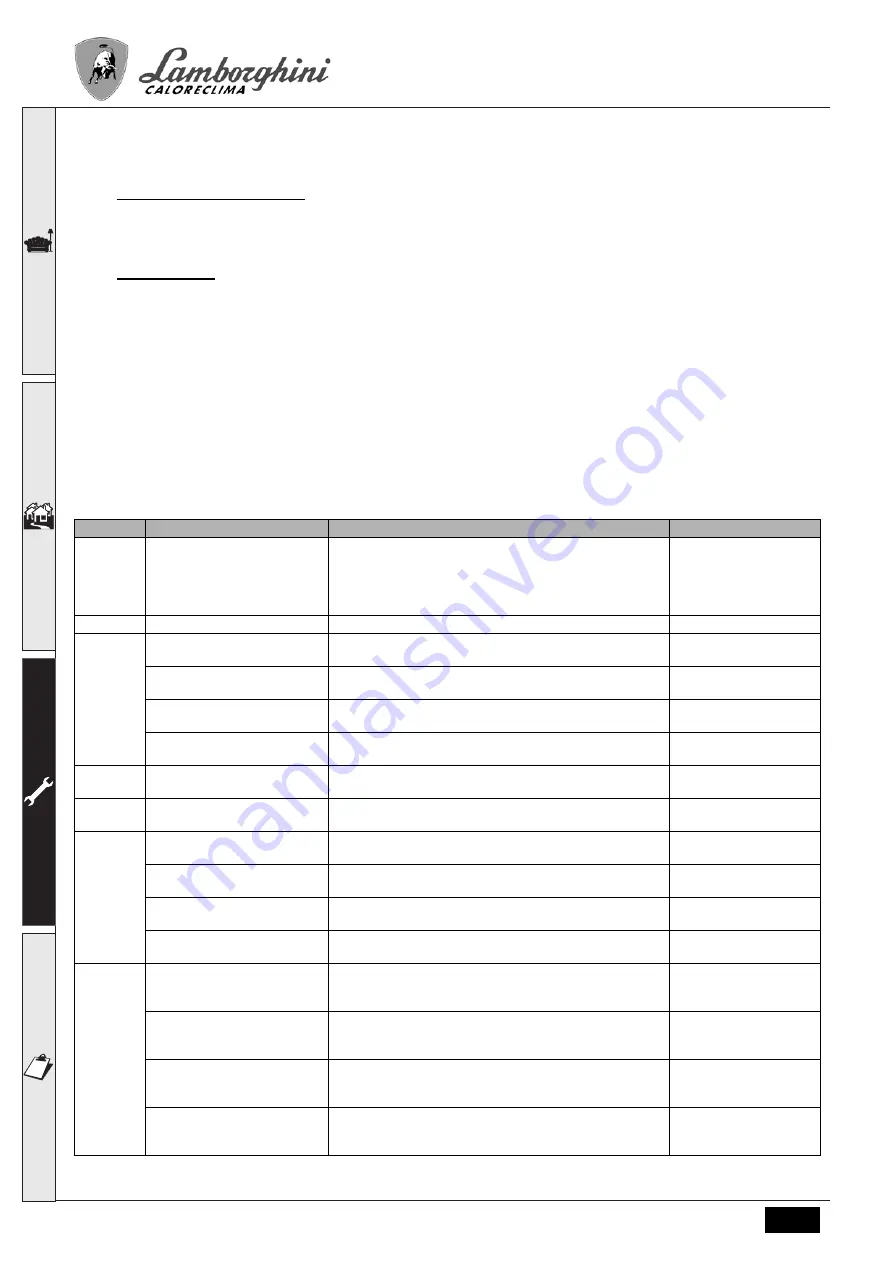
iXinox 24 C
24
EN
cod. 3541N452EN - Rev. 03 - 03/2020
The TEST mode is automatically disabled in any case after 15 minutes or on stopping of hot water drawing (if enough
hot water is drawn to activate DHW mode).
