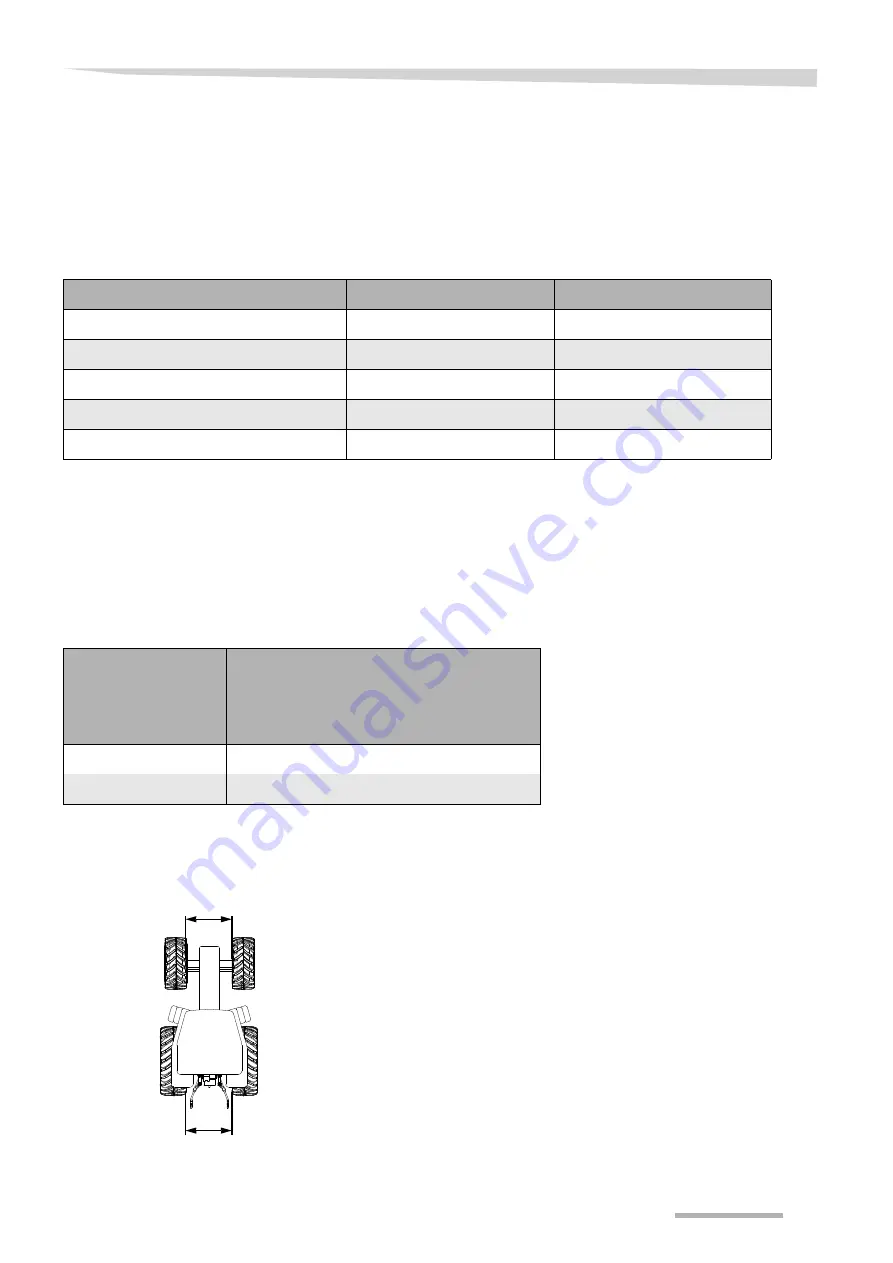
Preparation for use
27
Preparation for use
This chapter details how to prepare the plow and tractor before putting
the plow into operation.
Tractor
Hydraulic connections
The following table shows the tractor’s required connections.
We recommend the tractor's hydraulic output flow is 25-35 l/min.
(6.6- 9.2 gpm)
Depth control
We recommend setting the tractor’s depth control as shown in the fol
-
lowing table. The soil and field conditions determine the precise set
-
tings.
Track
•
To use the plow, the tractor’s internal rear track (the distance be
-
tween the internal edges of the rear wheels) must be 110–160 cm
(43-63 inches).
•
The internal front track (between the front wheels) must be 0 to 10
cm (0-4 inches) wider.
•
The rotating mechanism can be mounted in two ways on the plow,
depending on the distance between the rear wheels.
Hydraulic functions
Single-acting
Double-acting
Turnover
1
Hydraulic furrow width [+]
1
Hydraulic first furrow width [+]
1
Hydraulic depth wheel [+]
1
Hydraulic release system [+]
1
Plow size
Depth control of the plow
Initial settings
Tractive-power-regulated depth control
Position control<------------> Drag control
2–3 furrows
|----------------------------------X------------|
4–6 furrows
|----------------------X------------------------|
110–160 cm
(43-63 inches)
0–10 cm (0-4 inches) wider than the rear
Summary of Contents for ES
Page 9: ...Safety 9 ...