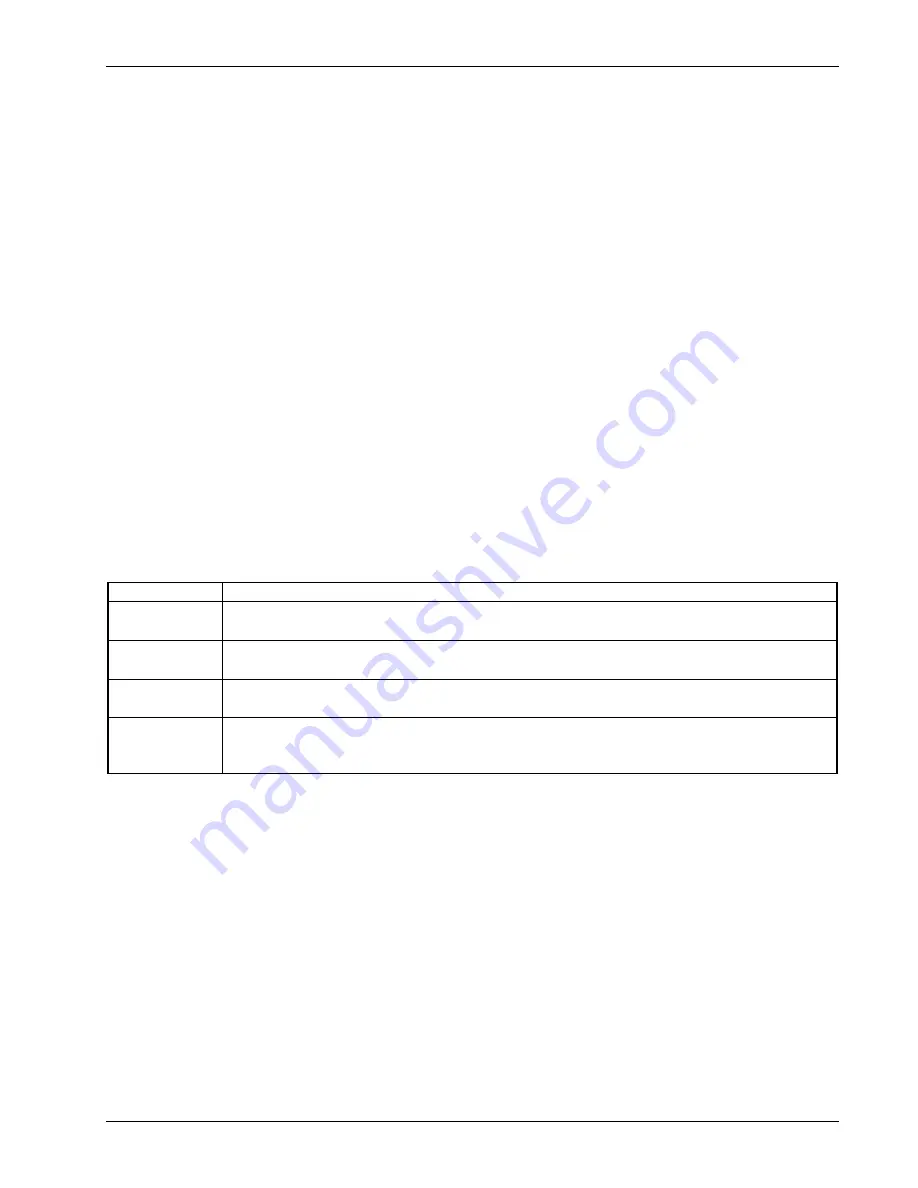
Lake Shore Model 340 Temperature Controller User’s Manual
Temperature Control Operation
6-3
6.4 CONTROL
CHANNEL
A control loop gets feedback from a control sensor located with or near the load. Either standard input can be
used for control; optional inputs appear on the setting list if useable. Configure the sensor input used for
control to match the sensor type, or as a special type with the correct temperature coefficient. No temperature
response curve is needed if the user controls in sensor units. Inputs using a scanner are not recommended
for control use.
If the user changes the control channel without selecting a temperature response curve for both the old and
new Channel, the Model 340 sets control units to sensor units and picks the sensor units reading from the
new control channel as the new Setpoint.
The user can choose which sensor input to use as feedback for each control loop. Loop 1 and Loop 2 settings
are independent.
To select a control channel, press
Loop 1
or
Loop 2
to display control parameters for that loop in the lower
portion of the display. Press
Control Channel
to highlight the setting field for the control channel sensor
input. Use the
s
or
t
key to select the sensor input. Press
Enter
to save the change or
Escape
to return to
the previous setting. The default setting is A.
6.5 CONTROL
MODES
There are two ways to tune a closed loop PID control loop using the Model 340: manual and AutoTune
(Paragraphs 2.6 thru 2.8). Once the control loop is tuned, the control parameters chosen function for a given
temperature range. If more than one temperature range is required, the user must change the control
parameters depending on the setpoint temperature. The Model 340 offers several options for doing so
including zone control, AutoTune, or internal programming.
Table 6-1. Control Mode Description
Control Mode
Description
MANUAL PID
The instrument can always be used in manual mode. The user changes control
parameters based on cooling system experience and knowledge.
AUTO PID
The AutoTune feature can be left on. It computes new control parameters after each
setpoint change. Auto PI and Auto P are similar, but they set only P and I or only P.
ZONE
Zone control mode automatically enters pre-selected control parameters when the
setpoint is changed to a value outside the present temperature zone (Paragraph 6.8).
OPEN LOOP
Open loop control allows the user to directly set control output. This is not a PID control
mode, but it is available for absolute setting of output. Use the Manual Output parameter
for open loop settings.
NOTE:
Internal programming is not a selection for control mode, but a separate feature that can change
PID control parameters and several other parameters. Internal programming overrides Manual
PID, but it can be used with Zone control (refer to Paragraph 8.3).
To select a control mode, press the
Control Setup
key and the
CONTROL SETUP
screen appears. The
control loop indicator is highlighted in the upper left hand corner. Use the
s
or
t
key to select Loop 1 or 2.
Press the
Enter
or
Next Setting
key. The control setup parameters for that loop are displayed. Press the
Next Setting
key until the
Ctrl Mode
field is highlighted. Use the
s
or
t
key to select the control mode.
Press the
Enter
or
Next Setting
key to continue with more settings, or press the
Save Screen
key to store
the changes in the Model 340. The default setting is Manual.