Heating power adjustment
To adjust the heating power, switch the boiler to TEST mode (see sez. 3.1). Press the heating buttons detail 3 - fig. 1
to increase or decrease the power (min. = 00 - max. = 100). Press the
reset
button within 5 seconds and the max. power
will remain that just set. Exit TEST mode (see sez. 3.1).
Service menu
ONLY QUALIFIED PERSONNEL CAN ACCESS THE SERVICE MENU AND MODIFY PARAMETERS.
The card Service Menu is accessed by pressing the Reset button for 10 seconds.
The display will show: "100" and the message "co" flashing.
Then set "103" with the DHW buttons, with the heating buttons set "123" and confirm by pressing the Reset button.
Five submenus are available: press the Heating buttons to select, in increasing or decreasing order,
“tS”, “sC”, “In”,
“Hi”
or
“rE”
.
To enter the selected menu, press the
reset
button once.
“tS” - Transparent Parameters Menu
Press the Heating buttons to scroll the list of parameters in increasing or decreasing order. Press the DHW buttons to
view or modify the value of a parameter: the change will be automatically saved.
Contents
Description
Range
Default
b01
Boiler type selection
1
= BITHERMAL INSTANTANEOUS
2
= MONOTHERMAL HEATING only (also with OPTIONAL
STORAGE TANK)
3
= MONOTHERMAL COMBI
4
= MONOTHERMAL with STORAGE TANK
3=RRT
b02
Exchanger type
1 ÷ 4
1
b03
Absolute Maximum Heating
Power (b02=1)
0 ÷ 100%
(Do not modify the value)
83%
Absolute Maximum Heating
Power (b02=2)
0 ÷ 100%
(Do not modify the value)
85%
Absolute Maximum Heating
Power (b02=3)
0 ÷ 100%
(Do not modify the value)
85%
Absolute Maximum Heating
Power (b02=4)
0 ÷ 100%
(Do not modify the value)
90%
b04
System water pressure protec-
tion selection
0=Pressure switch, 1=Pressure transducer
0=Pressure switch
b05
Summer / Winter function
0
= WINTER - SUMMER - OFF
1
= WINTER - OFF
0 = Enabled
b06
Variable input contact operation
selection (b01=1)
0=Flowmeter off, 1=System thermostat, 2=Second room ther-
mostat, 3=Warning/Notification, 4=Safety thermostat
2=Second room therm.
Variable input contact operation
selection (b01=2)
0=Continuous Comfort, 1=System thermostat, 2=Second room
thermostat, 3=Warning/Notification, 4=Safety thermostat
2=Second room therm.
Variable input contact operation
selection (b01=3)
0=Flowmeter off, 1=System thermostat, 2=Second room ther-
mostat, 3=Warning/Notification, 4=Safety thermostat
2=Second room therm.
Variable input contact operation
selection (b01=4)
0=Continuous Comfort, 1=System thermostat, 2=Second room
thermostat, 3=Warning/Notification, 4=Safety thermostat
2=Second room therm.
b07
Relay card LC32 operation selec-
tion (b01=1)
0=External gas valve, 1=Alarm, 2=System loading solenoid
valve, 3=solar 3-way valve, 4=Second heating pump,
5=Alarm2, 6=Burner On, 7=Frost protection active.
0=External gas valve
Relay card LC32 operation selec-
tion (b01=2)
0=External gas valve, 1=Alarm, 2=System loading solenoid
valve, 3=Legionella pump, 4=Second heating pump, 5=Alarm2,
6=Burner On, 7=Frost protection active.
0=External gas valve
Relay card LC32 operation selec-
tion (b01=3)
0=External gas valve, 1=Alarm, 2=System loading solenoid
valve, 3=solar 3-way valve, 4=Second heating pump,
5=Alarm2, 6=Burner On, 7=Frost protection active.
0=External gas valve
Relay card LC32 operation selec-
tion (b01=4)
0=External gas valve, 1=Alarm, 2=System loading solenoid
valve, 3=solar 3-way valve, 4=Second heating pump,
5=Alarm2, 6=Burner On, 7=Frost protection active.
0=External gas valve