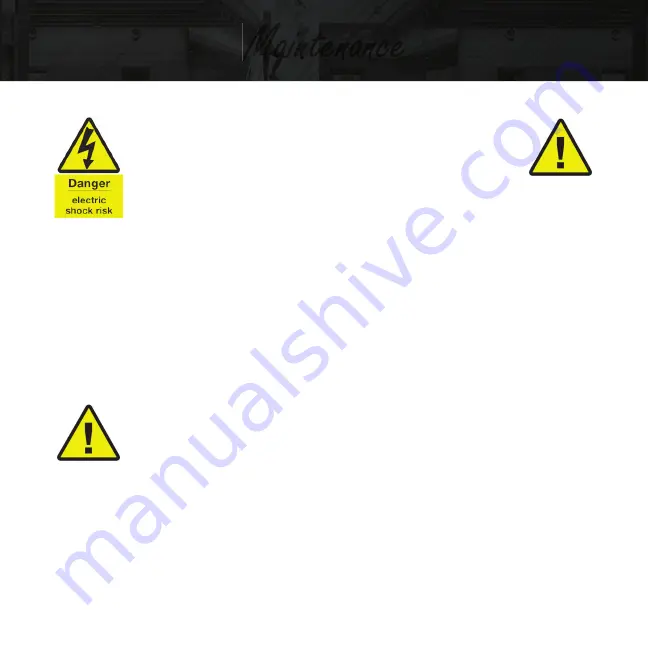
35
WARNING! RISK OF SHOCK!
WARNING! RISK OF SHOCK!
ONLY QUALIFIED PERSONNEL TO REMOVE
ONLY QUALIFIED PERSONNEL TO REMOVE
DRIVE COVER! THERE IS NO ADJUSTMENTS OR
DRIVE COVER! THERE IS NO ADJUSTMENTS OR
REPLACEMENT PARTS FOR THE USE!
REPLACEMENT PARTS FOR THE USE!
TERMINALS:
TERMINALS:
Power Terminal: 3A, 300V, 10-30 AWG Torque = 4 - 6 in/lbs
I/O Terminal: 17.5A, 300V, 12-30 AWG Torque = 5 - 8 in/lbs
POWER CORD:
POWER CORD:
Minimum 16AWG 3 Conductors rated 300VAC, use Copper Conductors
only. For permanent connection only.
WARNING! IF UNUSUAL OSCILLATING MOVEMENT IS
WARNING! IF UNUSUAL OSCILLATING MOVEMENT IS
OBSERVED, IMMEDIATELY STOP USING THE CEILING FAN
OBSERVED, IMMEDIATELY STOP USING THE CEILING FAN
AND CONTACT THE MANUFACTURER, ITS SERVICE AGENT
AND CONTACT THE MANUFACTURER, ITS SERVICE AGENT
OR SUITABLY QUALIFIED PERSONS.
OR SUITABLY QUALIFIED PERSONS.
Maintenance
Maintenance
Summary of Contents for HVAD 2020
Page 1: ...1 Installation Installation Operation Operation User Guide User Guide HVAD HVAD...
Page 10: ...10 CLEARANCES CLEARANCES...
Page 32: ...32 INPUT INPUT 120 240V 2 9 1 45A 1 PH 120 240V 2 9 1 45A 1 PH 50 60HZ 50 60HZ LED LED 25W 25W...
Page 40: ...2015 E Dale St Springfield MO 65803 417 869 6474 lorencook com...