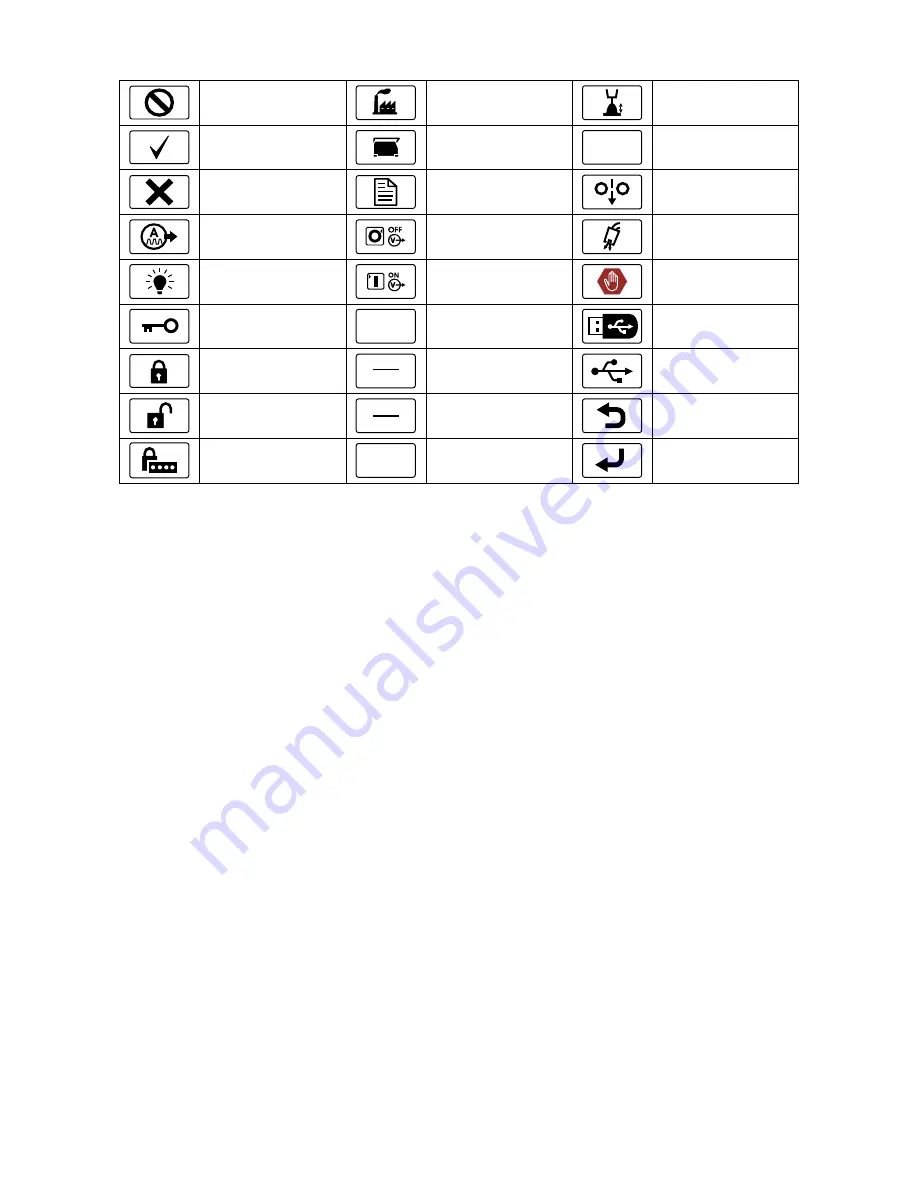
English
English
8
Disabled
Restore Factory Setting
Trim
Check Mark
?
View Software and
Hardware Version
Information
kW
Power in kW
Resignation Mark
Setup Menu
Cold Feed
Wave Controls
Switch Off Output
Voltage
MMA/TIG only)
Gas Purge
Brightness Level
Switch On Output
Voltage
(MMA/TIG only)
Error
Lock / Unlock
A
Welding Current
USB Memory
(PF46 only)
Locked
min
m
Wire Feed Speed
in [m/min]
USB Memory
is connected
(PF46 only)
Unlocked
min
in
Wire Feed Speed
in [in/min]
ESCape Button
Set Passcode
V
Welding Voltage
Confirm Button