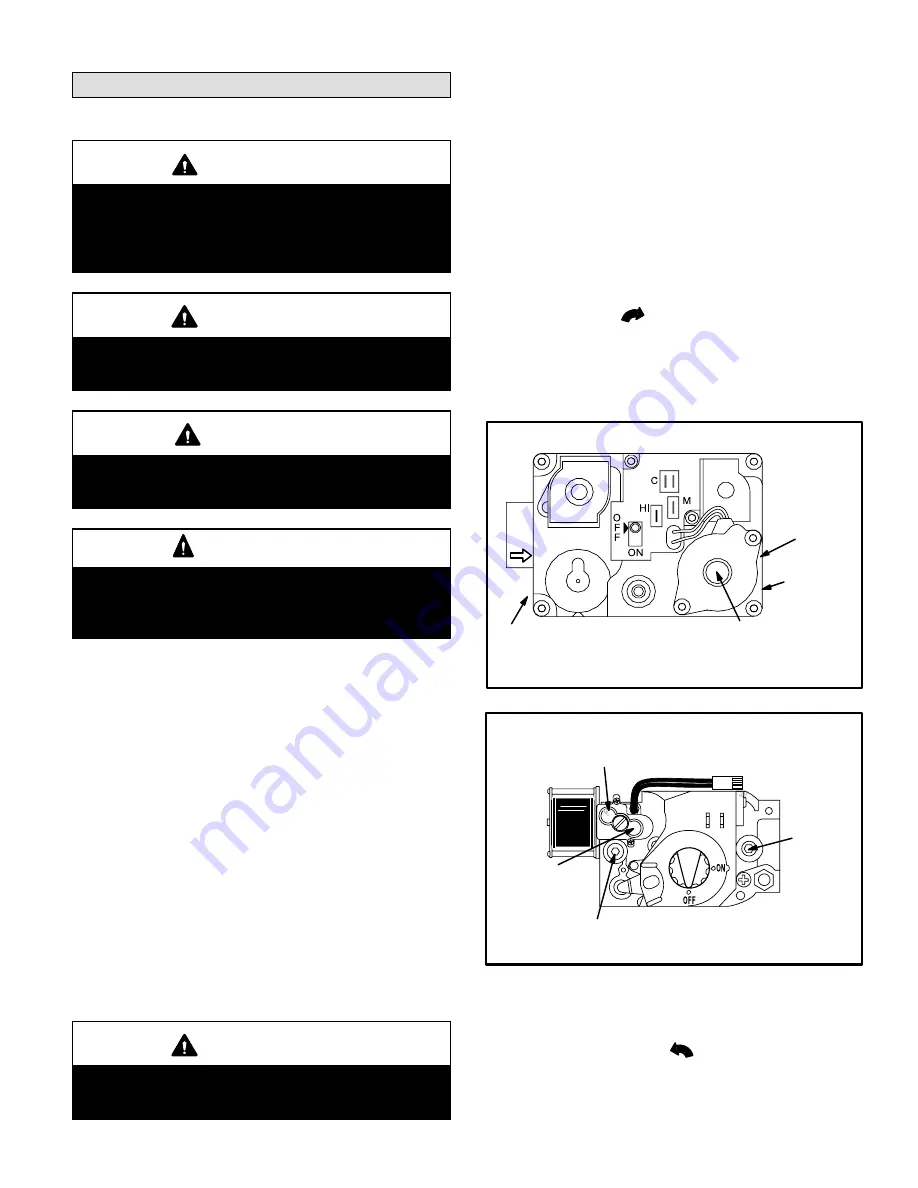
Page 37
Unit Start−Up
FOR YOUR SAFETY READ BEFORE LIGHTING
WARNING
Do not use this furnace if any part has been underwa-
ter. Immediately call a licensed professional service
technician (or equivalent) to inspect the furnace and
to replace any part of the control system and any gas
control which has been under water.
WARNING
If overheating occurs or if gas supply fails to shut off,
shut off the manual gas valve to the appliance before
shutting off electrical supply.
CAUTION
Before attempting to perform any service or mainte-
nance, turn the electrical power to unit OFF at dis-
connect switch.
WARNING
During blower operation, the ECM motor emits ener-
gy that may interfere with pacemaker operation. In-
terference is reduced by both the sheet metal cabinet
and distance.
BEFORE LIGHTING
smell all around the appliance area
for gas. Be sure to smell next to the floor because some gas
is heavier than air and will settle on the floor.
The gas valve on the G60UHV(X) unit may be equipped
with either a gas control knob or gas control switch. Use
only your hand to move the control switch or to turn the gas
control knob. Never use tools. If the knob will not turn or if
the control switch will not move by hand, do not try to repair
it. Call a licensed professional service technician (or equiv-
alent). Force or attempted repair may result in a fire or ex-
plosion.
Placing the furnace into operation:
G60UHV(X) units are equipped with an automatic ignition
system. Do not attempt to manually light burners on these
furnaces. Each time the thermostat calls for heat, the burn-
ers will automatically light. The ignitor does not get hot
when there is no call for heat on units with an automatic
ignition system.
WARNING
If you do not follow these instructions exactly, a fire
or explosion may result causing property damage,
personal injury or death.
Gas Valve Operation (Figures 26 and 27)
1 −
STOP
! Read the safety information at the beginning of
this section.
2 − Set the thermostat to the lowest setting.
3 − Turn off all electrical power to the unit.
4 − This furnace is equipped with an ignition device which
automatically lights the burners. Do
not
try to light the
burners by hand.
5 − Remove the upper access panel.
6 −
White Rodgers 36E Gas Valve −
Move gas valve con-
trol switch to
OFF
. See figure 26.
Honeywell VR8205 Gas Valve −
Turn knob on gas
valve clockwise
to
OFF
. Do not force. See figure
27.
7 − Wait five minutes to clear out any gas. If you then smell
gas, STOP! Immediately call your gas supplier from a
neighbor’s phone. Follow the gas supplier’s instruc-
tions. If you do not smell gas go to next step.
WHITE RODGERS 36E SERIES GAS VALVE
GAS VALVE SHOWN IN OFF POSITION
HIGH FIRE
MANIFOLD
PRESSURE
ADJUSTMENT
ON SIDE
(under cap)
MANIFOLD
PRESSURE
TAP ON SIDE
INLET PRESSURE
TAP ON SIDE
LOW FIRE MANIFOLD
PRESSURE ADJUSTMENT
ON SIDE (under cap)
FIGURE 26
HONEYWELL VR8205 SERIES GAS VALVE
GAS VALVE SHOWN IN OFF POSITION
MANIFOLD
PRESSURE
TAP
HIGH FIRE
ADJUSTING SCREW
(under cap)
INLET PRESSURE
TAP
LOW FIRE
ADJUSTING SCREW
(under cap)
FIGURE 27
8 −
White Rodgers 36E Gas Valve −
Move gas valve con-
trol switch to
ON
.
See figure 26.
Honeywell VR8205 Gas Valve −
Turn knob on gas
valve counterclockwise
to
ON
. Do not force. See
figure 27.
9 − Replace the upper access panel.
10− Turn on all electrical power to to the unit.