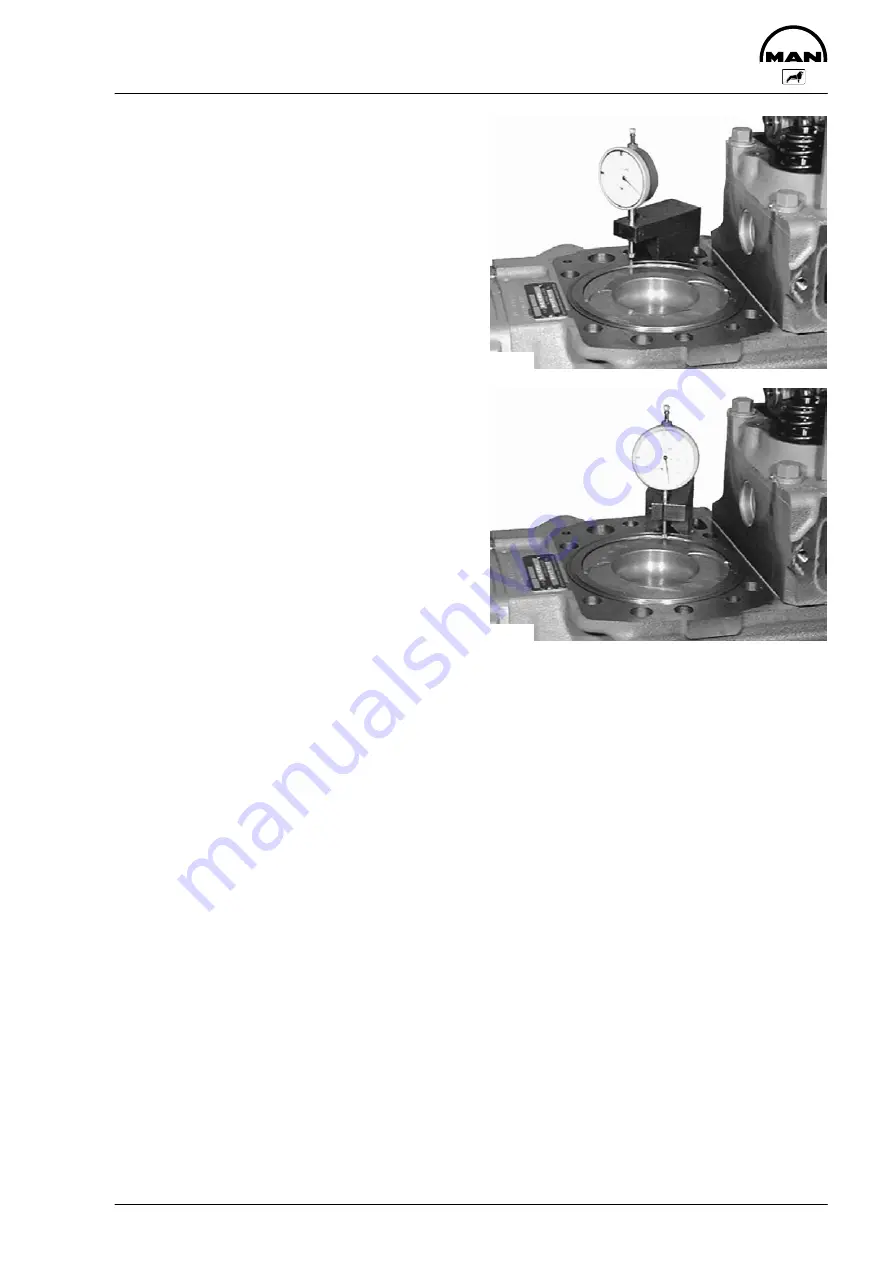
1
2
Measuring piston protrusion
115
Fig. 1
Remove cylinder heads.
Move piston to be measured to TDC.
Apply dial gauge in holder to crankcase sealing
face.
Set dial gauge to - 0 -.
Fig. 2
Carefully slew dial gauge holder round, lifting the
dial gauge tip as you do so.
Lower dial gauge tip on to piston crown and read
off piston protrusion.
3577
3578
Summary of Contents for D 2866 LE 401
Page 1: ......
Page 17: ...Engine views D 2866 LE401 16...
Page 18: ...Engine views D 2866 LE401 17...
Page 19: ...Cross section of engine 18...
Page 20: ...Longitudinal section 19...
Page 124: ...123 Special tools...
Page 125: ...Special tools 124 2 3 4 5 6 7 9 1 8 6 1 6 2 6 3...
Page 129: ...Special tools 128 21 22 23 25 25 2 24 25 1 26 27 1 27 2 27 20 1 19 2 19 1 20 2 19 20...
Page 131: ...Special tools 130 29 28 30...
Page 138: ......