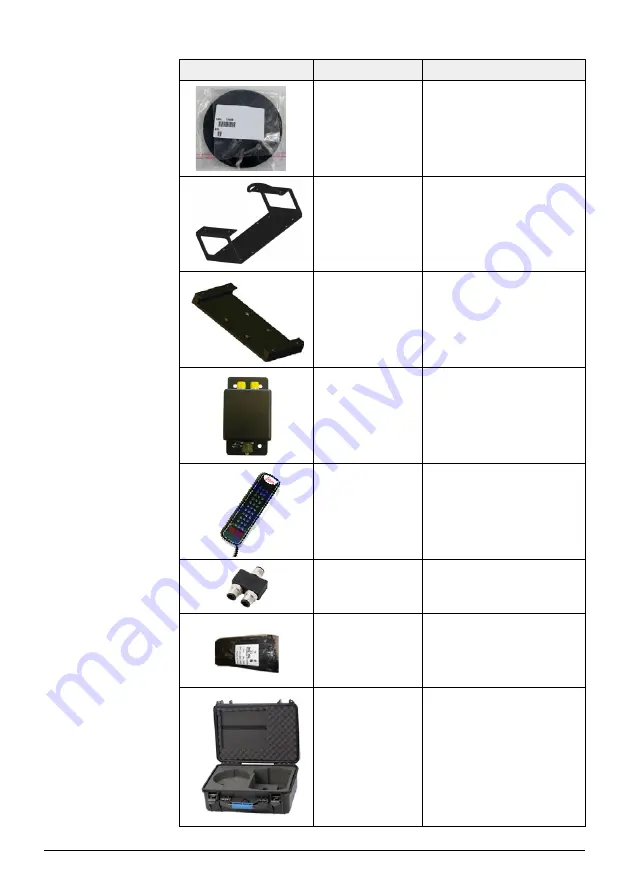
88
iCON grade, Spare Parts & Accessories
774308
Bracket for Rotation Sensor
for Komatsu
764916
Bracket for Junction box
upside-down
764917
Bracket f. junction box and
hydr clamp-on
761697
MJB300 CAN X 2xM12 1xMIL
764841
MLB1300 Remote Display
w. coil cable
772356
CX3 mini CAN-X,
3xM12/M/M/M
761702
Cable ties 4.8x200 mm,
100 pcs.
765546
Carrying case for iCON 3D
control panel.
Picture
Article number
Description