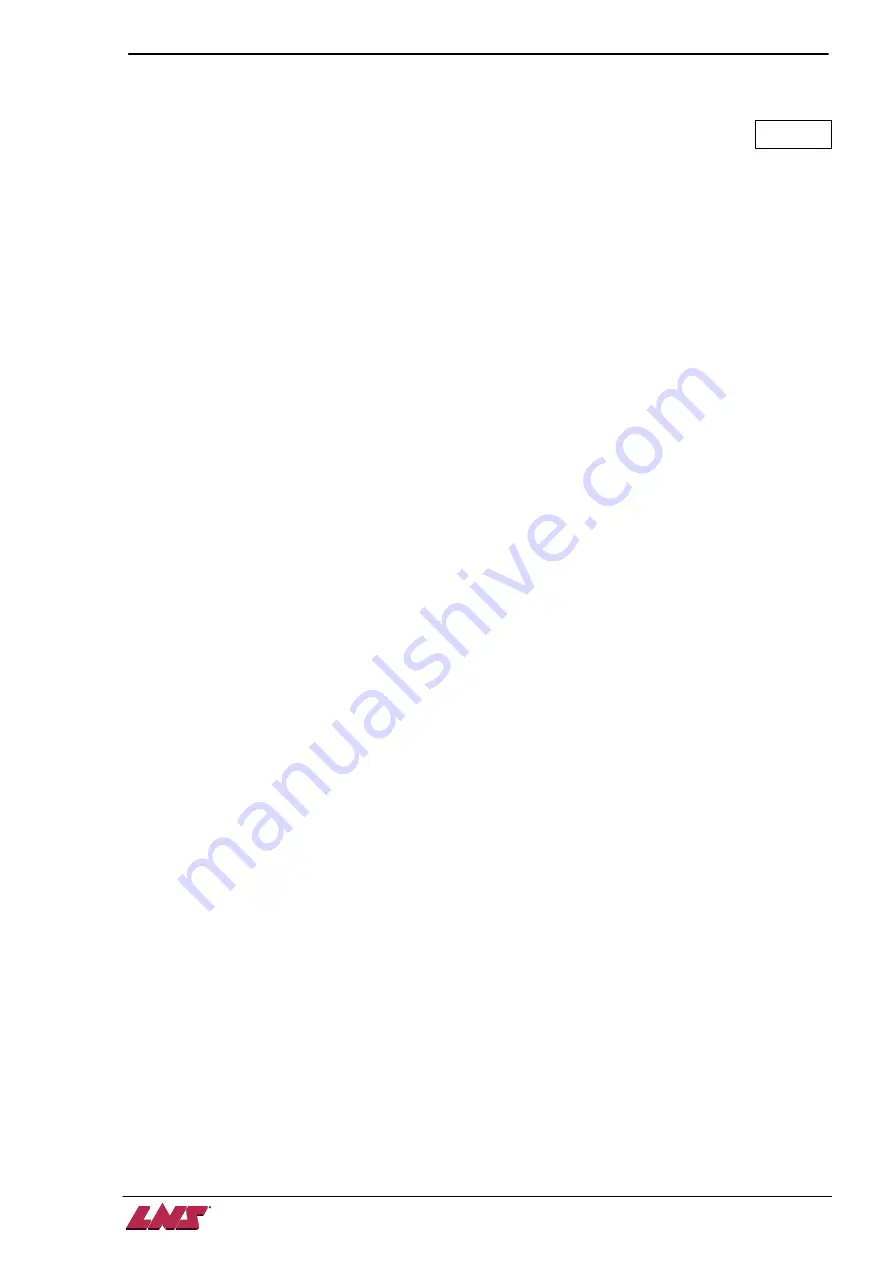
SPRINT 545/565 S2
V2.0
TABLE OF CONTENTS
CHAPTER 1 : BASIC PRINCIPLES .................................................................. 1-1
1.
STRUCTURE ......................................................................................................................... 1-2
2.
RIGHTS ................................................................................................................................. 1-3
3.
SAFETY REQUIREMENTS ................................................................................................... 1-5
4.
SAFETY DEVICES ................................................................................................................ 1-6
CHAPTER 2 : TECHNICAL DATA .................................................................... 2-1
1.
CHARACTERISTICS............................................................................................................. 2-2
2.
FLOOR PLAN ........................................................................................................................ 2-3
3.
LAYOUT OF THE ELEMENTS ............................................................................................. 2-5
CHAPTER 3 : SYSTEM START UP .................................................................. 3-1
1.
TRANSPORTATION ............................................................................................................. 3-2
2.
ASSEMBLY ........................................................................................................................... 3-5
3.
ANCHORING ......................................................................................................................... 3-6
4.
CONNECTIONS .................................................................................................................... 3-6
CHAPTER 4 : ELECTRICS ................................................................................ 4-1
1.
