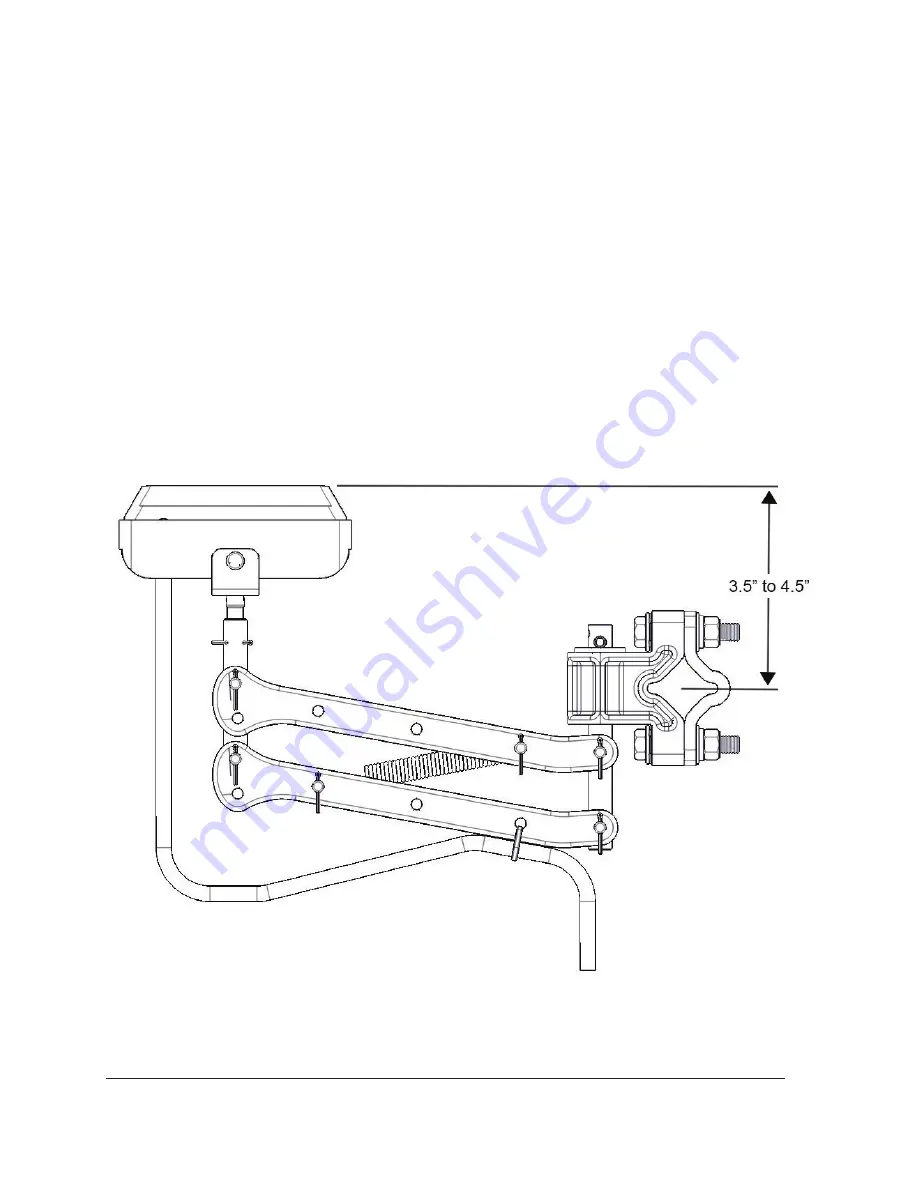
Electrification FS Conductor Bar System Instruction Manual
October 2019
Page
30
of
34
Chapter 10.0: Collectors
10.1: Mount the collector mounting post so the horizontal centerline of the post is 4”± 0.5” from the
running surface of the conductor bar.
10.1.(a):
Slide each of the collectors onto the mounting post until they are directly under the
conductor bar it is going to run in.
NOTE: When mounting tandem collectors, be sure each collector shoe is positioned in the
appropriate conductor bar.
10.1.(b):
Tighten each bolt (upper and lower) until the collector is firmly in place 10 ft-lb. (120 in-
lb.).
10.1.(c):
Termination of collector leads should be in accordance with NEC and local electrical
standards.
NOTE: Before performing any maintenance on the system, be sure that the power to the system
has been disconnected following lock-out tag-out procedures.