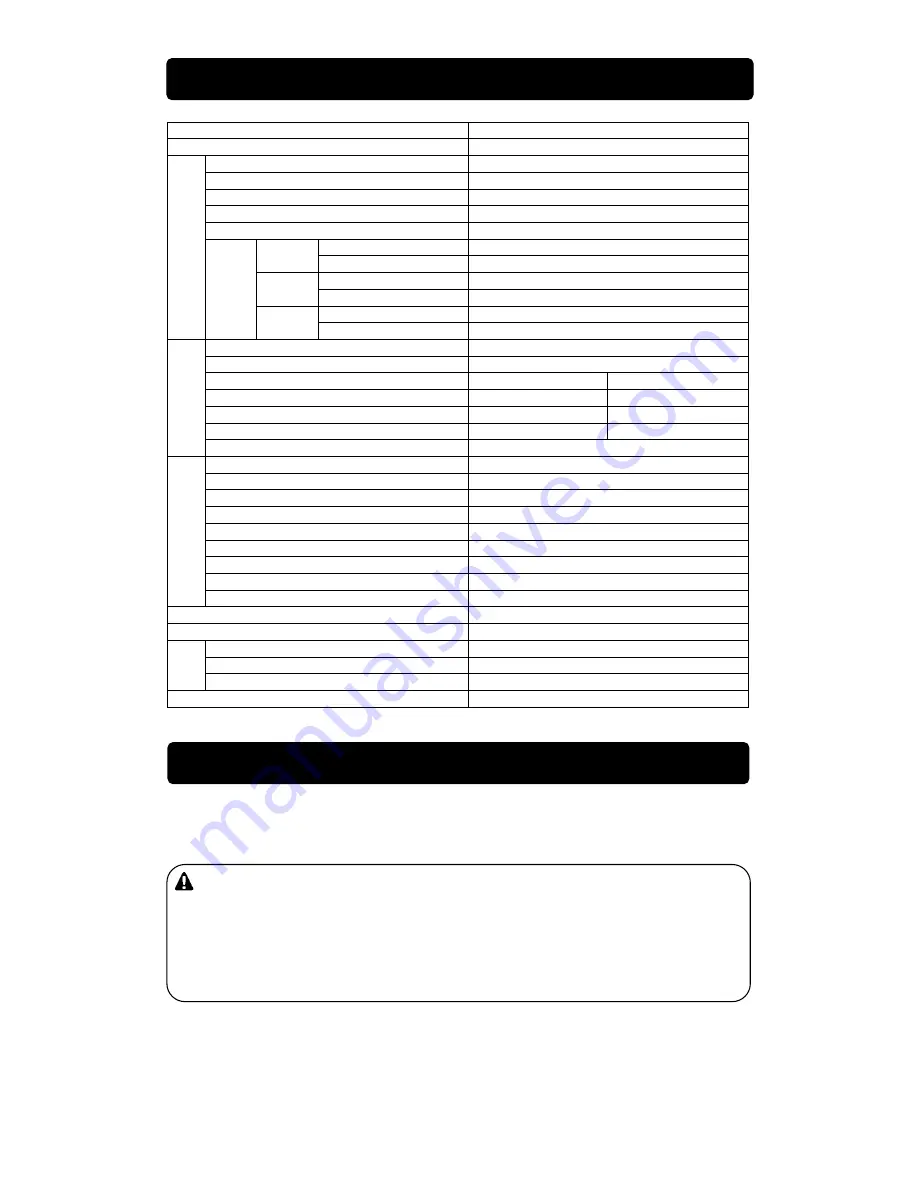
- 5 -
Model
DGW400DM
Generating Method
Rotating Field
Rated Current (A)
370 / 390
Rated Voltage (V)
34.8 / 35.6
Duty Cycle (%)
60
Rated Speed (min
-1
)
3000 / 3600
No Load Voltage (V)
MAX 85
Current Adj. Range (A)
90 – 380 / 110 - 400
Single
Welding Rod (
Ф
)
2.6 - 8.0
Current Adj. Range (A)
50 – 190 / 55 - 210
Dual
Welding Rod (
Ф
)
2.0 - 4.0
Current Adj. Range (A)
40 - 240
W
e
ld
in
g
G
e
n
e
ra
to
r
O
u
tp
u
t
C
h
a
n
g
e
Eco
Welding Rod (
Ф
)
2.0 - 5.0
Rated Frequency (Hz)
50 / 60
Rated Speed (min
-1
)
3000 / 3600
Phase
1-Phase
3-Phase
Rated Voltage (V)
220-240
380-415
Power Factor
1.0
0.8
Rated Output (kVA)
3
15
A
C
G
e
n
e
ra
to
r
Rating
Continuous
Model
Kubota D1005
Type
Vertical, Water-Cooled 4-Cycle Diesel Engine
Displacement (L)
1.001
Rated Output (kW/min
-1
)
16.5 / 3000 or 19.1 / 3600
Fuel
ASTM No.2-D Diesel Fuel or Equivalent
Lubricant Oil
API Class CC or better
Lubrication Oil Volume (L)
5.1 (Effective 1.4)
Cooling Water Volume (L)
4.3 (Sub Tank Capacity 0.6 L included)
E
n
g
in
e
Starting Method
Starter Motor
Battery
55B24L (Japanese Industrial Standard)
Fuel Tank Capacity (L)
37
Length (mm)
1519
Width (mm)
700
D
im
e
n
-
s
io
n
Height (mm)
760
Dry Weight (kg)
469
•
Arc Welding
•
Electric Tools and Home Appliances
•
Power Source for lights
Caution: Damage to the equipment or other properties
•
The equipment is designed for the above purposes only. Do not use it for the
other purpose. When it will be used for the equipment with the microcomputers
control or for the ultra-precision devices, the load may be malfunctioned.
•
Whenever connecting to use medical equipment or appliances, be sure to consult
with the medical equipment company, doctor or hospital personnel.
2. Specifications
3. Use
Summary of Contents for dgw400dm
Page 2: ......
Page 36: ... 33 14 Engine Wiring Diagram ...
Page 37: ... 34 15 Generator Wiring Diagram ...
Page 38: ......
Page 39: ......
Page 40: ... 2013 ...