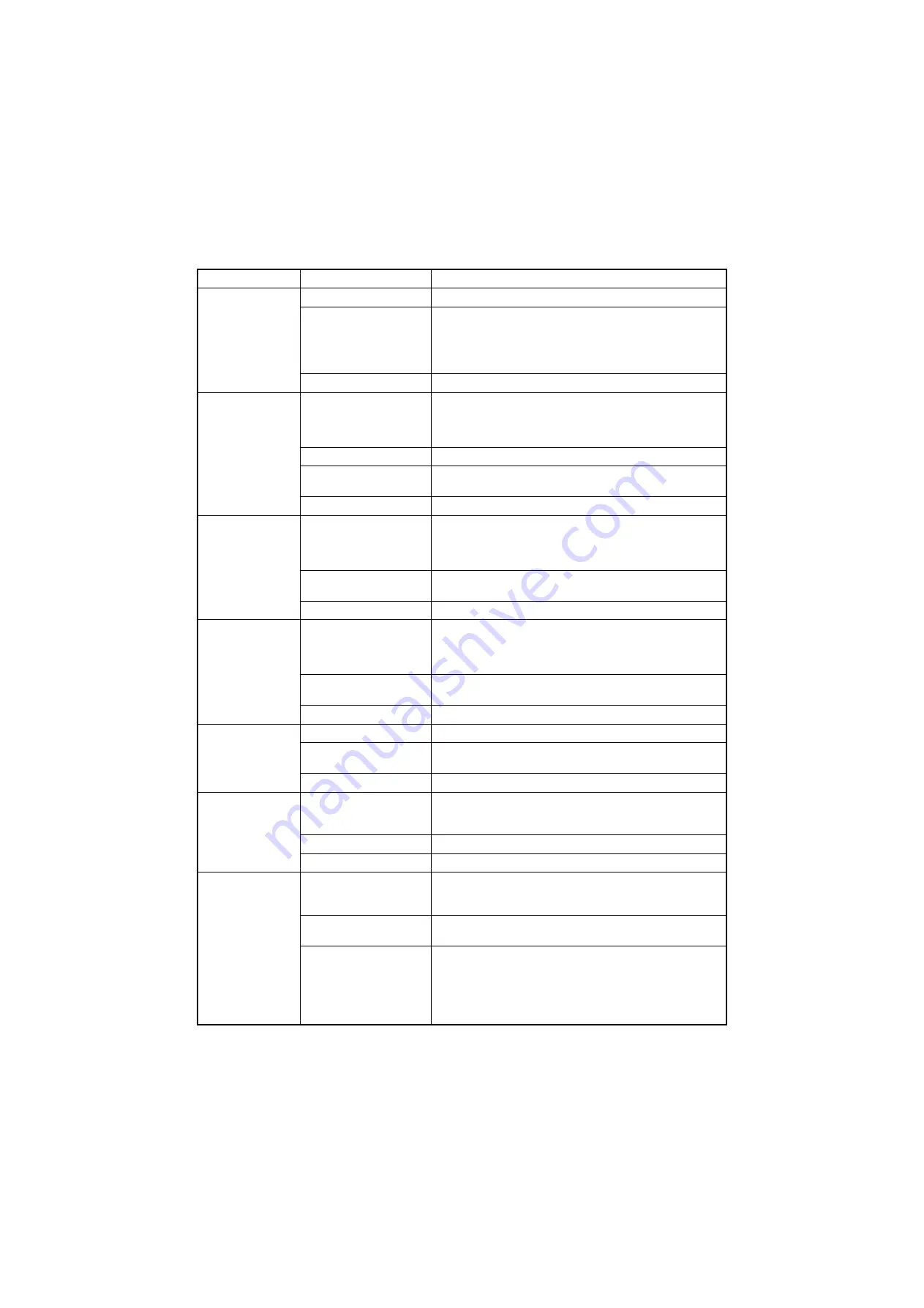
2PR
1-4-36
(5)MP paper feed
solenoid, ID solenoid,
duplex solenoid do
not operate.
