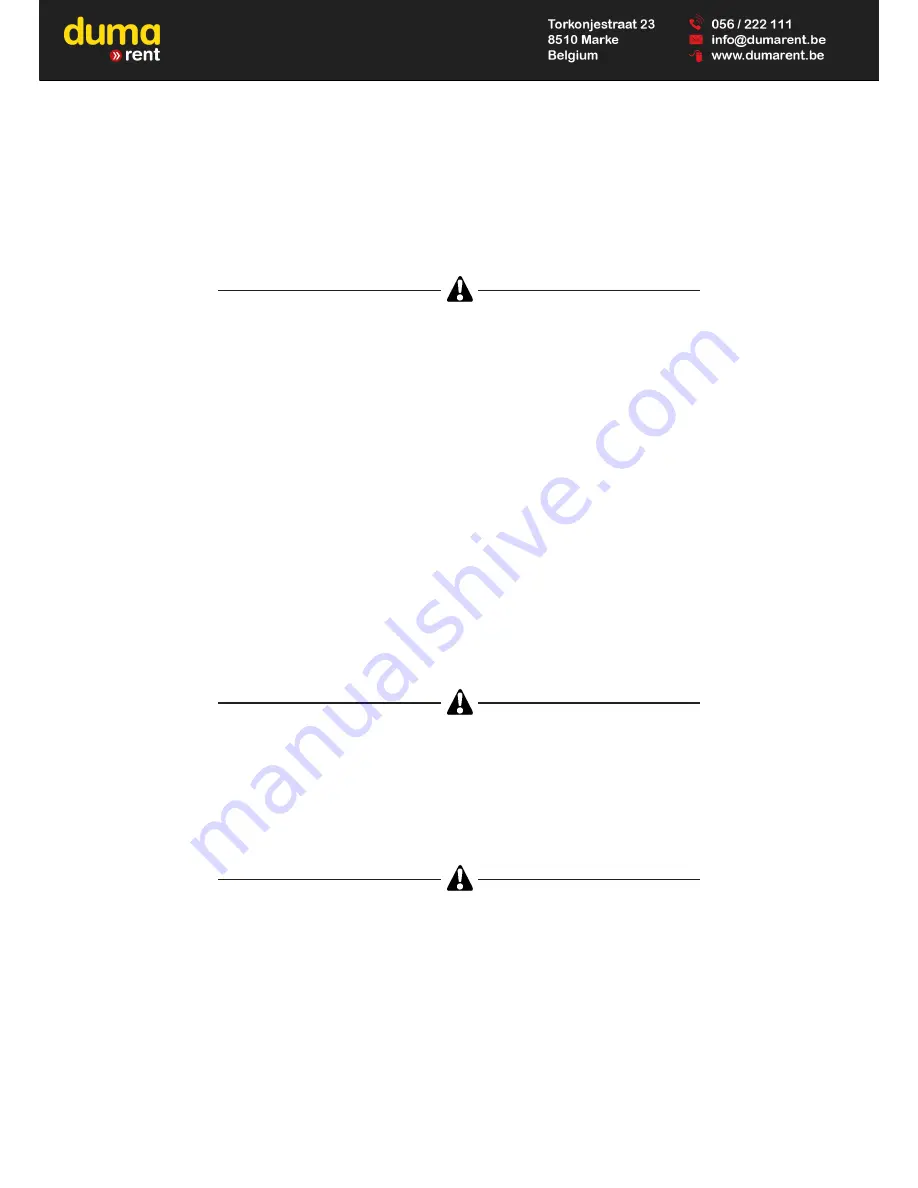
1 - 10
E - STOPPING THE LIFT TRUCK
SAFETY NOTICE
- Before stopping the lift truck after a long working period, leave the I.C. engine idling for a few moments, to allow the
coolant liquid and oil to lower the temperature of the engine and transmission.
Do not forget this precaution, in the event of frequent stops of the engine, or else the temperature of certain parts will
rise significantly due to the stopping of the cooling system, with the risk of badly damaging such parts.
- Never leave the ignition key in the lift truck when the lift truck is unattended.
- When the lift truck is stationary, place the forks or attachment on the ground, apply the parking brake and put the
forward/reverse lever in neutral.
- If the driver has to leave his cab, even for a moment, it is essential apply the parking brake and put the forward/reverse
lever in neutral.
- Make sure that the lift truck is not stopped in any position that will interfere with the traffic flow and at less than one
meter from the track of a railway.
- In the event of prolonged parking on a site, protect the lift truck from bad weather, particularly from frost (Check the
level of antifreeze), close the rear windows, lock the cab doors and ensure that the hood is properly secured.
INSTRUCTIONS
- Park the lift truck on flat ground or on an incline lower than 15 %.
- Release the accelerator pedal and stop the lift truck.
- Place the forward/reverse lever in neutral.
- Apply the parking brake.
- Lower the forks or attachment to rest on the ground.
- Stop the engine with the ignition switch.
- Remove the pressure in the hydraulic circuits by using the hydraulic controls.
- Remove the ignition key.
- Check the closing and locking of doors, windows and hood.
Before leaving your driver's cabin, ensure that you have carried out all operations for stopping the lift truck, for your
safety and the safety of others.
F - DRIVING THE LIFT TRUCK ON THE PUBLIC HIGHWAY
SAFETY INSTRUCTIONS
- When driving a lift truck on roads open to public traffic, observe the provisions of the Highway Code.
- Lift truck drivers, driving on the public highway, must abide by the general provisions relative to highway traffic.
- The lift truck must conform to the provisions of the Highway Code. If necessary, optional solutions exist, consult your
dealer.
Transport of loads on the public highway is forbidden and attachments mounted on the lift truck must be fitted with
equipment in accordance with regulations or else dismounted.
Summary of Contents for MSI 40
Page 2: ......
Page 4: ......
Page 6: ......
Page 7: ...1 1 1 OPERATING AND SAFETY INSTRUCTIONS 1 OPERATING AND SAFETY INSTRUCTIONS...
Page 8: ...1 2...
Page 11: ...1 5...
Page 23: ...1 17...
Page 28: ...1 22...
Page 29: ...2 1 2 DESCRIPTION 2 DESCRIPTION...
Page 30: ...2 2...
Page 31: ...2 3...
Page 45: ...2 17...
Page 46: ...2 18 DIMENSIONS AND LOAD CHART MSI 40 MSI 50...
Page 71: ...3 1 3 MAINTENANCE 3 MAINTENANCE...
Page 72: ...3 2...
Page 79: ...3 9...
Page 110: ...4 2...