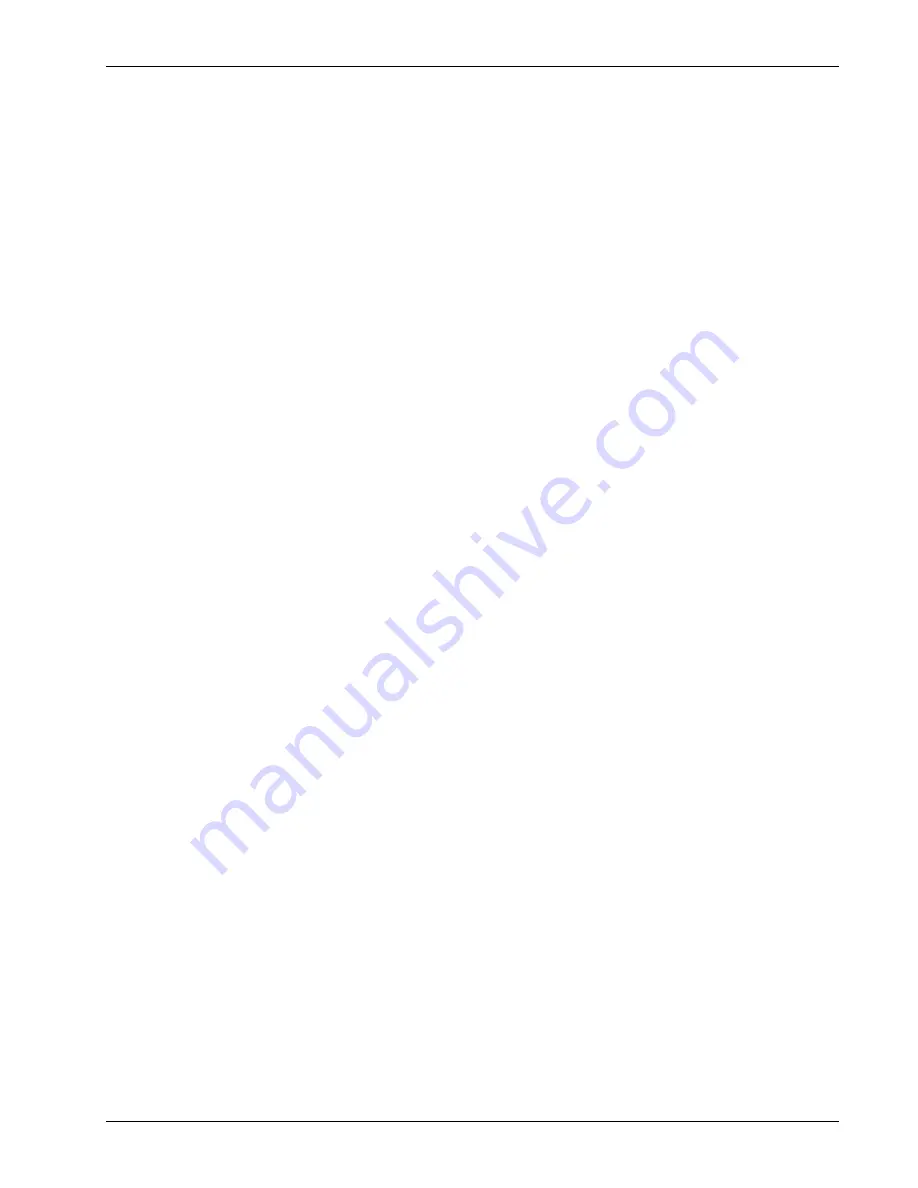
Lake Shore Model 340 Temperature Controller User’s Manual
Temperature Control Operation
6-7
6.9 USING OPEN LOOP CONTROL
Directly setting control output is called open loop control because there is no feedback from a load sensor to
close the control loop. Load temperature, setpoint, and control parameters are ignored. Use open loop control
for experiments requiring constant control output regardless of load temperature, for initial cooling system
tuning, or for when a computer calculates the control equation and sends output information to the instrument.
