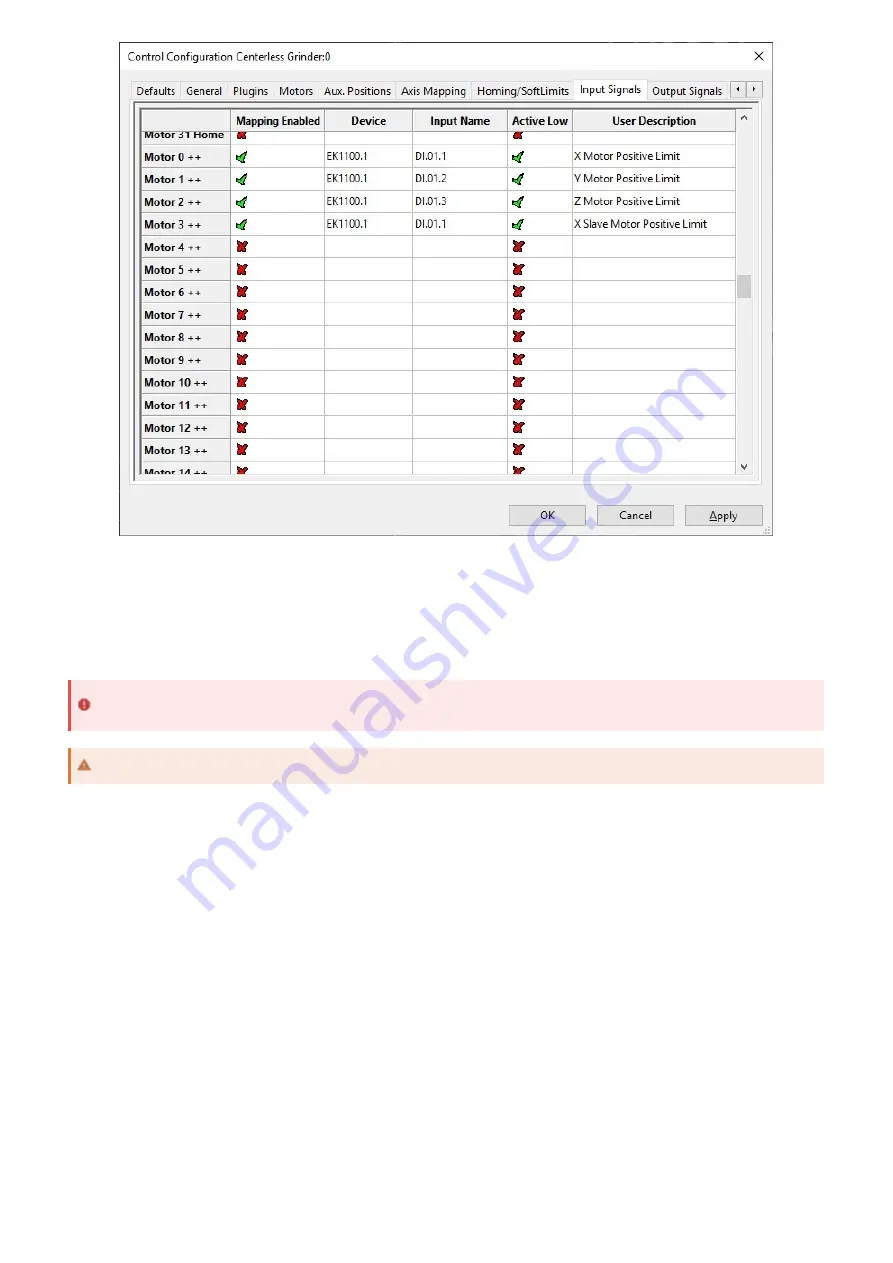
Each motor has a home signal for use during homing. If a motor is not using the Home to Switch method, then it's
signal does not need to be configured. The home signal for a motor is called Motor # Home, where # is the motor
number. The I/O point that is mapped here needs to be the one that the home switch for that motor is wired into.
Multiple motors can share a home switch input, if the machine is wired in that way. A limit switch can also function as
a home switch.
Home Switches
If these signals are not mapped correctly, the machine will not stop when the home switch is triggered during
homing.
If a limit switch is used as a home switch, then it will not disable the machine while homing.