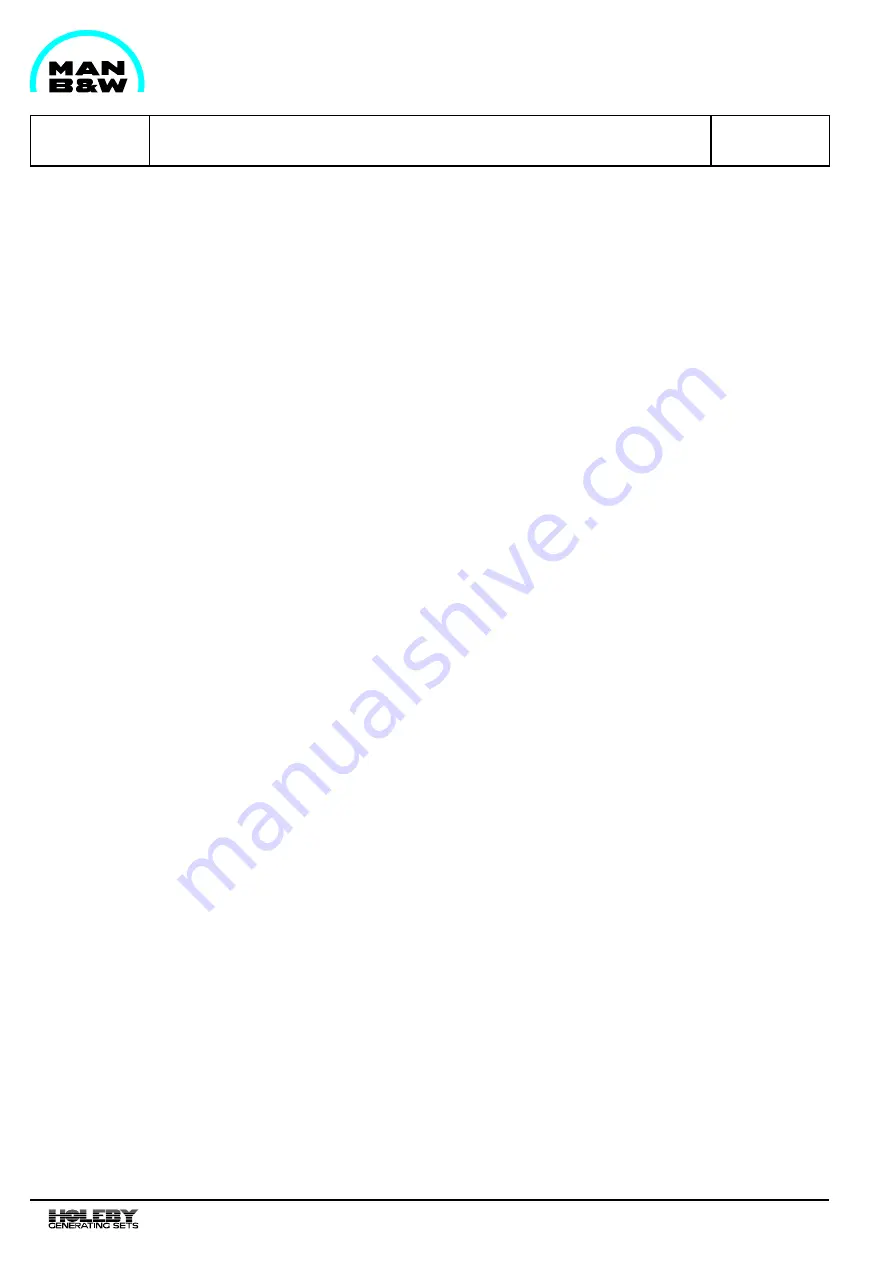
08028-0D\H5250\94.08.12
B 13 00 0
1609571-3.4
Page 2 (5)
General
00.11
If deionized or distilled water cannot be obtained,
normal drinking water can be used in exceptional
cases. If so, the total hardness of the water must not
exceed 9° dH (German hardness degrees). The
chloride, chlorine, sulphate, and silicate contents are
also to be checked. These contents should not
exceed the following values:
Chloride
50 ppm
(50 mg/litre)
Chlorine
10 ppm
(10 mg/litre)
Sulphate
100 ppm
(100 mg/litre)
Silicate
150 ppm
(150 mg/litre)
There should be no sulphide and ammonia content.
Rain water must not be used, as it may be heavily
contaminated.
It should be noted that softening of water does not
reduce its sulphate and chloride contents.
Corrosion Inhibitors
To protect freshwater cooling systems in marine
diesel engines against corrosion, various types of
inhibitors are available.
Generally, only nitrite-borate based inhibitors
are recommended.
A number of the products marketed by major compa-
nies are specified on the enclosed list, together with
the necessary dosages and admixing procedures.
We recommend that these directions are strictly
observed.
Treatment of the cooling water with inhibting oils is
not recommended, as such treatment involves the
risk of oil adhering to the heat transmitting surfaces.
