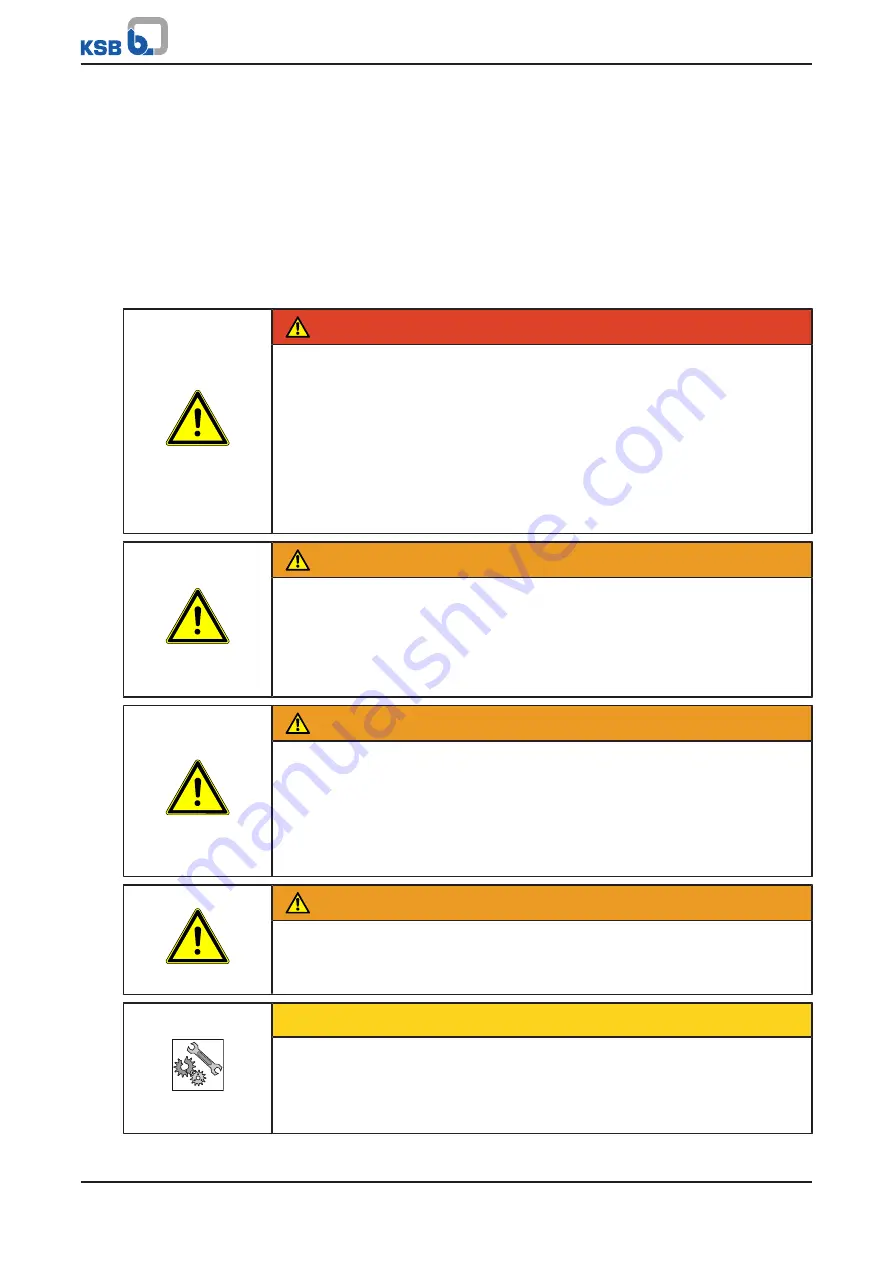
6 Commissioning/Start-up/Shutdown
59 of 116
CHTRa
▪
The cooling liquid temperature at the outlet must not exceed 55 °C.
▪
All temperatures indicated are below the limit values.
▪
In the case of a pump set with variable speed coupling, check the scoop tube
position for compliance with the manufacturer’s product literature and re-adjust,
if required.
▪
Check all guards for correct fastening.
▪
Monitor the bearing oil temperature. Make sure that the limits are not exceeded.
(
6.3.3 Start-up and trial run
DANGER
Non-compliance with operating limits for pressure, temperature, fluid handled and
speed
Hot or toxic fluid could escape!
Explosion hazard!
▷
Comply with the operating data indicated in the data sheet.
▷
Avoid prolonged operation against a closed shut-off element.
▷
Never operate the pump at temperatures exceeding those specified in the data
sheet or on the name plate unless the written consent of the manufacturer has
been obtained.
WARNING
Sound pressure level above 85 dB(A) when starting up the pump set
Injury to or impairment of hearing!
▷
Wear ear protection.
▷
Access to the pump set is permitted to authorised specialist personnel only.
▷
Observe the applicable local occupational health and safety regulations.
WARNING
Failure of seal elements on suction and discharge nozzles and other pressurised
parts
Risk of personal injury in the event that hot, pressurised fluid handled escapes!
▷
Wear safety goggles.
▷
Check seal elements regularly.
▷
Access to the pump is permitted to authorised specialist personnel only.
WARNING
Hot surfaces - Pump and piping take on the temperature of the fluid handled.
Risk of burns!
▷
Do not touch hot surfaces.
CAUTION
Abnormal noises, vibrations, temperatures or leakage
Damage to the pump!
▷
Switch off the pump (set) immediately.
▷
Eliminate the causes before returning the pump set to service.