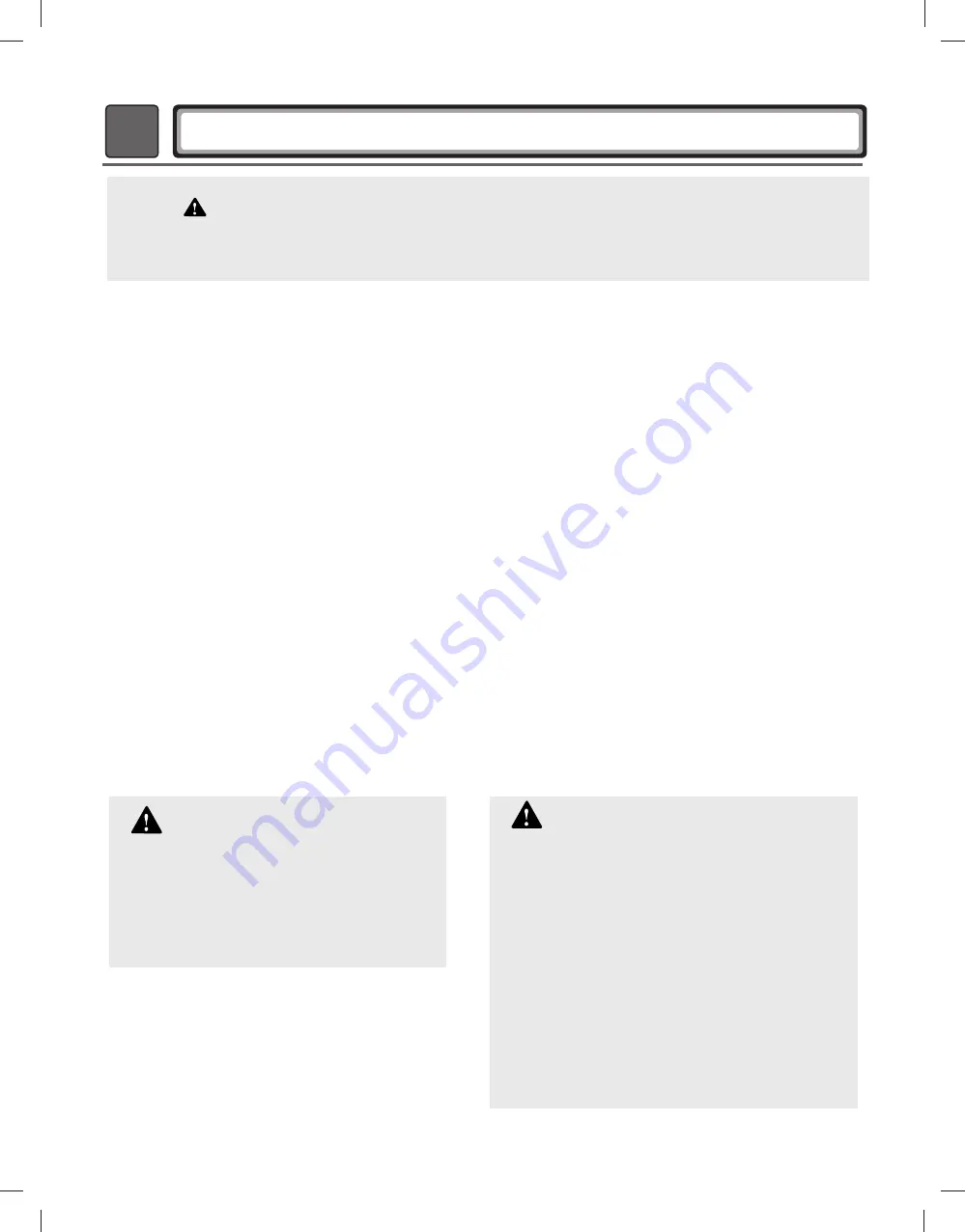
35
8
GAS REQUIREMENTS AND INSTRUCTIONS
Following are important instructions and information concerning the requirements for the gas supply and service for
gas dryers.
IMPORTANT WARNING:
The gas supply and service for a gas dryer must comply with all local
codes and ordinances. In the absence of any local codes or ordinances in your area, the gas supply and
service for your gas dryer must comply with the latest edition of the National Fuel Gas Code, ANSI Z223.1/
NFPA 54(USA) or Canadian gas installation code CAS B149.1(Canada).
