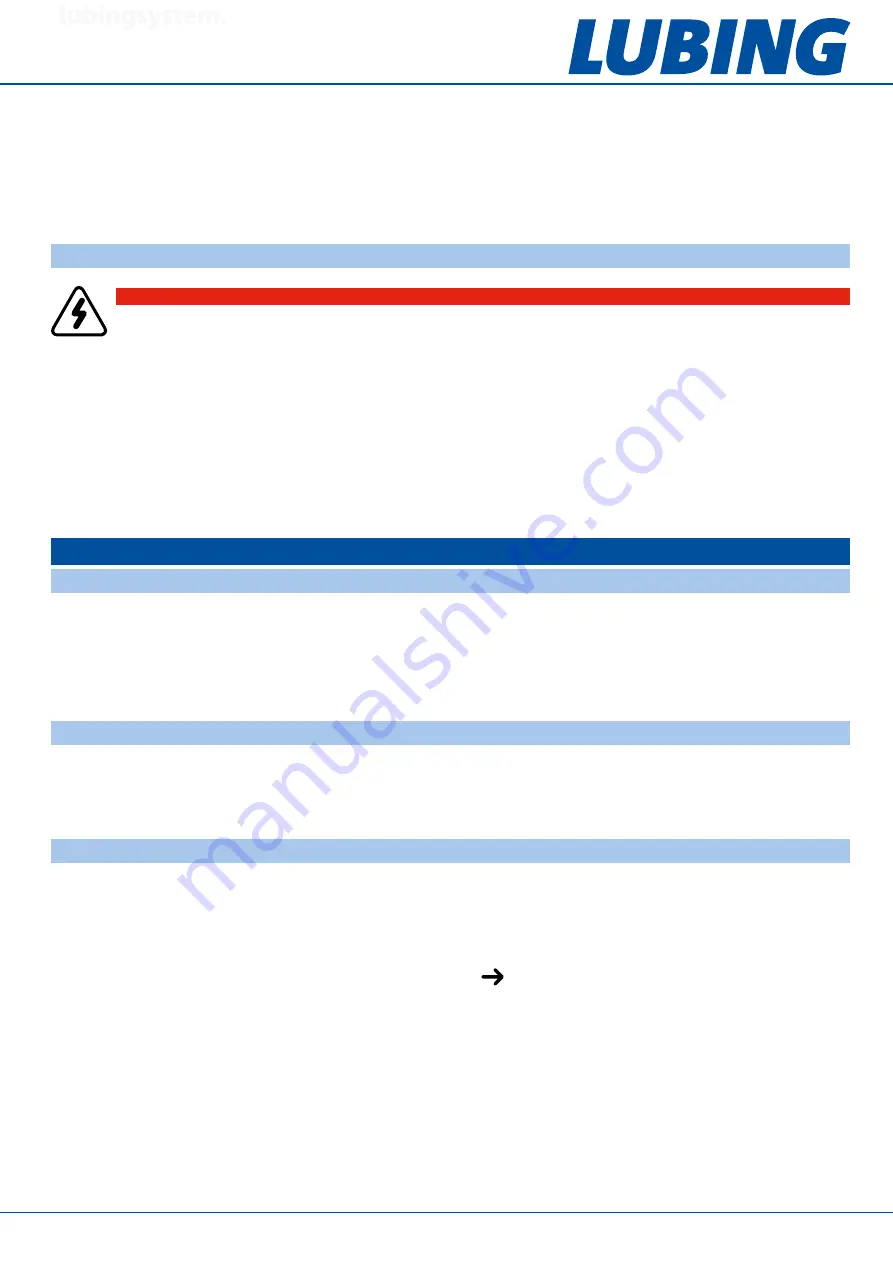
Spare part list
Floor watering system
Copyright © 2018 Lubing System - All rights reserved
8
– Non-observation of the information in the operating manual regarding transport, storage, assembly,
commissioning, operation, service and equipment of the system,
– Independent structural changes to the system,
– Defective monitoring of wear parts,
– Incorrectly performed repairs,
– Disaster due to foreign bodies and force majeure.
2.5 Electrical system
Any tasks exceeding the scope of system maintenance must only be performed by qualified staff.
Turn off the power supply and secure it against reactivation when work on the device is to be performed. Check
electrical cables for visible damage before commissioning. Replace any damaged cables before taking the device
into operation. Damaged or destroyed plug-in units must be replaced by a qualified electrician. Do not pull any
plugs from the sockets by pulling the cable. Covering electrical parts may cause high temperatures that in turn may
destroy the equipment and cause fires.
3. ASSEMBLY
3.1 Assembly information
Please read the following pages with care. The instructions in this manual shall apply to various Pad-climate-
system designs. For this reason, please select and use the sections that apply to you.
When using this manual for LUBING standard versions, please observe any changes to and/or deviations from the
scope of delivery.
3.2 Installation position in the building
The pad surface design should be designed based on the maximal required cooling. The system should be
attached to the building in order to best avoid detriments air swirls or air leaks. Additionally, the resulting air speed
should not exceed the comfort level for the animals kept.
3.3 Preparation of the attachment opening
The attachment opening should have a height of:
PAD HEIGHT (max. 2500 mm) – 77 mm
and a length of:
PAD LENGHT - 60 mm (e.g.: pad length 24000 mm
opening = 23940 mm)
DANGER!
Warning of electrical hazard!
Always interrupt power supply before performing any work on the electrical system.
lubingsystem.
com
lubingsystem.
com
lubingsystem.
com
lubingsystem.
com
lubingsystem.
com
lubingsystem.
com
lubingsystem.
com
lubingsystem.
com
lubingsystem.
com
lubingsystem.
com
lubingsystem.
com
lubingsystem.
com
lubingsystem.
com
lubingsystem.
com
lubingsystem.
com
lubingsystem.
com
lubingsystem.
com
lubingsystem.
com
lubingsystem.
com
lubingsystem.
com
com
lubingsystem.
com
lubingsystem.
com
lubingsystem.
com
lubingsystem.
com
lubingsystem.
com
lubingsystem.
com
lubingsystem.
com
lubingsystem.
com
lubingsystem.
com
lubingsystem.
com