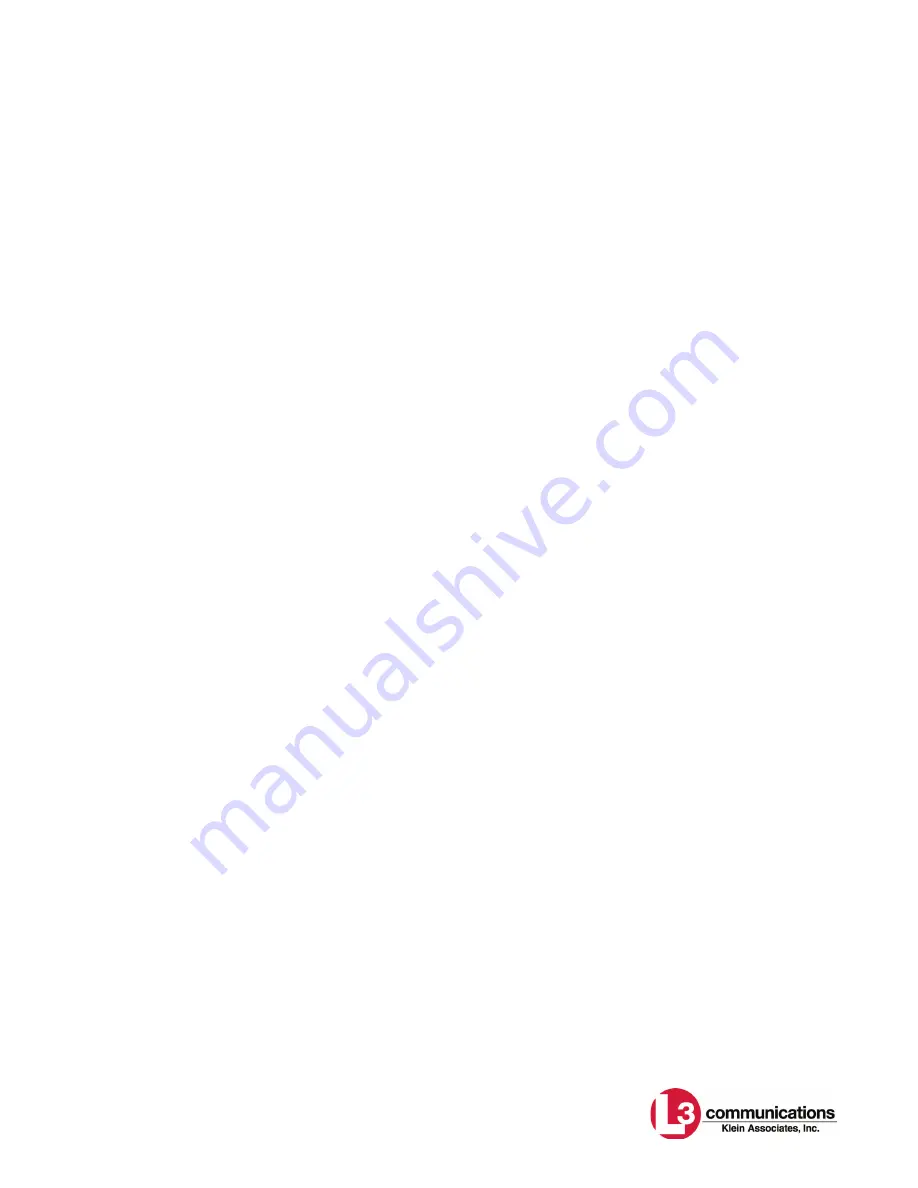
Theory of Operation
1-9
CPU board.
The CPU board is an embedded MVME-6100-based processor
board that enables external control of the TPU by a PC connected via an
Ethernet 100BaseT local area network (LAN), providing control over system
functions. All functions, including communicating the operating parameters to
the DSP and extracting sensor data from the Demultiplexer board, are
communicated over the LAN.
Demultiplexer board.
The Demultiplexer board receives the encoded digital
data telemetered from the towfish, recovers the clock and data, and then
decodes the data and routes it to the DSP for processing.
The data from the towfish arrives in serial NRZ format and is conditioned and
input to the clock recovery circuit. The recovered clock is used to strobe the
serial data into a line decoder. The decoded data is converted to parallel format
and output the front panel connector.
The downlink modulators are used to indicate to the towfish when to fire the
main array and to send commands to the towfish. The modulators use FSK
modulation and are frequency multiplexed together before being amplified and
combined with 200-volt power which is then transmitted down the tow cable.
The CPU board controls the modulators, thereby allowing their independent
operation.
DSP board.
The DSP board is the heart of the sea bottom imaging system. It
processes the data and forms the multiple swaths for display. The processed
data is output via a parallel interface to an external sonar display processor;
i.e., workstation or PC. The DSP performs the multi-channel processing using
a parallel processor approach. To achieve this the board is equipped with three
high performance floating point DSP processors and supporting ICs. The board
is capable of performing 150 million floating point operations per second
(75 MIPS). This level of processing performance is necessary to provide for
the required real-time operation. The board uses a phase shift beam forming
algorithm along with a proprietary interpolation algorithm to form the
respective swaths. All the swath forming is under software control, allowing
updates and revisions by the simple changing of a PROM. In the same way
multiple test modes have been incorporated in the operating code of the
system.
The DSP board also demultiplexes the high speed sensor data from the towfish
and passes this information to the CPU board. This data includes the optional
high speed yaw rate, pitch, roll, and altimeter data.
Since the DSP board is essentially a very high speed computer, little else can
be said about its operation. The details of the swath processing software are
proprietary and are not discussed any further here.
Summary of Contents for SERIES 5000
Page 27: ......
Page 59: ......
Page 162: ...Splashproof TPU Drawings 6 13 ...
Page 164: ...Splashproof TPU Drawings 6 15 ...
Page 166: ...Splashproof TPU Drawings 6 17 ...
Page 167: ......
Page 170: ...A 3 Figure A 1 Cable Length vs Towfish Depth Graph 1 ...
Page 172: ...A 5 Figure A 3 Cable Length vs Towfish Depth Graph 3 ...
Page 174: ...A 7 Figure A 5 Cable Length vs Towfish Depth Graph 5 ...
Page 175: ......
Page 179: ......
Page 203: ......
Page 262: ...NMEA 0183 Formats and Information D 59 D 13 NMEA 0183 Formats and Information ...
Page 264: ...NMEA 0183 Formats and Information D 61 ...
Page 265: ......
Page 268: ...E 3 ...
Page 270: ...E 5 ...
Page 272: ...E 7 ...
Page 274: ...E 9 ...
Page 276: ...E 11 ...
Page 278: ...E 13 ...
Page 280: ...E 15 ...
Page 282: ...E 17 ...
Page 283: ......