Chromate inhibitors must not be used in plants
connected to a freshwater generator.
Evaporated cooling water is to be replaced with
noninhibited water, whereas a loss of water through
leakage must be replaced with inhibited water.
When overhauling individual cylinders, a new dos-
age of inhibitor must, if necessary, be added im-
mediately after completing the job.
Checking of the Cooling Water System and
the Sooling Water during Service
If the cooling water is contaminated during service,
sludge or deposits may form. The condition of the
cooling water system should therefore be regularly
checked, especially if deionized or distilled water is
not used. If deposits are found in the cooling spaces,
these spaces or, if necessary, the entire system
should be cleaned.
According to experience, a zinc galvanized coating
in the freshwater cooling system is often very sus-
ceptible to corrosion, which results in heavy for-
mation of sludge, even if the cooling water is cor-
rectly inhibited. The initial descaling with acid will, to
a great extent, remove the galvanized coating. Gen-
erally, therefore, we advise against the use of galva-
nized piping in the freshwater cooling system.
The quality of the cooling water is to be checked
regularly, if possible once a week. Basically the
inhibitor concentration, the pH value and the chloride
concentration should be in accordance with limits
stated by inhibitor manufacturer. For this purpose
the inhibitor manifactures normally supply simple
test kits.
As a general guidance values the pH value should be
7-10 measured at 20° C and the chloride concentra-
tion should not exceed 50 ppm (50 mg/litre).
The water sample for these tests is to be taken from
the circulating system, and not from the expansion
tank or the pipe leading to it.
The concentration of inhibitor must under no
circumstances be allowed to fall below that re-
commended by the producer, as this would in-
crease the risk of corrosion.
A clear record of all measuring results should be
kept, so that the actual condition and trend of the
system may be currently ascertained and evaluated.
A sudden or gradual increase in the chloride content
of the cooling water may be indicative of salt water
leakages. Such leakages are to be traced and repai-
red at the first opportunity.
Freshwater System Treatment
Summary of Contents for L28/32H
Page 4: ......
Page 5: ...Introduction I 00...
Page 6: ......
Page 8: ......
Page 10: ......
Page 11: ...Designation of Cylinders In Line 98 19 1607568 0 1 Page 1 1 I 00 15 0...
Page 12: ......
Page 18: ......
Page 19: ...General information D 10...
Page 20: ......
Page 22: ......
Page 24: ......
Page 26: ......
Page 30: ......
Page 32: ......
Page 34: ......
Page 36: ......
Page 37: ...Basic Diesel Engine B 10...
Page 38: ......
Page 44: ......
Page 45: ...99 40 B 10 01 1 L28 32H Cross Section 1607528 5 2 Page 1 1...
Page 46: ......
Page 48: ......
Page 50: ......
Page 52: ......
Page 54: ......
Page 58: ......
Page 59: ...1607566 7 1 Page 1 1 Engine Rotation Clockwise B 10 11 1 General 98 18...
Page 60: ......
Page 61: ...Fuel Oil System B 11...
Page 62: ......
Page 68: ......
Page 72: ......
Page 74: ......
Page 76: ......
Page 79: ...Lubrication Oil System B 12...
Page 80: ......
Page 86: ......
Page 88: ......
Page 91: ...Cooling Water System B 13...
Page 92: ......
Page 98: ......
Page 106: ......
Page 108: ......
Page 112: ......
Page 113: ...Compressed Air System B 14...
Page 114: ......
Page 118: ......
Page 119: ...Combustion Air System B 15...
Page 120: ......
Page 124: ......
Page 126: ...Fig 1 Jet system 1639456 5 0 Page 2 2 Lambda Controller 93 44 L28 32H B 15 11 1...
Page 127: ...Exhaust Gas System B 16...
Page 128: ......
Page 136: ......
Page 140: ......
Page 142: ......
Page 144: ......
Page 146: ......
Page 147: ...Speed Control System B 17...
Page 148: ......
Page 150: ......
Page 152: ......
Page 153: ...Monitoring Equipment B 18...
Page 154: ......
Page 156: ......
Page 158: ......
Page 159: ...Safety and Control System B 19...
Page 160: ......
Page 164: ......
Page 166: ......
Page 177: ...Foundation B 20...
Page 178: ......
Page 180: ......
Page 183: ...Test running B 21...
Page 184: ......
Page 186: ......
Page 187: ...Spare Parts E 23...
Page 188: ......
Page 190: ......
Page 191: ...99 35 1607521 2 6 Page 1 1 Recommended Wearing Parts E 23 04 0 L28 32H...
Page 192: ......
Page 195: ...Tools P 24...
Page 196: ......
Page 200: ......
Page 202: ......
Page 203: ...Preservation and Packing B 25...
Page 204: ......
Page 206: ......
Page 208: ......
Page 210: ......
Page 211: ...Alternator G 50...
Page 212: ......
Page 216: ......
Page 218: ......