ELECTRICAL EQUIPMENT .................................................................................................. 4-2
2.
ELECTRICAL CABINET ....................................................................................................... 4-6
3.
INTERFACE DIAGRAM ...................................................................................................... 4-15
4.
INTERFACE ........................................................................................................................ 4-16
CHAPTER 5 : PNEUMATICS ............................................................................ 5-1
1.
PNEUMATIC EQUIPMENT ................................................................................................... 5-2
2.
AIR HANDLING ..................................................................................................................... 5-3
3.
PNEUMATIC BATTERY ....................................................................................................... 5-4
CHAPTER 6 : HYDRAULICS ............................................................................. 6-1
1.
HYDRAULIC EQUIPMENT ................................................................................................... 6-2
2.
HYDRAULIC ELEMENTS ..................................................................................................... 6-4
CHAPTER 7 : GENERAL DESCRIPTION ......................................................... 7-1
1.
BAR MAGAZINE ................................................................................................................... 7-2
2.
GUIDING BLOCKS ............................................................................................................... 7-3
3.
PUSHER ................................................................................................................................ 7-6
4.
BELT DRIVE .......................................................................................................................... 7-9
5.
REMNANT EXTRACTION SYSTEM (option) .................................................................... 7-10
6.
FRONT REST ...................................................................................................................... 7-12
7.
RETRACTION DEVICE (option) ........................................................................................ 7-14
8.
2-POSITION OPTION .......................................................................................................... 7-15
9.
AUTOMATIC FRONT REST (option) ................................................................................. 7-16
10.
2-POSITION PNEUMATIC FRONT REST (option) ........................................................... 7-17
Summary of Contents for Sprint 545 S2
Page 1: ...LNS SA CH 2534 Orvin www LNS group com Instruction Manual ENG Sprint 545 565 S2 9 545 01 ANG...
Page 2: ......
Page 5: ...CHAPTER 1 BASIC PRINCIPLES 1 1 SPRINT 545 565 S2 CHAPTER 1 BASIC PRINCIPLES...
Page 11: ...CHAPTER 2 TECHNICAL DATA 2 1 SPRINT 545 565 S2 CHAPTER 2 TECHNICAL DATA...
Page 14: ...2 4 CHAPTER 2 TECHNICAL DATA SPRINT 545 565 S2...
Page 16: ...2 6 CHAPTER 2 TECHNICAL DATA SPRINT 545 565 S2...
Page 17: ...CHAPTER 3 SYSTEM START UP 3 1 SPRINT 545 565 S2 CHAPTER 3 SYSTEM START UP...
Page 23: ...CHAPTER 4 ELECTRICS 4 1 SPRINT 545 565S2 CHAPTER 4 ELECTRICS...
Page 29: ...CHAPTER 4 ELECTRICS 4 7 SPRINT 545 565S2 2 2 LAYOUT OF THE ELEMENTS A D B C AJ1 A D B C AJ1...
Page 36: ...4 14 CHAPTER 4 ELECTRICS SPRINT 545 565S2...
Page 37: ...CHAPTER 4 ELECTRICS 4 15 SPRINT 545 565S2 3 INTERFACE DIAGRAM...
Page 42: ...4 20 CHAPTER 4 ELECTRICS SPRINT 545 565S2...
Page 43: ...CHAPTER 5 PNEUMATICS 5 1 SPRINT 545 565 S2 CHAPTER 5 PNEUMATICS...
Page 48: ...5 6 CHAPTER 5 PNEUMATICS SPRINT 545 565 S2 3 4 PNEUMATIC DIAGRAMS...
Page 49: ...CHAPTER 5 PNEUMATICS 5 7 SPRINT 545 565 S2...
Page 50: ...5 8 CHAPTER 5 PNEUMATICS SPRINT 545 565 S2...
Page 51: ...CHAPTER 6 HYDRAULICS 6 1 SPRINT 545 565S2 CHAPTER 6 HYDRAULICS...
Page 55: ...CHAPTER 7 GENERAL DESCRIPTION 7 1 SPRINT 545 565S2 CHAPTER 7 GENERAL DESCRIPTION...
Page 72: ...7 18 CHAPTER 7 GENERAL DESCRIPTION SPRINT 545 565S2...
Page 73: ...CHAPTER 8 HANDLING 8 1 SPRINT 545 565S25 CHAPTER 8 HANDLING...
Page 104: ...8 32 CHAPTER 8 HANDLING SPRINT 545 565S2...
Page 105: ...CHAPTER 9 MALFUNCTIONS 9 1 SPRINT 545 565S2 CHAPTER 9 MALFUNCTIONS...
Page 111: ...CHAPTER 10 APPENDICES 10 1 SPRINT 545 565S2 CHAPTER 10 APPENDICES...