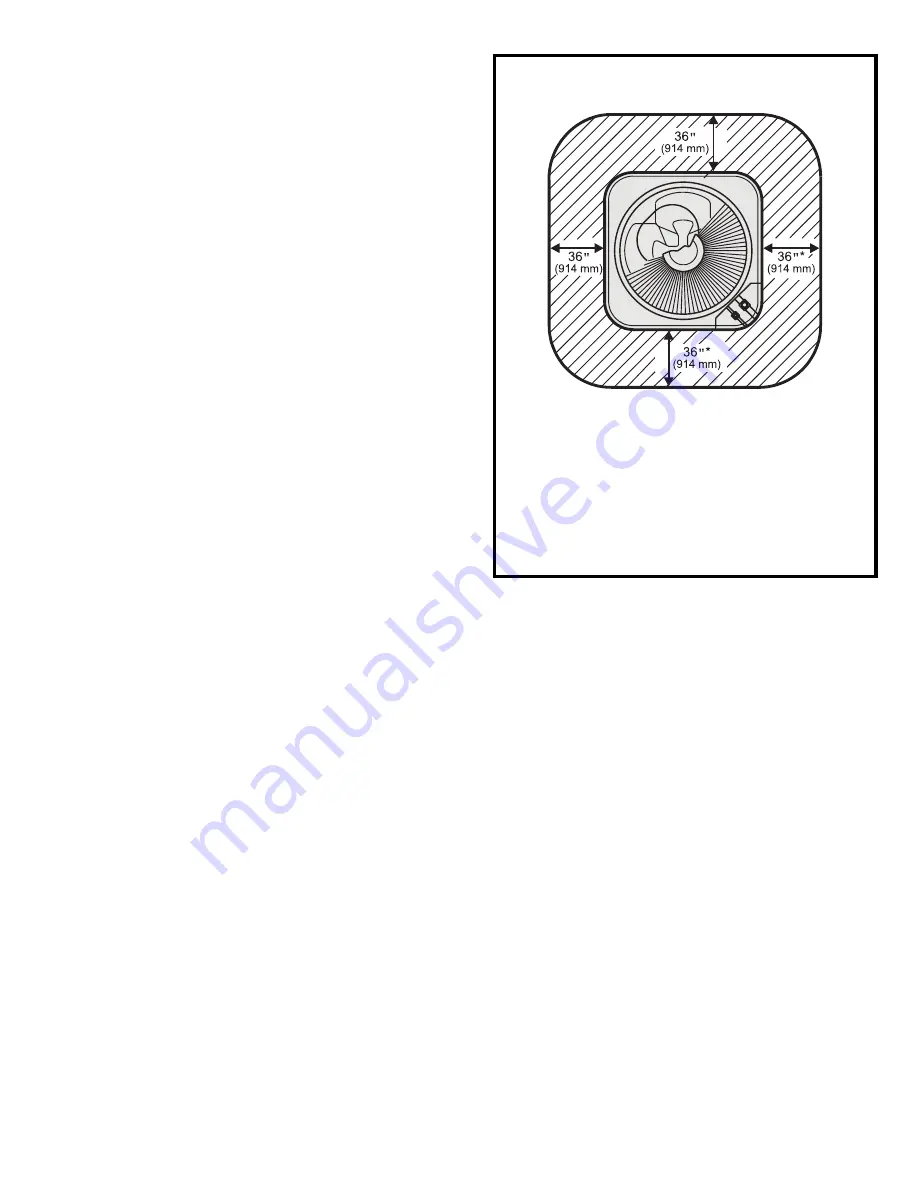
# 504,910M
Page 3
INSTALLATION
Roof Mounting
Install unit at a minimum of 4" above surface of the roof.
Care must be taken to ensure weight of unit is properly
distributed over roof joists and rafters. Either redwood or
steel supports are recommended.
Electrical Wiring
All field wiring must be done in accordance with the
National Electrical Code (NEC) recommendations,
Canadian Electrical Code (CEC) and CSA Standards, or
local codes, where applicable.
Refer to the furnace or blower coil Installation Instructions
for additional wiring application diagrams and refer to unit
rating plate for minimum circuit ampacity and maximum
overcurrent protection size.
Unit must be grounded in accordance with national
and local codes.
1. Install line voltage power supply to unit from a properly
sized disconnect switch.
2. Ground unit at unit disconnect switch or to an earth
ground. To facilitate conduit, a hole is in the bottom of
the control box. Connect conduit to the control box
General
Read this entire instruction manual, as well as the
instructions supplied in separate equipment, before
starting the installation. Observe and follow all warn-
ings, cautions, instructional labels, and tags. Failure
to comply with these instructions could result in an
unsafe condition and/or premature component failure.
These instructions are intended as a general guide only
for use by qualified personnel and do not supersede any
national or local codes in any way. The installation must
comply with all provincial, state, and local codes as well as
the National Electrical Code (U.S.) or Canadian Electrical
Code (Canada). Compliance should be determined prior
to installation.
SCU12M condensing units use R410A which is an ozone-
friendly HFC refrigerant. This unit must be installed with a
matching indoor coil and line set. SCU12M units are
designed for use in expansion valve (TXV) and fixed
orifice systems. The orifice is shipped with the unit while
the TXV expansion valve must be ordered separately from
the manufacturer. A filter drier approved for use with 410A
has been shipped with the unit. These components must
be installed prior to unit operation.
Inspection of Shipment
Upon receipt of equipment, carefully inspect it for possible
shipping damage. If damage is found, it should be noted
on the carrier’s freight bill. Take special care to examine
the unit inside the carton if the carton is damaged. Any
concealed damage discovered should be reported to the
last carrier immediately, preferably in writing, and should
include a request for inspection by the carrier’s agent.
If any damages are discovered and reported to the carrier
DO NOT INSTALL THE UNIT
, as claim may be denied.
Check the unit rating plate to confirm specifications
are as ordered.
Location of Unit
Refer to
UNIT DIMENSIONS
on page 2 for information on
sizing mounting slab, platforms, or supports. Refer to
Figure 1 for installation clearances.
Slab Mounting
When installing unit at grade level, install on a level slab
high enough above grade to allow adequate drainage of
water. Top of slab should be located so runoff water from
higher ground will not collect around unit.
Figure 1
Installation Clearances
* A service clearance of 30" must be maintained on one
of the sides adjacent to the control box. Clearance to
one of the other three sides must be 36". Clearance to
one of the remaining two sides may be 12" and the
final side may be 6".
A clearance of 24" must be maintained between units.
48" clearance required on top of unit. Maximum soffit
overhang is 36".