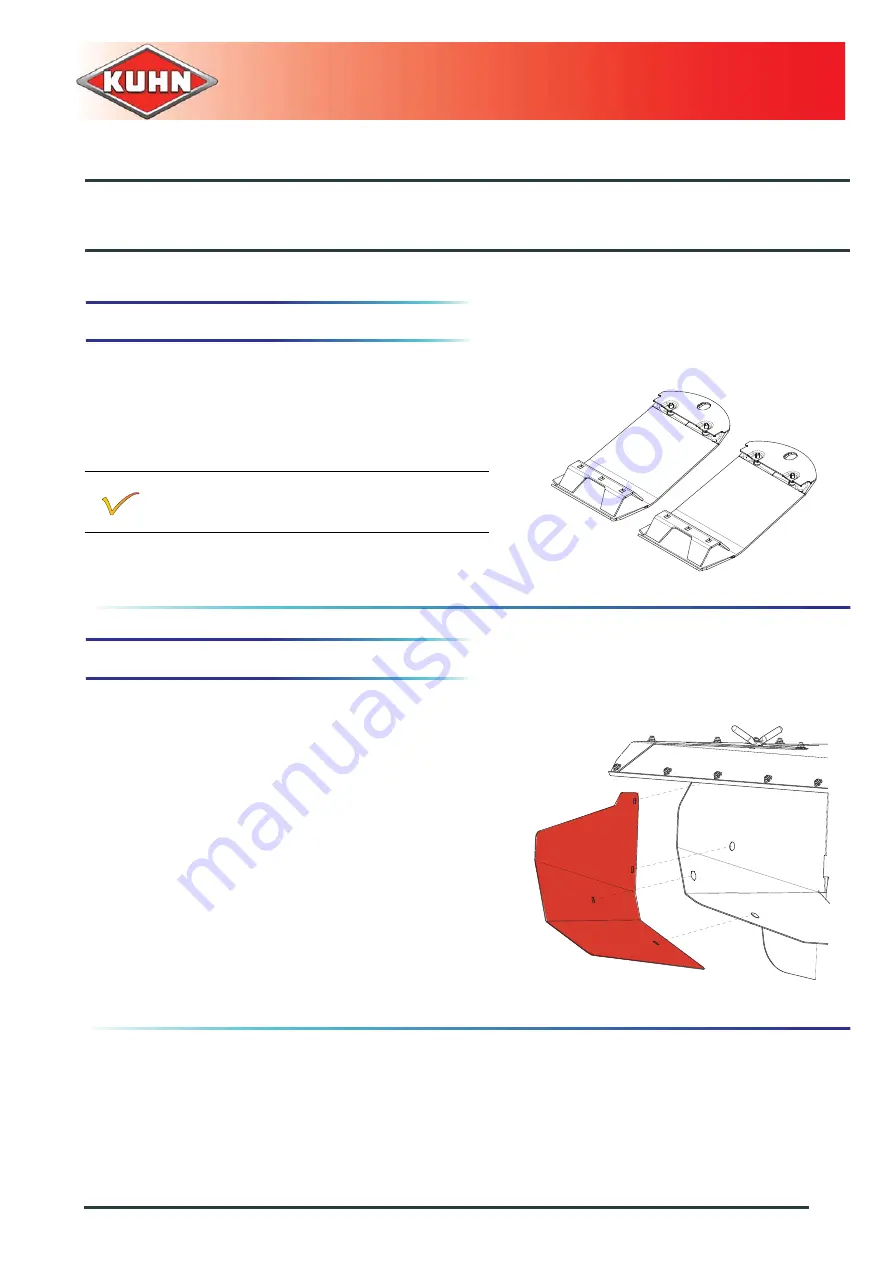
9. - Optional equipment
FC244R / FC244R HD
69
KN330CGB_A
Mower conditioner
9. Optional equipment
9.1
Raised skid shoes
9.2
Swath shield extensions
The raised skids shoes allow mowing higher,
between 60 and 120 mm (2.4’’ - 4.7’’).
- Replace the end disc skids by the 2 raised skid
shoes.
The use of raised skid shoes is also
recommended on sticky grounds.
The swath shield extensions allow reducing the
swath width to approximately 1 m (3’3’’).