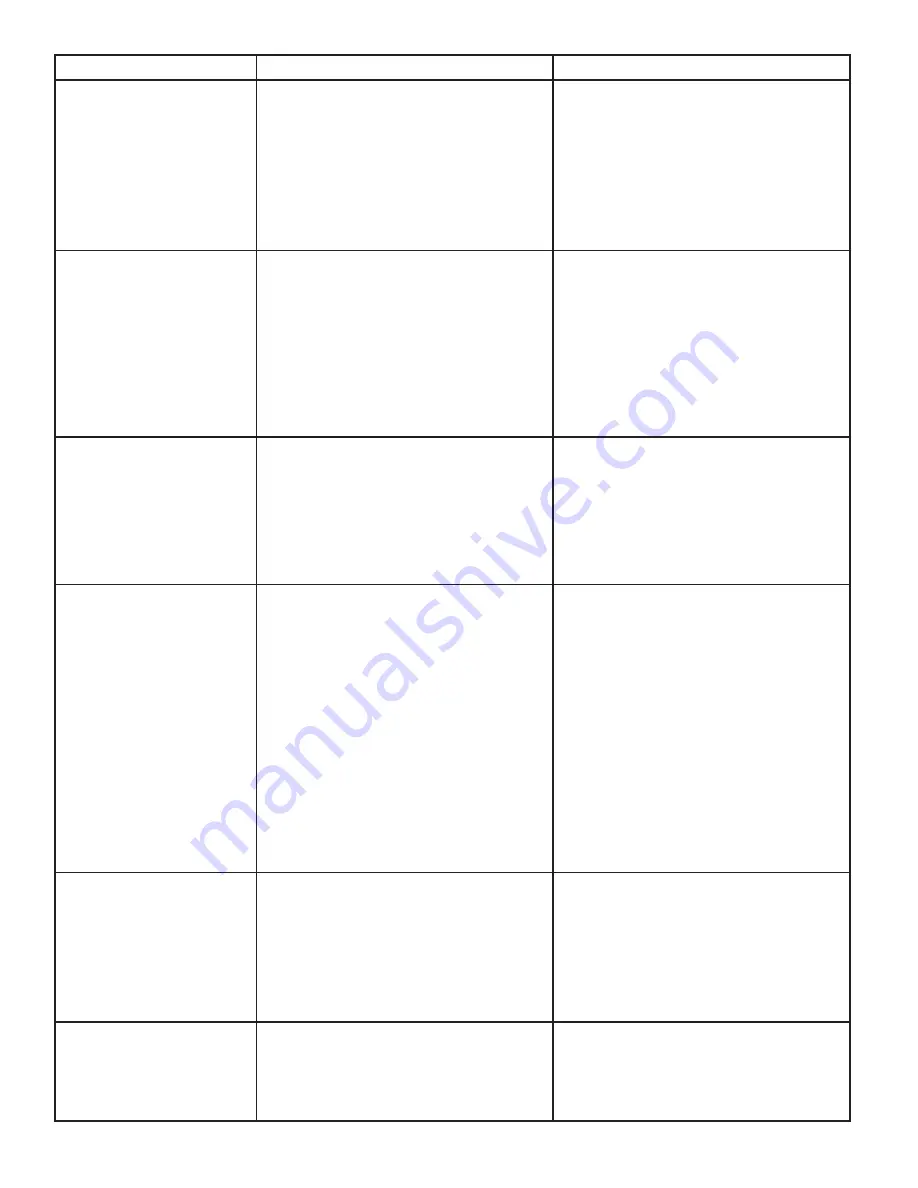
16
TROUBLE
CAUSE
REMEDY
Compressor does not start (no
hum), but gas cooler fan motor
runs.
1. Compressor relay, capacitors, or overload
protectors malfunctioning.
2.
Inadequate voltage.
3. Incorrect wiring.
4. Compressor malfunctioning.
1. Replace compressor relay, capacitors, or
overload protector.
2. Measure voltage across commom and run
terminal on compressor. Voltage must not
drop below 90% of rated voltage.
3. Refer to wiring diagram and correct.
4.
Have the unit repaired by a qualified
service technician.
Compressor does not start but
hums.
1.
Inadequate voltage.
2. Incorrect wiring.
3. Start capacitor or relay malfunctioning.
4. Compressor malfunctioning.
1. Measure voltage across common and run
terminal on compressor. Voltage must not
drop below 90% of rated voltage.
2. Refer to wiring diagram and correct.
3. Replace start capacitor or relay. Be sure
to use correct rating. Failure to use correct
rating will cause compressor failure.
4.
Have the unit repaired by a qualified
service technician.
Compressor starts but does not
switch off start winding (will run
for only a few seconds before
internal overload switches
before internal overload
switches compressor off).
1.
Inadequate voltage.
2. Incorrect wiring.
3. Starting relay malfunctioning.
1. Measure voltage across common and run
terminal on compressor. Voltage must not
drop below 90% of rated voltage.
2. Refer to wiring diagram and correct.
3. Replace starting relay. Be sure to use
correct relay. Failure to use correct relay
will cause compressor failure.
Compressor starts and runs
a short time but shuts off on
overload.
1. Dirty condenser.
2.
Insufficient or blocked air flow.
3.
Inadequate voltage.
4. Incorrect wiring.
5. Defective condenser fan motor.
6. Refrigerant leak.
7. Compressor malfunctioning.
1. Clean the condenser.
2. Remove all obstruction and allow for
minimum clearances of 8 inches (203 mm)
over top.
3. Measure voltage across common and run
terminal on compressor. Voltage must not
drop below 90% of rated voltage.
4. Refer to wiring diagram and correct.
5.
Have the unit repaired by a qualified
service technician.
6.
Have the unit repaired by a qualified
service technician.
7.
Have the unit repaired by a qualified
service technician.
Compressor runs normally, but
water line is frozen.
1. Low water level in water bath.
2. Syrup in water bath.
3. Water cage is out of position.
4. Low refrigerant charge or slow refrigerant
leak.
1. Add water to water bath until water runs
out of overflow into drip tray.
2. Drain water from water bath and refill with
clean water.
3. Reposition water cage.
4.
Have the unit repaired by a qualified
service technician.
Compressor cycles on and off
frequently during the initial
pulldown and/or normal
operations.
1. PCB malfunctioning
2. Defective probe.
3. Weak overload or pressure switch.
1. See page 18.
2. Replace probe.
3.
Have the unit repaired by a qualified
service technician.
Summary of Contents for CED-04
Page 19: ...19 INTENTIONALLY LEFT BLANK...
Page 23: ...23 Wiring Diagram 115 Volt...