To use open loop control, set control mode to open (refer to Paragraph 6.5).
When using Control Loop 1 and the heater output, select an appropriate heater range. The manual output
parameter sets the control output as percent of full scale current or power on the selected heater range.
Manual Output setting range is -100% to +100% with a resolution of 0.01%. Change settings from the front
panel or with a computer interface. Negative values are not recommended when using the heater.
When using control Loop 2 and Analog Output 2, manual output parameter sets control output in percent of
the ±10 V range. Manual Output setting range is ±100% with a resolution of 0.01%. Negative values are not
recommended unless the output drives a device operating as a heating and cooling source. In most cases,
configure Analog Output 2 as unipolar when using it for control output.
To enter a manual output value, press
Loop 1
or
Loop 2
to display control parameters for that loop in the
lower portion of the display. Press
Manual Output
to highlight the
MOut
setting field. Enter a value with the
number keys and press
Enter
to save the change or
Escape
to return to the previous value. Default is 0.
6.10 SETTING A SETPOINT AND SETPOINT UNITS
The control setpoint is the desired load temperature expressed in temperature or sensor units. Use sensor
units if no temperature response curve is selected for the sensor input used as the control channel.
The control setpoint has its own units parameter. When the user selects sensor units as the setpoint units the
instrument calculates the control equation in sensor units. It calculates the control equation in temperature
with setpoint units set to kelvin or Celsius. The setpoint displays in the selected units. Adjust the P control
parameter when changing setpoint units from temperature to sensor. Control channel readings can display in
any units. Display units need not match setpoint units.
When changing setpoint units while the control loop is active, the Model 340 converts the control setpoint to
the new control units for minimal disruption in control output.
To select setpoint units, press
Control Setup
to display the
CONTROL SETUP
screen with the control loop
indicator highlighted in the upper left hand corner. Use the
s
or
t
key to select Loop 1 or 2. Press
Enter
or
Next Setting
to display control setup parameters for that loop. Press
Next Setting
until the
Setp Unit
field
highlights. Use the
s
or
t
key to select units. Press
Enter
or
Next Setting
to continue with more settings, or
press
Save Screen
to store changes in the Model 340. Default is Temp K.
Setpoint resolution depends on sensor type and setpoint units. With setpoint expressed in temperature,
setpoint resolution is 0.001 degree for setpoints below 1000, and 0.0001 for setpoints below 10. In sensor
units, the setpoint resolution matches the display resolution for the sensor input type given in the
specifications (Table 1-1). If auto ranging sensor, enter a units multiplier of
Ω
or k
Ω
after the setpoint.
The instrument allows a large setpoint range to accommodate a variety of sensors and units. With setpoint
expressed in sensor units, setpoint range is unlimited. The user must determine suitability of a setpoint value.
In temperature units, two safety features limit the setpoint value to help prevent load damage load. The first
limit is the part of the temperature response curve that shows maximum safe temperature in kelvin for the
sensor package. It can be verified by using the
Curve Entry
key (Paragraph 8.1). The user may enter a
second global limit (Paragraph 6.13.1). Set it to the maximum safe temperature in kelvin for the entire system.
The setpoint is limited to a value less than or equal to the lower of the two safety limits.
After selecting setpoint units and limits, enter the setpoint value. Setpoint has a direct setting key because it
changes often. The setpoint value remains on the display any time control parameters for its control loop
display. If the setpoint value changes from the number entered when
Enter
is pressed, it is likely the setpoint
exceeds one of the above limits is inappropriate for the sensor type.
To enter a setpoint value, press
Loop 1
or
Loop 2
to display control parameters for that loop in the lower
portion of the display. Press
Setpoint
to highlight the setpoint setting field. Enter a value with the number
keys and press
Enter
to save the change or
Escape
to return to the previous value. Select a scale factor of
n, u, m, k, M, or G. Blank indicates a scale factor of x1. The default is 0.