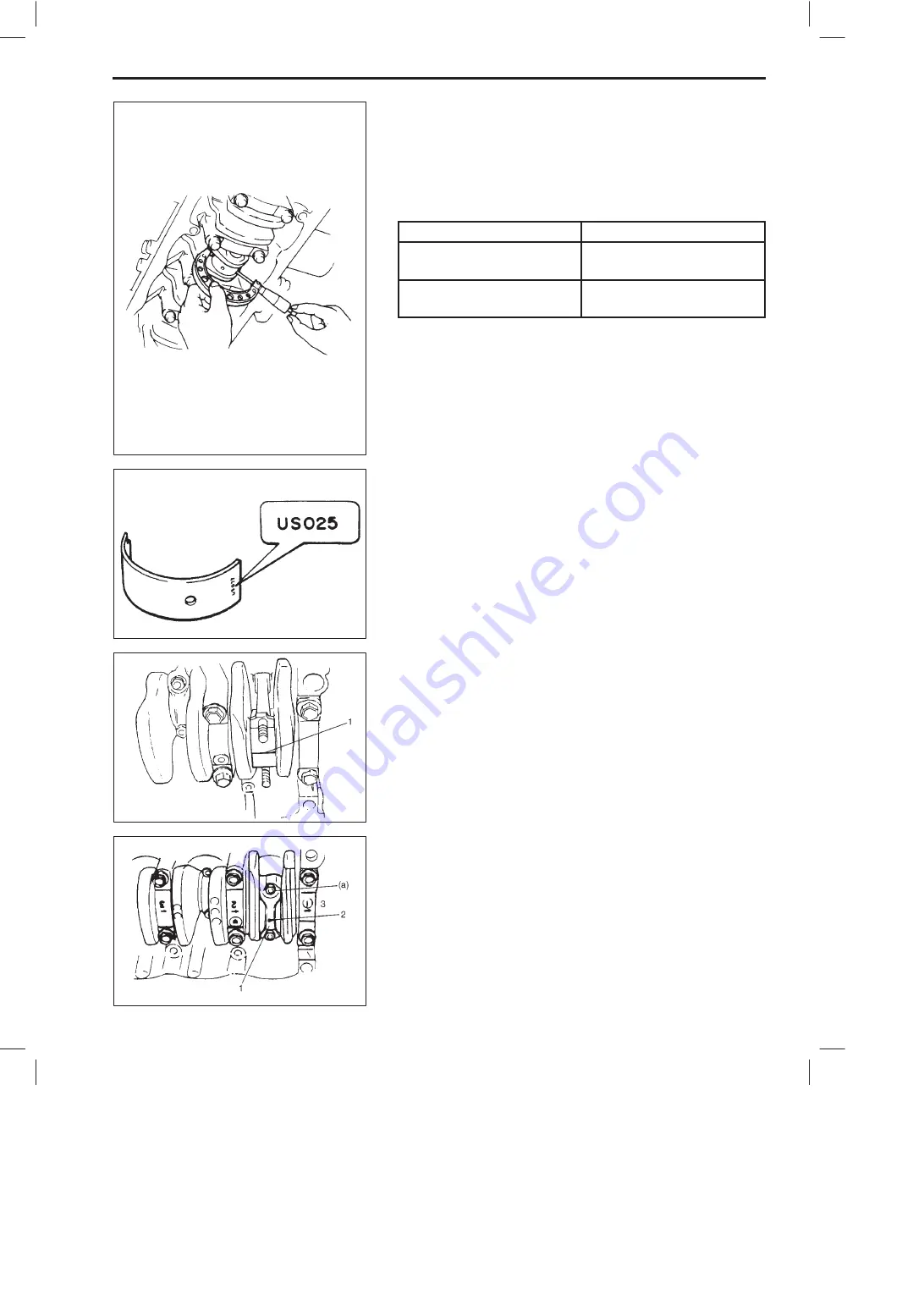
Crank Pin and Connecting Rod Bearings
Inspect crank pin for uneven wear or damage. Measure crank
pin for out-of-round or taper with a micrometer. If crank pin is
damaged, or out-of-round or taper is out of limit, replace crank-
shaft or regrind crank pin to undersize and use undersize bear-
ing.
Out-of-round and taper limit: 0.01 mm (0.0004 in.)
Rod bearing:
Inspect bearing shells for signs of fusion, pitting, burn or flaking
and observe contact pattern. Bearing shells found in defective
condition must be replaced.
Two kinds of rod bearing are available; standard size bearing
and 0.25 mm undersize bearing. To distinguish them, 0.25 mm
undersize bearing has the stamped number (US025) on its
backside as indicated in figure, but standard size one has no
number.
Rod bearing clearance:
1) Before checking bearing clearance, clean bearing and crank
pin.
2) Install bearing in connecting rod and bearing cap.
3) Place a piece of gaging plastic (1) to full width of crankpin as
contacted by bearing (parallel to crankshaft), avoiding oil
hole.
4) Install rod bearing cap (1) to connecting rod.
When installing cap, be sure to point arrow mark (2) on cap to
crankshaft pulley side (3), as shown in figure. After applying en-
gine oil to rod bolts, tighten cap nuts to specified torque. DO
NOT turn crankshaft with gaging plastic installed.
Tightening Torque
(a): 35 N
.
m (3.5 kg-m, 25.5 lb-ft)
ENGINE MECHANICAL
6A1-55
SH410
Connecting rod bearing size
Crank pin diameter
Standard
41.982 – 42.000 mm
(1.6528 – 1.6535 in.)
0.25 mm (0.0098 in.)
undersize
41.732 – 41.750 mm
(1.6430 – 1.6437 in.)