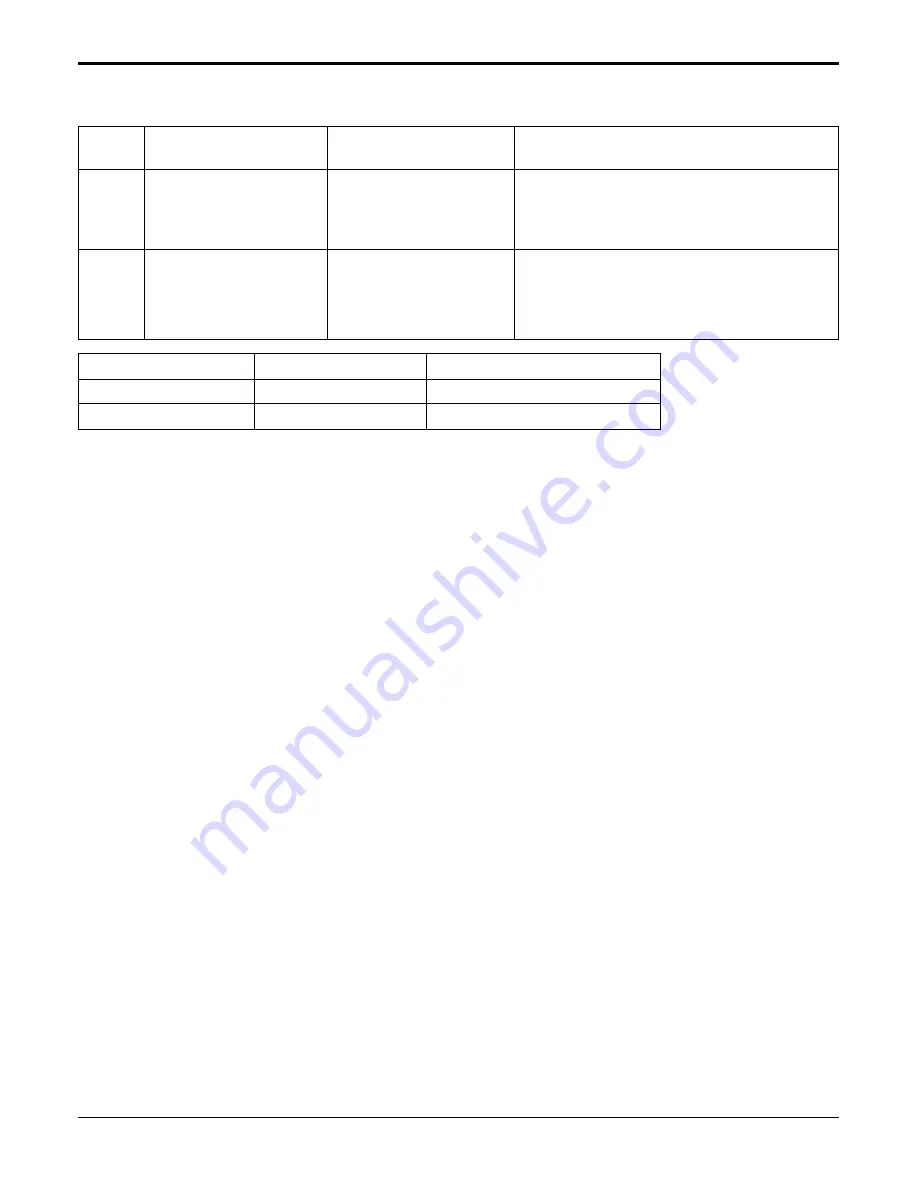
Service Manual 125
12) Troubleshooting CH51, CH60
51
60
Over capacity
EEPROM
Check sum
• Over capacity
Combination
• Check sum error
• Check the indoor unit capacity.
• Check the combination table.
• Check the PCB ASM P/No.
• Check the poor soldering.
Display
code
Title
Cause of error
Check point & Normal condition
Check Point
• CH 51
1. Check the indoor unit capacity.
• CH 60
1. Check the insertion condition of EEPROM.
2. Check the poor soldering
Troubleshooting Guide
Model
Gross max. capacity
Max. single indoor unit capacity
L8UC100BFA0
52k
12K
L8UH100BFA0
52k
12K
Summary of Contents for L8UC100BFA0
Page 92: ...92 Multi type Air Conditioner Schematic Diagram 2 Outdoor Unit 1 L8UC100BFA0 L8UH100BFA0 ...
Page 95: ...Service Manual 95 L8UH100BFA0 L8UC100BFA0 Schematic Diagram 2 Outdoor Unit ...
Page 97: ...Service Manual 97 2 Duct Type High static BH BG BE chassis Schematic Diagram ...
Page 98: ...98 Multi type Air Conditioner Schematic Diagram Low static BT BT1 chassis ...
Page 99: ...Service Manual 99 4 way TE TF TD chasis 58 B Schematic Diagram ...
Page 100: ...100 Multi type Air Conditioner Schematic Diagram 2 Display ASSEMBLY 1 Split Type ...
Page 153: ...P No 3828A22009L October 2005 Printed in Korea ...