Broken solenoid coil.
Check for continuity across the coil. If none, replace the solenoid.
Defective harness or
improper connector inser-
tion.
Reinsert the connector. Also check for continuity within the con-
nector harness. If none, remedy or replace the harness.
MP paper feed solenoid - Engine PWB (YC40)
ID solenoid - Engine PWB (YC617)
Duplex solenoid - Engine PWB (YC3)
Defective engine PWB.
Replace the engine PWB (See page 1-5-28).
(6)Main charging is
not performed.
Defective harness or
improper connector inser-
tion.
Reinsert the connector. Also check for continuity within the con-
nector harness. If none, remedy or replace the high voltage PWB
1 (See page 1-5-34).
High voltage PWB 1 - Engine PWB (YC600)
Defective main charger unit Replace the main charger unit (See page 1-5-15).
Defective high voltage PWB
1.
Replace the high voltage PWB 1 (See page 1-5-34).
Defective engine PWB.
Replace the engine PWB (See page 1-5-28).
(7)No developing
bias is output.
Defective harness or
improper connector inser-
tion.
Reinsert the connector. Also check for continuity within the con-
nector harness. If none, remedy or replace the high voltage PWB
1 (See page 1-5-34).
High voltage PWB 1 - Engine PWB (YC600)
Defective high voltage PWB
1.
Replace the high voltage PWB 1 (See page 1-5-34).
Defective engine PWB.
Replace the engine PWB (See page 1-5-28).
(8)Transfer charging
is not performed.
Defective harness or
improper connector inser-
tion.
Reinsert the connector. Also check for continuity within the con-
nector harness. If none, remedy or replace the high voltage PWB
2 (See page 1-5-41).
High voltage PWB 2 - Engine PWB (YC610)
Defective high voltage PWB
2.
Replace the high voltage PWB 2 (See page 1-5-41).
Defective engine PWB.
Replace the engine PWB (See page 1-5-28).
(9)The message
requesting paper to
be loaded is shown
when paper is pres-
ent in the cassette.
Defective paper sensor 1/2. Replace the engine PWB (See page 1-5-28).
Broken paper sensor 1/2
actuator.
Check the bending of the actuator lever of the paper sensor 1/2 if
there is trouble, remedy or replace.
Defective engine PWB.
Replace the engine PWB (See page 1-5-28).
(10)The message
requesting paper to
be loaded is shown
when paper is pres-
ent in the MP tray.
Defective harness or
improper connector inser-
tion.
Reinsert the connector. Also check for continuity within the con-
nector harness. If none, remedy or replace the harness.
MP tray sensor - Engine PWB (YC21)
Defective MP tray sensor.
Replace the MP tray sensor.
Defective engine PWB.
Replace the engine PWB (See page 1-5-28).
(11)The size of paper
in the cassette is not
displayed correctly.
Defective harness or
improper connector inser-
tion.
Reinsert the connector. Also check for continuity within the con-
nector harness. If none, remedy or replace the harness.
Cassette size switch - Engine PWB (YC9)
Defective cassette size
switch.
Replace the cassette size switch.
Defective engine PWB.
Replace the engine PWB (See page 1-5-28).
Problem
Causes
Check procedures/corrective measures
Summary of Contents for ECOSYS P7035cdn
Page 1: ...SERVICE MANUAL Published in May 2014 842PR111 2PRSM061 Rev 1 ECOSYS P7035cdn...
Page 4: ...This page is intentionally left blank...
Page 10: ...This page is intentionally left blank...
Page 14: ...2PR This page is intentionally left blank...
Page 20: ...2PR 1 1 6 This page is intentionally left blank...
Page 28: ...2PR 1 2 8 This page is intentionally left blank...
Page 48: ...2PR 1 3 20 This page is intentionally left blank...
Page 154: ...2PR 2 1 20 This page is intentionally left blank...
Page 177: ......
Page 178: ......