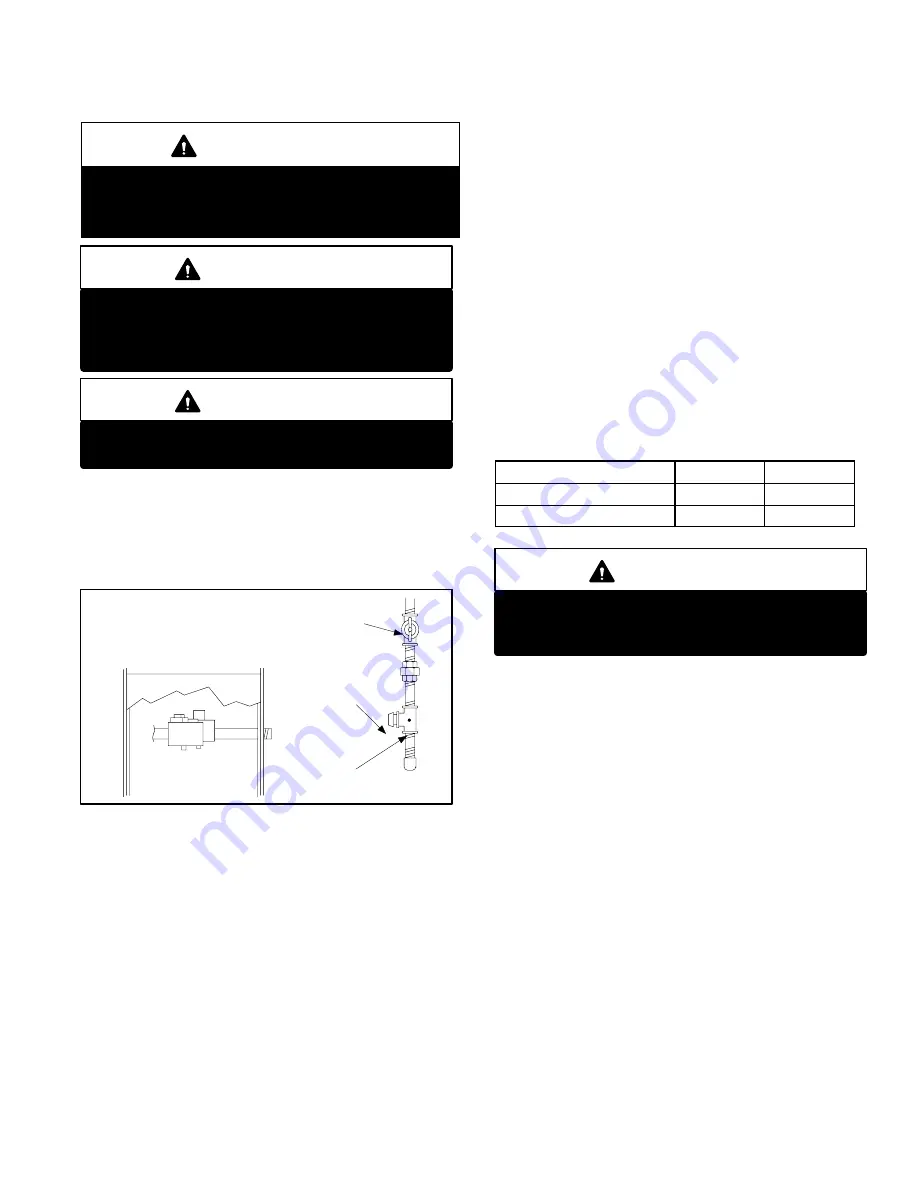
Page 25
Compounds used on gas piping threaded joints should be
resistant to action of liquefied petroleum gases.
C−Testing Gas Piping
CAUTION
If a flexible gas connector is required or allowed by
the authority that has jurisdiction, black iron pipe
shall be installed at the gas valve and extend outside
the furnace cabinet.
IMPORTANT
In case emergency shutdown is required, turn off
the main shut-off valve and disconnect the main
power to unit. These controls should be properly
labeled by the installer.
WARNING
Do not exceed 600 in−lbs (50 ft−lbs) torque when
attaching the gas piping to the gas valve.
When pressure testing gas lines, the gas valve must be dis-
connected and isolated. Gas valves can be damaged if
subjected to more than 0.5psig (14" W.C.). See figure 19
.
If
the pressure is equal to or less than 0.5psig (14"W.C.), use
the manual shut−off valve before pressure testing to isolate
furnace from gas supply.
FIGURE 19
MANUAL MAIN SHUT−OFF VALVE
WILL NOT HOLD TEST PRESSURE
IN EXCESS OF 0.5 PSIG (14"W.C.)
GAS VALVE
CAP
GAS PIPING TEST PROCEDURE
FIELD PROVIDED
LINE PRESSURE TAP
When checking piping connections for gas leaks, use pre-
ferred means. Kitchen detergents can cause harmful corro-
sion on various metals used in gas piping. Use of a specialty
Gas Leak Detector is strongly recommended. It is available
through Lennox under part number 31B2001. See Corp.
8411−L10, for further details.
Do not use matches, candles, flame or any other source of
ignition to check for gas leaks.
D−Testing Gas Supply Pressure
When testing supply gas pressure, connect test gauge to
inlet pressure tap (field provided). See figure 19. Check gas
line pressure with unit firing at maximum rate. Low pres-
sure may result in erratic operation or underfire. High pres-
sure can result in permanent damage to gas valve or over-
fire. See table 12 for operating pressure at unit gas connec-
tion (line).
On multiple unit installations, each unit should be checked
separately, with and without units operating. Supply pres-
sure must fall within range listed in previous paragraph.
E−Check Manifold Pressure
After line pressure has been checked and adjusted, check
manifold pressure. Move pressure gauge to outlet pres-
sure tap located on unit gas valve (GV1). Checks of man-
ifold pressure are made as verification of proper regulator ad-
justment. Manifold pressure for the G40UH(X) can be mea-
sured at any time the gas valve is open and is supplying gas
to the unit. See table 12 for normal operating manifold pres-
sure.
TABLE 12
All G40UH Units
Natural
LP
Line Pressure WC"
4.5 − 10.5
11.0 − 13.0
Manifold Pressure WC"
3.5
10.0
IMPORTANT
For safety, connect a shut-off valve between the
manometer and the gas tap to permit shut off of
gas pressure to the manometer.
The gas valve is factory set and should not require adjust-
ment. All gas valves are factory regulated. See specifica-
tions section of this manual for High Altitude manifold pres-
sure settings.
Manifold Adjustment Procedure:
1 − Connect a test gauge to outlet pressure tap on gas
valve. See figures 16, 15 and 17. Start unit and allow 5
minutes for unit to reach steady state.
2 − While waiting for the unit to stabilize, notice the flame.
Natural gas should burn blue. L.P. gas should burn
mostly blue with some orange streaks.
3 − After allowing unit to stabilize for 5 minutes, record
manifold pressure.
NOTE−Shut unit off and remove manometer as soon as
an accurate reading has been obtained. Take care to re-
place pressure tap plug.