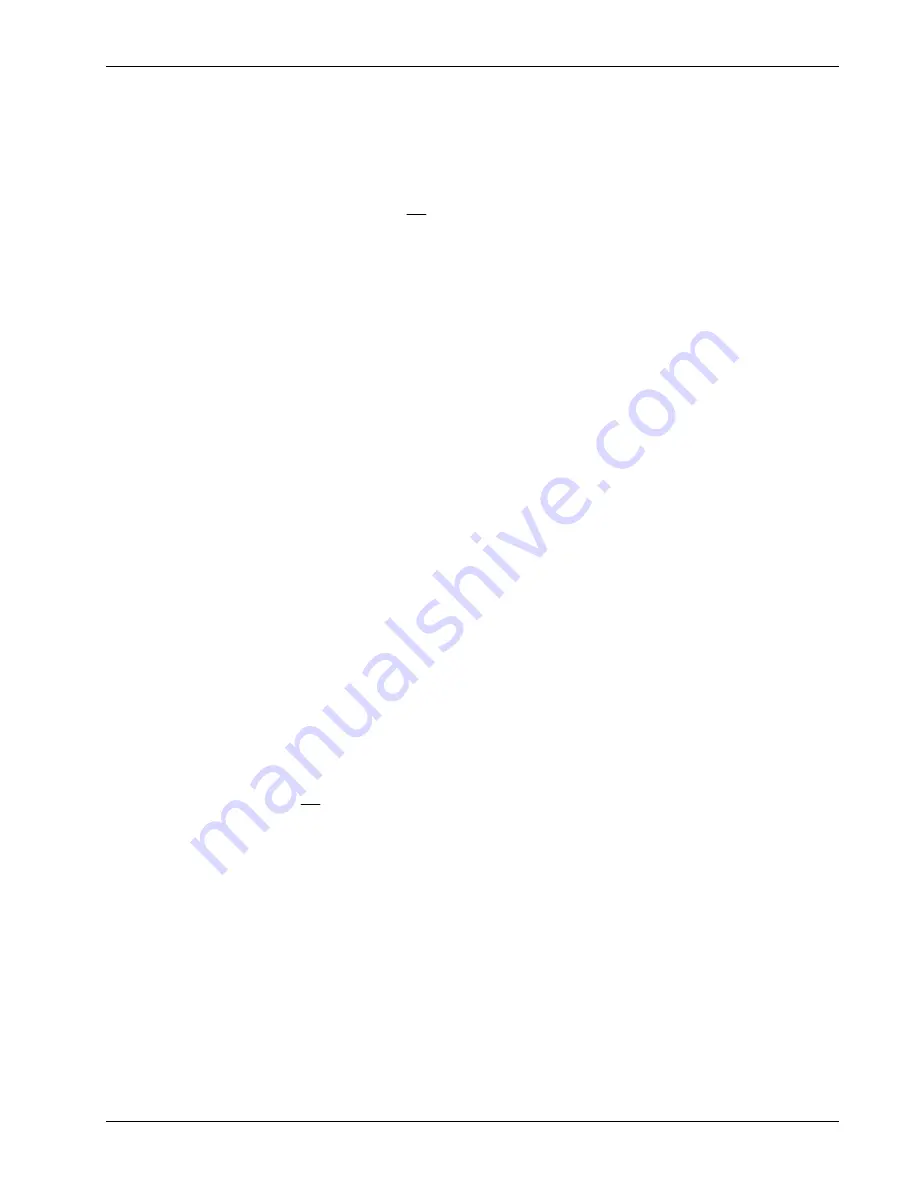
Lake Shore Model 340 Temperature Controller User’s Manual
Cooling System Design
2-9
2.6 PID
CONTROL
The Model 340 Temperature Controller uses a algorithm called PID control for closed-loop control operation.
The control equation for the PID algorithm has three variable terms, a P or proportional term, an I or integral
term, and a D or derivative term. See Figure 2-3. Changing these variables for best control of a system is
called tuning. The PID equation in the Model 340 is:
where
error (e) = Setpoint - Feedback Reading
.
Proportional (P) is discussed in Paragraph 2.6.1. Integral (I) is discussed in Paragraph 2.6.2. Derivative (D) is
discussed in Paragraph 2.6.3. Finally, the manual heater output is discussed in Paragraph 2.6.4.
2.6.1 Proportional
(P)
The Proportional term, also called gain, must have a value greater than zero for the control loop to operate.
The value of the proportional term is multiplied by the error (e) which is defined as the difference between the
setpoint and feedback temperatures, to generate the proportional contribution to the output: Output (P) = Pe.
If proportional is acting alone, with no integral, there must always be an error or the output will go to zero. A
great deal must be known about the load, sensor, and controller to compute a proportional setting (P). Most
often, the proportional setting is determined by trial and error. The proportional setting is part of the overall
control loop gain, and so are the heater range and cooling power. The proportional setting will need to change
if either of these change.
2.6.2 Integral
(I)
In the control loop, the integral term, also called reset, looks at error over time to build the integral contribution
to the output:
Output I
PI e dt
a f
a f
=
z
.
By adding the integral to proportional contributions, the error that is necessary in a proportional only system
can be eliminated. When the error is at zero, controlling at the setpoint, the output is held constant by the
integral contribution. The integral setting (I) is more predictable than the gain setting. It is related to the
dominant time constant of the load. As discussed in Paragraph 2.7.3, measuring this time constant allows a
reasonable calculation of the integral setting. In the Model 340, the integral term is not set in seconds like
some other systems. The integral setting can be derived by dividing 1000 by the integral seconds:
I
setting
= 1000 / I
seconds
.
2.6.3 Derivative
(D)
The derivative term, also called rate, acts on the change in error with time to make its contribution to the
output:
Output D
PD
de
dt
( )
=
.
By reacting to a fast changing error signal the derivative can work to boost the output when the setpoint
changes quickly, reducing the time it takes for temperature to reach the setpoint. It can also see the error
decreasing rapidly when the temperature nears the setpoint and reduce the output for less overshoot. The
derivative term can be useful in fast changing systems but it is often turned off during steady state control
because it reacts too strongly to small disturbances. The derivative setting (D) is related to the dominant time
constant of the load similar to the I setting. The derivative term is set in seconds.
Heater Output
=
+
+
L
NM
O
QP
z
P e I e dt D
de
dt
a f