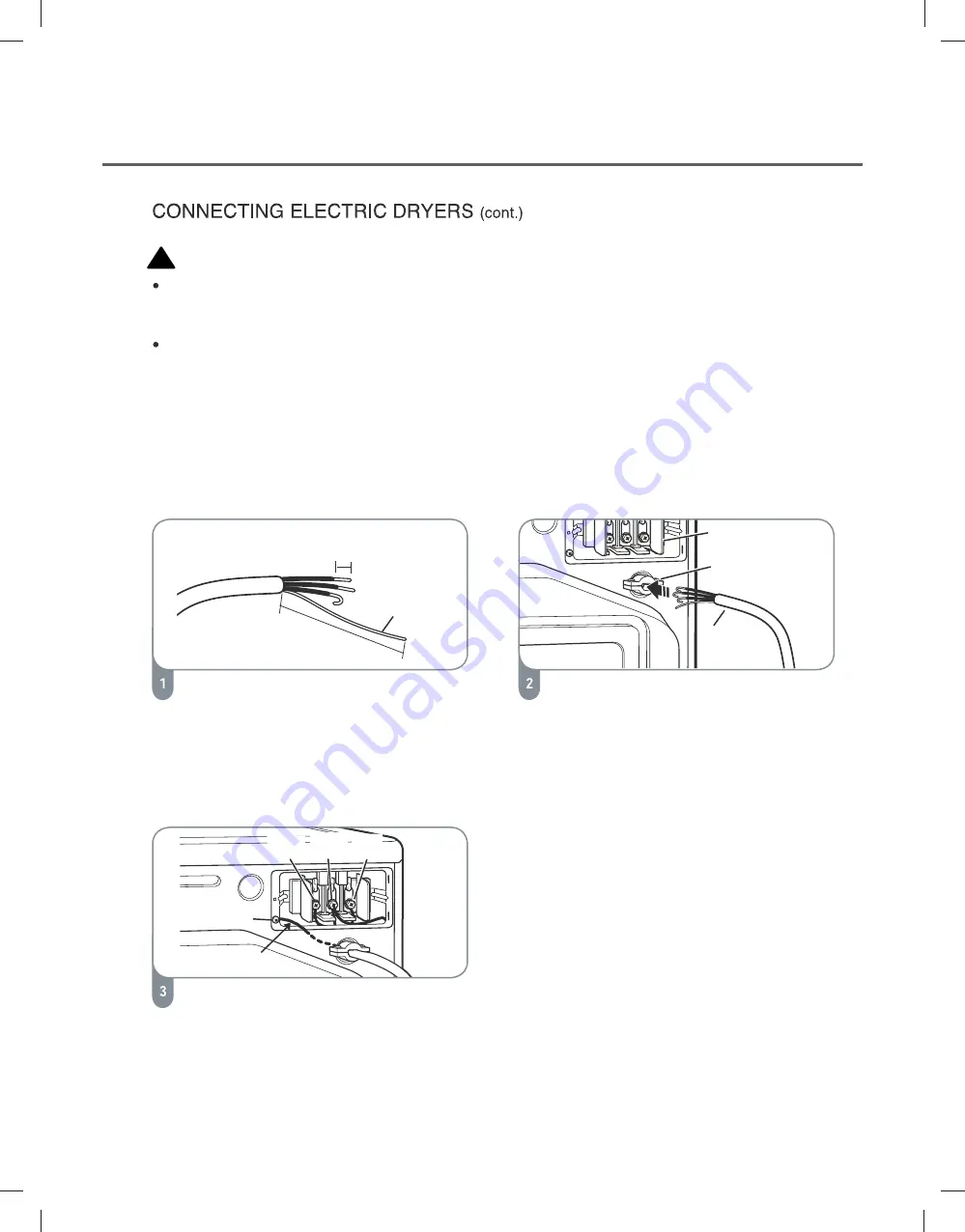
31
Remove 5 inches (12.7 cm) of the outer
covering from the wire. Remove 5 inches
of insulation from the ground wire. Cut off
approximately 1
1
⁄
2
inches (3.8 cm) from the
the other three wires and strip 1 inch (2.5
cm) insulation from each wire. Bend
the ends of the three shorter wires into
a hook shape.
Transfer the dryer’s ground wire from behind
the green ground screw to the center screw
of the terminal block. Attach the two hot
leads of the power cable to the outer terminal
block screws. Attach the white neutral wire
to the center terminal block screw. Attach the
power cable ground wire to the green ground
screw. TIGHTEN ALL SCREWS SECURELY.
Reinstall the terminal block access cover.
Ground Wire
Ground Screw
Neutral
(White)
Hot
(Black)
Ground Wire
Hot
(Red)
Remove the terminal block access cover
on the upper back of the dryer. Install a
UL-listed strain relief into the power cord
through-hole; then thread the power cable
prepared in Step 1 through the strain relief.
UL-Listed
Strain Relief
UL-Listed
4-Wire
Power Cord
Terminal
Block
5"
(12.7 cm)
1" (2.5 cm)
Four-Wire Connection for Electric Dryers: Direct Wire
• A 4-wire connection is required for all mobile
and manufactured home installations, as well
as all new construction after January 1, 1996.
• A UL-listed strain relief is required.
• Use UL-listed 4-wire #10 AWG-minimum copper
conductor cable.
• Allow at least 5 ft (1.5 m) length to allow for
removal and reinstallation of the dryer.
WARNING:
Connect the power cord to the terminal block. Each colored wire should be connected to
same color screw. Wire color indicated on manual is connected to the same color screw
in block. Failure to follow these instructions may result in a short or overload.
Grounding through the neutral conductor is prohibited for: (1) new branch-circuit
installations, (2) mobile homes, (3) recreational vehicles, and (4) areas where local
codes prohibit grounding through the neutral conductor.
!
Summary of Contents for GDL1329CED3
Page 13: ...13 4 INITIAL STEPS FOR INSTALLING YOUR DRYER ...
Page 14: ...14 ...
Page 15: ...15 ...
Page 16: ...16 ...
Page 17: ...17 ...
Page 28: ...28 ...
Page 29: ...29 6 ELECTRICAL REQUIREMENTS FOR ELECTRIC DRYERS ...
Page 36: ...36 9 EXHAUST REQUIREMENTS AND MAINTENANCE ...
Page 40: ...40 10 DRYER CYCLE PROCESS ...
Page 42: ...42 44 ...
Page 43: ...43 ...
Page 44: ...44 12 MOTOR DIAGRAM AND SCHEMATIC Centrifugal switch Centrifugal switch Pull Drive forward ...
Page 45: ...45 13 CONTROL LAY OUT PWB ASSEMBLY DISPLAY LAY OUT PWB ASSEMBLY LAY OUT ...
Page 50: ...50 ...
Page 51: ...51 Trouble Symptom Measurement Condition Air TEMP RES k Air TEMP RES k Air TEMP RES k ...
Page 55: ...55 Trouble Symptom Measurement Condition ...
Page 56: ...56 Trouble Symptom Measurement Condition ...
Page 57: ...57 16 ERROR MODE ...
Page 61: ...61 18 CHANGE GAS SETTING NATURAL GAS PROPANE GAS ...
Page 62: ...62 ...
Page 71: ...71 EXPLODED VIEW 20 20 1 1 Control Panel Plate Assembly Coin OPL Type A210 A120 A116 A110 ...
Page 72: ...72 20 1 2 Control Panel Plate Assembly Card Type A210 A120 A117 A116 A110 ...