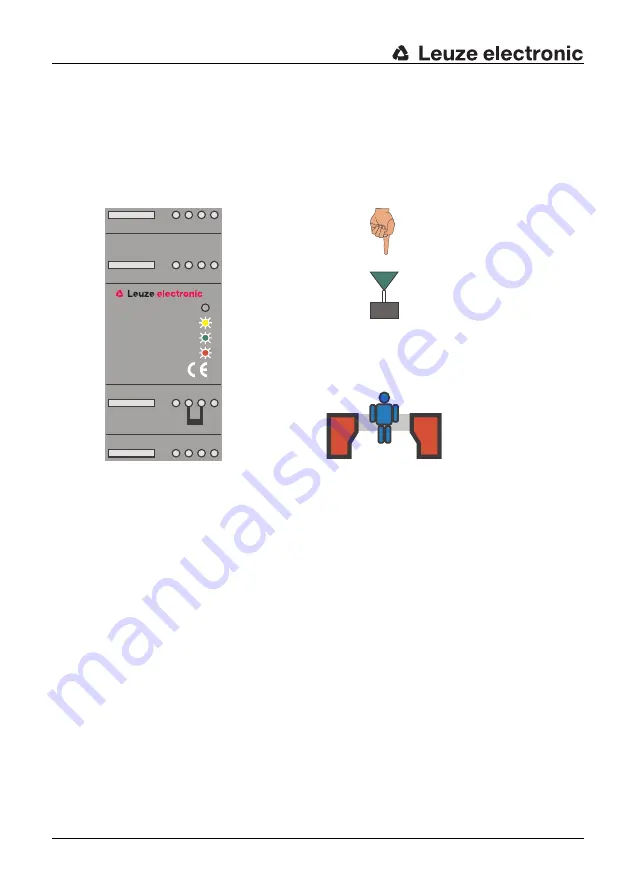
Function and Commissioning of the TNT 35
38
TNT 35 und TNT 35/7-24V
Leuze electronic
DEUTSCH
E
NGLISH
FRANÇAIS
IT
A
LIANO
ESPAÑOL
N
EDERLANDS
Safety field interruption:
The safety outputs of the TNT 35 are opened (LED "OFF/ON" on red) if during safety
operation the light beam of the protective photoelectric sensor is interrupted.
The restart-disable inside the TNT 35 becomes active and prevents an automatic restart of
the machine. The yellow LED "Start" displays the function of the restart-disable.
The TNT 35 is in waiting state and can be restarted by pressing the start-/restart button
after the safety field is free.
4.6
Fault indication and device reset
Faults of the test monitoring unit TNT 35 are indicated by the blinking of the red "ON/OFF"
LED. The possible faults are:
Fault in the operating mode selection:
The selected operating mode of the device at startup (with/without start- and restart-
disable) changed during operation. The jumper (terminal 22 to terminal 23 or terminal 23 to
terminal 24) should be checked that it is set to the desired operating mode.
Fault in the relay monitoring:
A fault in the wiring or soldered safety contacts was detected by the TNT 35. The wiring
and connected contacts should be checked.
Internal device failures:
Equipment faults that are caused by an internal defect result in the unit going into locked
state.
Figure 4.5-4:
Display of the TNT 35 during a safety field interruption
5 6
8
7
13 14 15 16
21 22 23 24
29 30 31 32
Sensor
Start/Active
EDM
OFF/ON
TNT35
Start
Activation
SLS