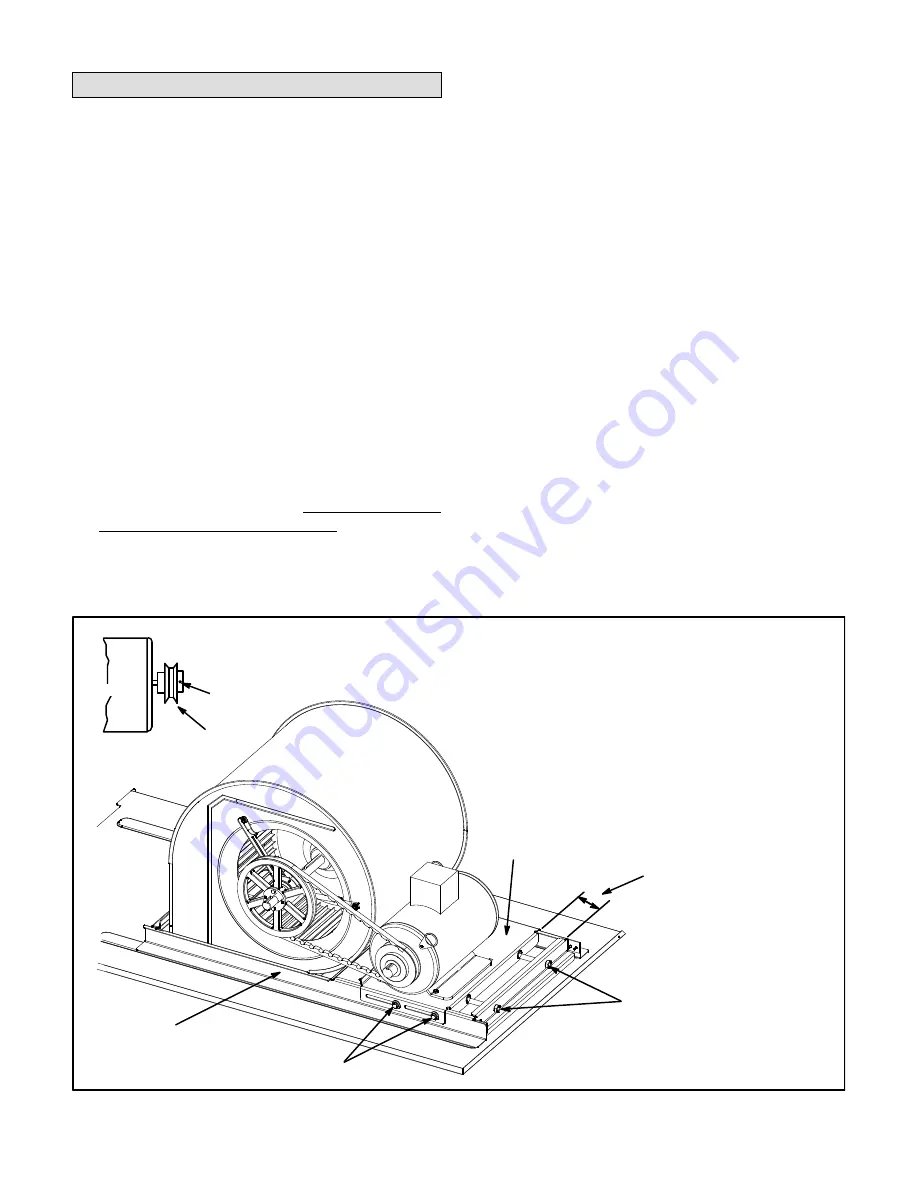
Page 7
Blower Operation and Adjustments
A-Three Scroll Compressor Voltage Phasing
Three phase scroll compressors must be phased
sequentially to ensure correct compressor and blower
rotation and operation. Compressor and blower are
wired in phase at the factory. Power wires are
color-coded as follows: line 1-red, line 2-yellow, line
3-blue.
1- Observe suction and discharge pressures and
blower rotation on unit start-up.
If pressure differential is not observed or blower rotation is
not correct:
2- Suction pressure must drop, discharge pressure
must rise, and blower rotation must match rotation
marking.
3- Disconnect all remote electrical power supplies.
4- Reverse any two field-installed wires connected to
the line side of K3, TB2 or F4. Do not reverse wires
at blower contactor or compressors.
5- Make sure the connections are tight.
Discharge and suction pressures should operate at
their normal start‐up ranges.
B-Blower Operation
Initiate blower demand at thermostat according to
instructions provided with thermostat. Unit will cycle on
thermostat demand. The following steps apply to
applications using a typical electro-mechanical
thermostat.
1- Blower operation is manually set at the thermostat
subbase fan switch. With fan switch in
ON
position,
blowers will operate continuously.
2- With fan switch in
AUTO
position, the blowers will
cycle with demand. Blowers and entire unit will be off
when system switch is in
OFF
position.
C-Blower Access
The blower assembly is secured to a sliding frame which
allows the blower motor to be pulled out of the unit. See
figure 6.
1- Loosen the reusable wire tie which secures the
blower wiring to the blower motor mounting plate.
2- Remove and retain screws on either side of sliding
frame. Pull frame toward outside of unit.
3- Slide frame back into original position when finished
servicing. Reattach the blower wiring in the previous
location on the blower motor base using the wire tie.
4- Replace retained screws on either side of the sliding
frame.
STANDARD BLOWER ASSEMBLY
TO INCREASE BELT TENSION
1- Loosen four bolts securing motor mounting base
to frame.
2- Turn adjusting bolt to the right, or clockwise, to
move the motor away from the blower housing.
IMPORTANT - Gap between end of frame and motor
mounting base should be equal at both ends, i.e. par
allel along gap.
3- Tighten four bolts securing motor mounting base
to frame.
4- Relieve tension on two adjusting bolts.
FIGURE 6
PULLEY
MOTOR
SIDE VIEW
ALLEN
SCREW
BELT ADJUSTING BOLTS
- TURN CLOCKWISE
TO TIGHTEN BELT
MOTOR
MOUNTING
BASE
LOOSEN BEFORE
ADJUSTING BELT TENSION
(TWO EACH SIDE)
MOTOR
BLOWER
HOUSING
BLOWER
FRAME
GAP BETWEEN EDGES SHOULD
BE PARALLEL ON BOTH ENDS
BEFORE TIGHTENING MOTOR
MOUNTING BASE IN PLACE