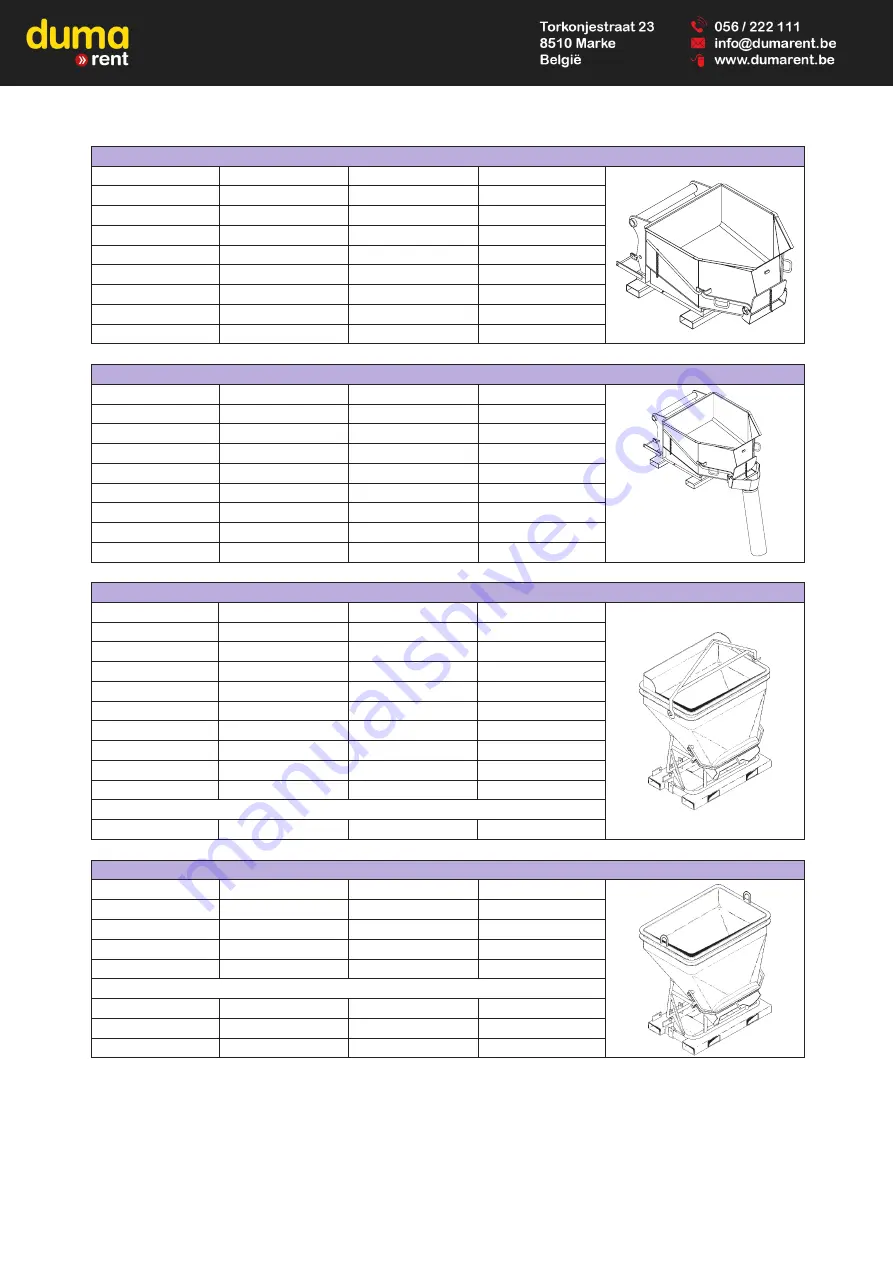
4 - 18
CONCRETE BUCKET (ADAPTABLE ON FORKS)
BB 500 S4
BBH 500 S4
REFERENCE
654409
654410
Nominal load capacity
500 L/1300 Kg
500 L/1300 Kg
Width
1100 mm
1100 mm
Weight
210 Kg
230 Kg
CONCRETE BUCKET WITH SPOUT (ADAPTABLE ON FORKS)
BBG 500 S4
BBHG 500 S4
REFERENCE
654411
654412
Nominal load capacity
500 L/1300 Kg
500 L/1300 Kg
Width
1100 mm
1100 mm
Weight
210 Kg
230 Kg
SPOUT BUCKET (ADAPTABLE ON FORKS)
GL 300 S2
GL 400 S2
GL 600 S2
REFERENCE
174371
174372
174373
Nominal load capacity
300 L/660 Kg
400 L/880 Kg
600 L/1320 Kg
Weight
149 Kg
157 Kg
277 Kg
GL 800 S2
REFERENCE
174374
Nominal load capacity
800 L/1760 Kg
Weight
308 Kg
HYDRAULIC KIT TO OPEN THE SPOUT
REFERENCE
653750
SPOUT BUCKET (ADAPTABLE ON FORKS)
GL 1000 S2
GL 1500 S2
REFERENCE
174375
174376
Nominal load capacity
1000 L/2200 Kg
1500 L/3300 Kg
Weight
325 Kg
375 Kg
HYDRAULIC KIT TO OPEN THE SPOUT
REFERENCE
653750
Summary of Contents for B-E2 Series
Page 2: ......
Page 4: ......
Page 5: ...1 1 1 OPERATING AND SAFETY INSTRUCTIONS...
Page 6: ...1 2...
Page 30: ...1 26...
Page 31: ...2 1 2 DESCRIPTION 2 DESCRIPTION...
Page 32: ...2 2...
Page 47: ...2 17...
Page 65: ...2 35...
Page 75: ...3 1 3 MAINTENANCE 3 MAINTENANCE...
Page 76: ...3 2...
Page 78: ...3 4...
Page 97: ...3 23...
Page 103: ...3 29...
Page 107: ...3 33...
Page 109: ...3 35...
Page 116: ...4 2...
Page 118: ...4 4...
Page 127: ...4 13...