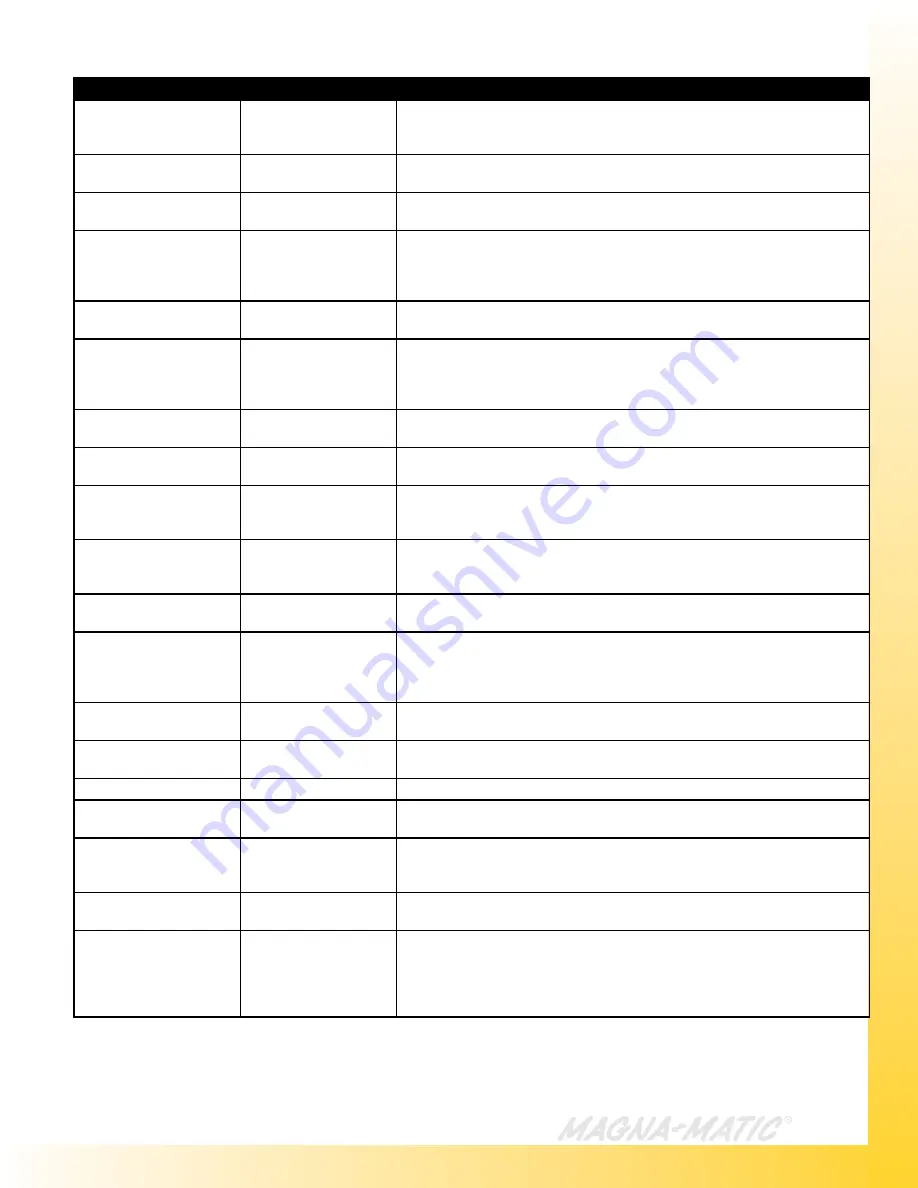
37
TROUBLESHOOTING
PROBLEM
CAUSE
SOLUTION
Motor fails to start
Fan guard bent/dam-
aged and contacting
fan.
Replace fan guard
Motor has been running,
then fails to start
Fuse or circuit breaker
tripped.
Replace fuse or reset the breaker.
Motor has been running,
then fails to start
Motor overloaded or
load jammed.
Inspect to see that the load is free. Verify amp draw of motor versus name
-
plate rating.
Motor has been running,
then fails to start
Capacitor may have
failed.
First discharge capacitor. To check capacitor, set volt-ohm meter to RX100
scale and touch its probes to capacitor terminals. If capacitor is OK, needle
will jump to zero ohms, and drift back to high. Steady zero ohms indicates a
short circuit; steady high ohms indicates an open circuit.
Motor has been running,
then fails to start
Starting switch has
failed.
See wiring diagram and connect the black wire from the motor and the black
wire from the cord to bypass the switch.
Motor runs but dies down Voltage drop
If voltage is less than 10% of the motor’s rating contact power company or
check if some other equipment is taking power away from the motor. If motor
is run using an extension cord, verify that this extension cord is properly
sized for motor’s current draw.
Motor takes too long to
accelerate
Defective capacitor
Test capacitor per previous instructions.
Motor takes too long to
accelerate
Bad bearings
Noisy or rough feeling bearings should be replaced.
Motor takes too long to
accelerate
Voltage too low.
Make sure that the voltage is within 10% of the motor’s nameplate rating.
If not, contact power company or check if some other equipment is taking
power away from the motor.
Motor overload protector
continually trips
Ambient temperature
too high.
Verify that the motor is getting enough air for proper cooling. Most motors
are designed to run in an ambient temperature of less than 40°C. (Note: A
properly operating motor may be hot to the touch.)
Start capacitors continu-
ously fail.
Voltage to motor is too
low.
Verify that voltage to the motor is within 10% of the nameplate value. If the
motor is rated 110-125 V, the deviation must be calculated from 125 V.
MAG-8200 is vibrating
Grinding wheel is out-
of-round
Dress the wheel and old lawn mower blade. Use a perfectly flat area, like
around the mounting hole. Place it in the sharpener like you would normal-
ly, and slowly apply pressure into the wheel. Do not go back and forth, just
apply even pressure, and let the wheel true itself.
MAG-8200 is vibrating
Bad motor bearings
Remove the grinding wheel, and run the MAG-8000. Inspect the motor shaft
and bearings.
MAG-8200 is vibrating
Loose pulleys or bear-
ing collars
Tighten set screws, locking agent should be used.
MAG-8200 is vibrating
Poor belt tension
Check idler pulley springs
MAG-8200 is vibrating
Bad drive shaft bear
-
ings
Check and replace the two flange bearings
MAG-8200 crank will not
adjust the wheel up or
down
Adjustment block
jammed
Inspect the guide rods for debris, or check if you are jammed at the top or
bottom of the adjustment.
Unable to remove grind-
ing wheel
Turning wrong direction
The arbor nut has left-handed threads. Turn clockwise to loosen. Use both
the arbor and spanner wrench.
Difficult to remove grind
-
ing wheel
Extremely tight, wheel
has not been changed
in a long time.
Using both the spanner and arbor wrenches, Allow the arbor wrench to
stop against the yellow body, Use a plastic hammer and tap the end of the
spanner wrench, imparting vibration will shock the nut loose. In extreme sit-
uations you can apply heat, only to the arbor nut. Last resort, you can break
the wheel off the arbor.