1. Gas supply requirements: Liquefied
Petroleum (L.P.) Gas (2,500 Btu/ft3 (93.1
MJ/m3)) service must be provided at 10 +
1.5 in. water column pressure.
2. Do not attempt to connect the dryer to
Liquified Petroleum (LP Gas) Gas service
without a qualified professional.
3. Isolate the dryer from the gas supply piping
system by closing its individual manual shut-
off valve during any pressure testing of the
gas supply system at test pressure equal to
or less than 1/2 psi (3.45 kPa).
4. Supply Line Requirements. Your laundry
room must have a rigid gas supply line to
your dryer. In the United States, an
individual manual shutoff valve MUST be
installed within at least 6 feet (1.8 m) of the
dryer, in accordance with the National Fuel
Gas Code ANSI Z223.1 or Canadian gas
installation code CSA B149.1.
A 1/8 in. N.P.T. pipe plug must be installed as
shown.
5. If using a rigid pipe, the rigid pipe should be 1/2
inch IPS. If acceptable under local codes and
ordinances and when acceptable to your gas
supplier, 3/8 inch approved tubing may be used
where lengths are less than 20 feet (6.1 m).
Larger tubing should be used for lengths in
excess of 20 feet (6.1 m). It is also important that
you use pipe joint compound that is insoluble in
LP gas.
6. To reduce the danger of gas leaks, explosion,
and fire, please follow and observe the following
instructions and WARNINGS.
• Connect the dryer to the type of gas shown on the
nameplate.
• Use new flexible stainless steel connectors.
• Use Teflon tape and pipe joint compound insoluble
in LP gas on all pipe threads.
• Purge gas supply of air and sediment before
connecting the gas supply to the dryer in order to
prevent gas valve contamination. Before tightening
connection between gas supply and dryer, purge
remaining air until odor of gas is identified.
• DO NOT use an open flame to inspect for gas leaks;
instead use a non-corrosive leak detection fluid.
WARNING
•
Use a new AGA or CSA approved gas supply
line.
•
Install a shut-off valve.
•
Securely tighten all gas connections.
•
If connected to LP, have a qualified person
make sure gas pressure does not exceed 13
in. water column.
•
Examples of a qualified person include
licensed heating personnel, authorized gas
company personnel, and authorized service
personnel.
•
Failure to do so can result in death, explosion,
or fire.
WARNING
•
Do not attempt any disassembly of the
dryer. Any disassembly requires the
attention and tools of an authorized and
qualified service person or company.
•
Failure to do so can result in
death,explosion, or fire.
Summary of Contents for GDL1329CED3
Page 13: ...13 4 INITIAL STEPS FOR INSTALLING YOUR DRYER ...
Page 14: ...14 ...
Page 15: ...15 ...
Page 16: ...16 ...
Page 17: ...17 ...
Page 28: ...28 ...
Page 29: ...29 6 ELECTRICAL REQUIREMENTS FOR ELECTRIC DRYERS ...
Page 36: ...36 9 EXHAUST REQUIREMENTS AND MAINTENANCE ...
Page 40: ...40 10 DRYER CYCLE PROCESS ...
Page 42: ...42 44 ...
Page 43: ...43 ...
Page 44: ...44 12 MOTOR DIAGRAM AND SCHEMATIC Centrifugal switch Centrifugal switch Pull Drive forward ...
Page 45: ...45 13 CONTROL LAY OUT PWB ASSEMBLY DISPLAY LAY OUT PWB ASSEMBLY LAY OUT ...
Page 50: ...50 ...
Page 51: ...51 Trouble Symptom Measurement Condition Air TEMP RES k Air TEMP RES k Air TEMP RES k ...
Page 55: ...55 Trouble Symptom Measurement Condition ...
Page 56: ...56 Trouble Symptom Measurement Condition ...
Page 57: ...57 16 ERROR MODE ...
Page 61: ...61 18 CHANGE GAS SETTING NATURAL GAS PROPANE GAS ...
Page 62: ...62 ...
Page 71: ...71 EXPLODED VIEW 20 20 1 1 Control Panel Plate Assembly Coin OPL Type A210 A120 A116 A110 ...
Page 72: ...72 20 1 2 Control Panel Plate Assembly Card Type A210 A120 A117 A116 A110 ...