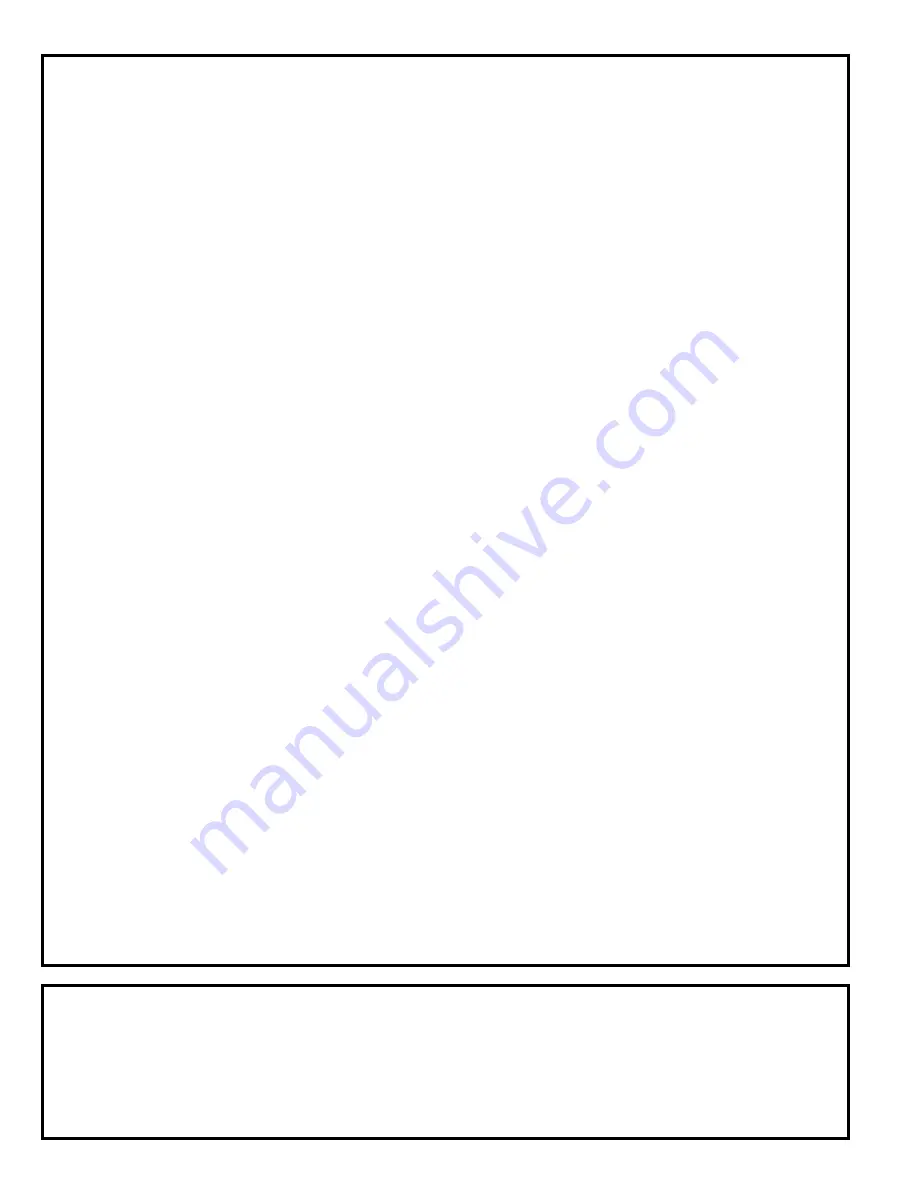
Page 16
# 504,910M
Limited Warranty
August 1, 1997
This warranty gives you specific legal rights and you may have other rights
which vary from state/province to state/province.
Warrantor: Armstrong Air Conditioning Inc., 421 Monroe St., Bellevue, OH 44811
Armstrong Air Conditioning Inc. products are available under the following names: Air Ease, Armstrong Air, American Aire, Concord
Subject to the limitations stated in this warranty, we warrant to the first buyer for use the residential heating, cooling or heat pump unit, when
installed, operated and maintained as required by this warranty, to be free of defects in workmanship or material for a period of 5 years
(1 year for commercial equipment) from the time of installation. We will replace any defective component without cost or expense to you
except for the costs of delivery and labor for removal and replacement of the defective component.
The SCU 12 Series air conditioners carry a 10 -year compressor warranty.
Warranty Begins
The warranty period begins when the installation is complete and the product is ready to operate. You must be able to verify this date
whenever a warranty claim is made. Original bill of sale, installer’s invoice or other similar document will suffice. If the beginning date
cannot be verified, we will consider warranty coverage to begin 6 months after the date the product was shipped from our factory.
Limitations on Implied Warranties
Implied warranties of merchantability or, to the extent applicable, fitness for a particular purpose are limited to 5 years, the same duration
as the basic limited written warranty provided herein. Some states/provinces do not allow limitations on how long an implied warranty of
merchantability or fitness lasts, so the above limitations or exclusions may not apply to you.
Only Warranty
This written Limited Warranty is the only warranty made by the warrantor; this warranty is in lieu of and excludes all other warranties,
express or implied. The warrantor does not authorize any person to provide any other warranty or to assume for it any further obligation in
connection with the warranted product.
What is NOT Covered
1. Cabinets or cabinet pieces.
2. Normal maintenance items such as filters, fan belts, fuses or other consumable items.
3. Damage caused by misuse, failure to maintain properly, accidents or acts of God.
4. External wiring, piping, venting or attachment of accessory products not integral to our product, including without limitation,
humidifier, air cleaner, vent damper, thermostat or other mechanical devices not manufactured by the warrantor.
5. Products that have been operated in a corrosive atmosphere where a concentration of acids, halogenated hydrocarbons or
other corrosive elements causes deterioration to metal surfaces or integral components. NOTE: Operation in a corrosive
atmosphere is considered abuse and voids this warranty.
6. Products that have NOT been installed in accordance with our published installation instructions, applicable local, state/
provincial or national codes, ACCA published standards.
7. Products that have NOT been installed by competent, qualified installers.
8. Products that have been moved from their original place of installation.
Warranty on Replacement Components
Any replacement component furnished by us will assume the remaining (unused) portion of the Limited Warranty.
Consequential Damages
The warrantor shall not be responsible for any consequential damages caused by any defect in the product. Some state/provinces do not
allow the exclusion or limitations of incidental or consequential damages, so the above limitation or exclusion may not apply to you.
This product must be installed, used and cared for in accordance with the instruction manual. You are responsible for required periodic
maintenance or service, such as changing or cleaning of air filters and lubrication or cleaning of components. Failure to properly install,
operate or maintain your unit voids this warranty.
Owner Record
Model # ________________________ Serial # _________________
Installation Date __________________
INSTALLED BY:
Dealer _____________________________________________________________________________________
Address ____________________________________________________________________________________
Telephone # ____________________________
License # _______________________________