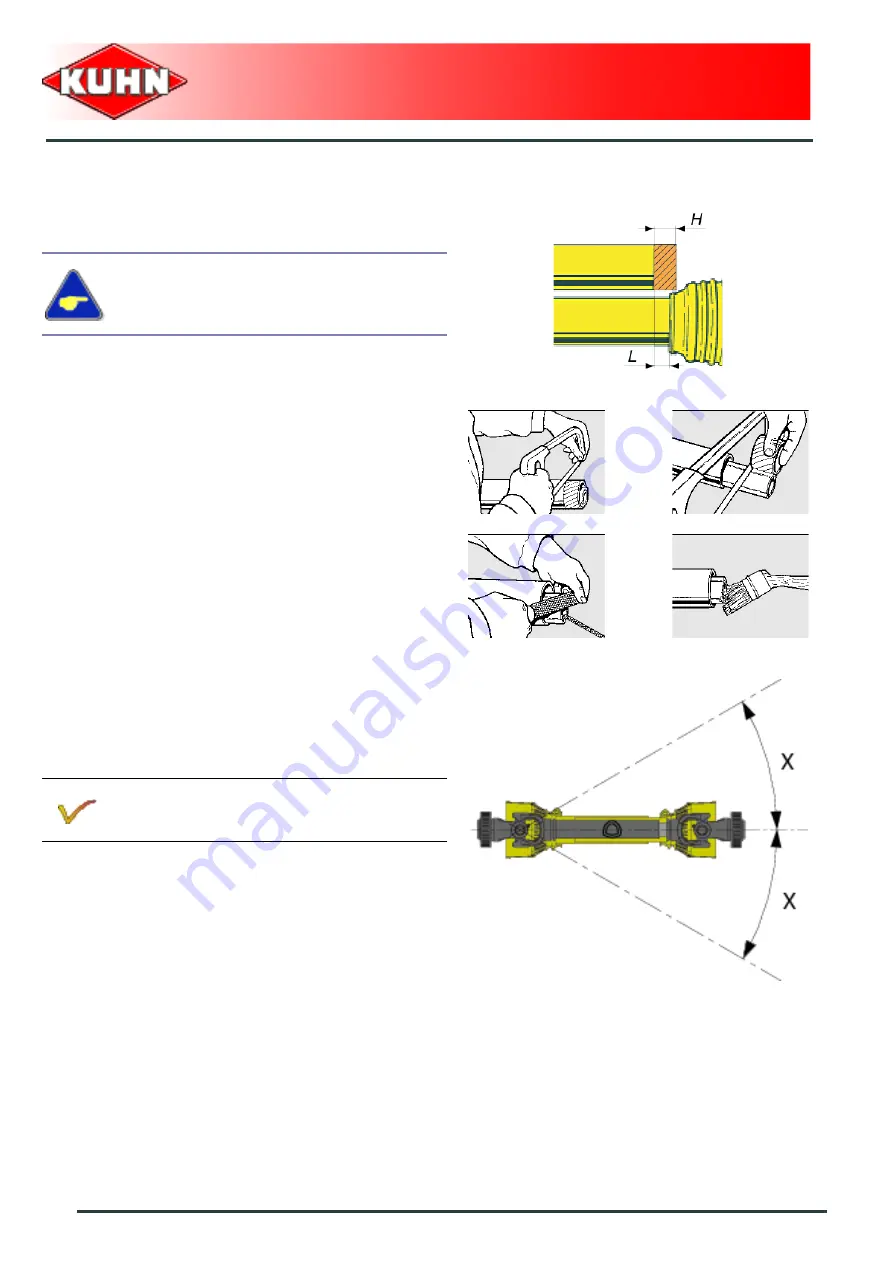
Silo unloader - Straw Spreader
48
ALTOR 4560
Putting into service
PTO shaft
Separate the two half PTO shafts and connect them to
the machine's input shaft and to the tractor PTO stub.
- Check the length of the PTO shaft:
• Check the maximum overlap when the machine is in
transport position and the tractor turned to the
direction which provides maximum overlap.
• When the PTO shaft is in its maximum overlap
position (retracted), tubes should not butt against
the yokes. As a safety measure, a clearance (L) of
at least 25 mm (1’’) must be maintained.
• When the PTO shaft is in its maximum extended
position, the tube overlap must be more than
330 mm (13’’)
- If this is not the case:
• Mark length (H) to cut when the transmission is the
maximum overlap position.
• Shorten the guard tubes and the transmission tubes
by the same length.
• Bevel and clean the tubes.
• Grease the inside of the outer tube.
- The cardan drive shaft must not work at an angle X:
• More than 15° for a standard joint
• More than 25° for a homokinetic joint
Make sure that the PTO shaft is correctly
adjusted, to avoid premature wear and tear.
Check that there is still a minimum overlap of
330 mm (13’’) when the machine is in working
position and the tractor in line with the machine.
Summary of Contents for ALTOR 4560
Page 2: ......
Page 19: ...Safety Silo unloader Straw Spreader ALTOR 4560 17...
Page 26: ...Silo unloader Straw Spreader 24 ALTOR 4560 Machine specifications 2 Technical specifications...
Page 97: ......
Page 98: ......