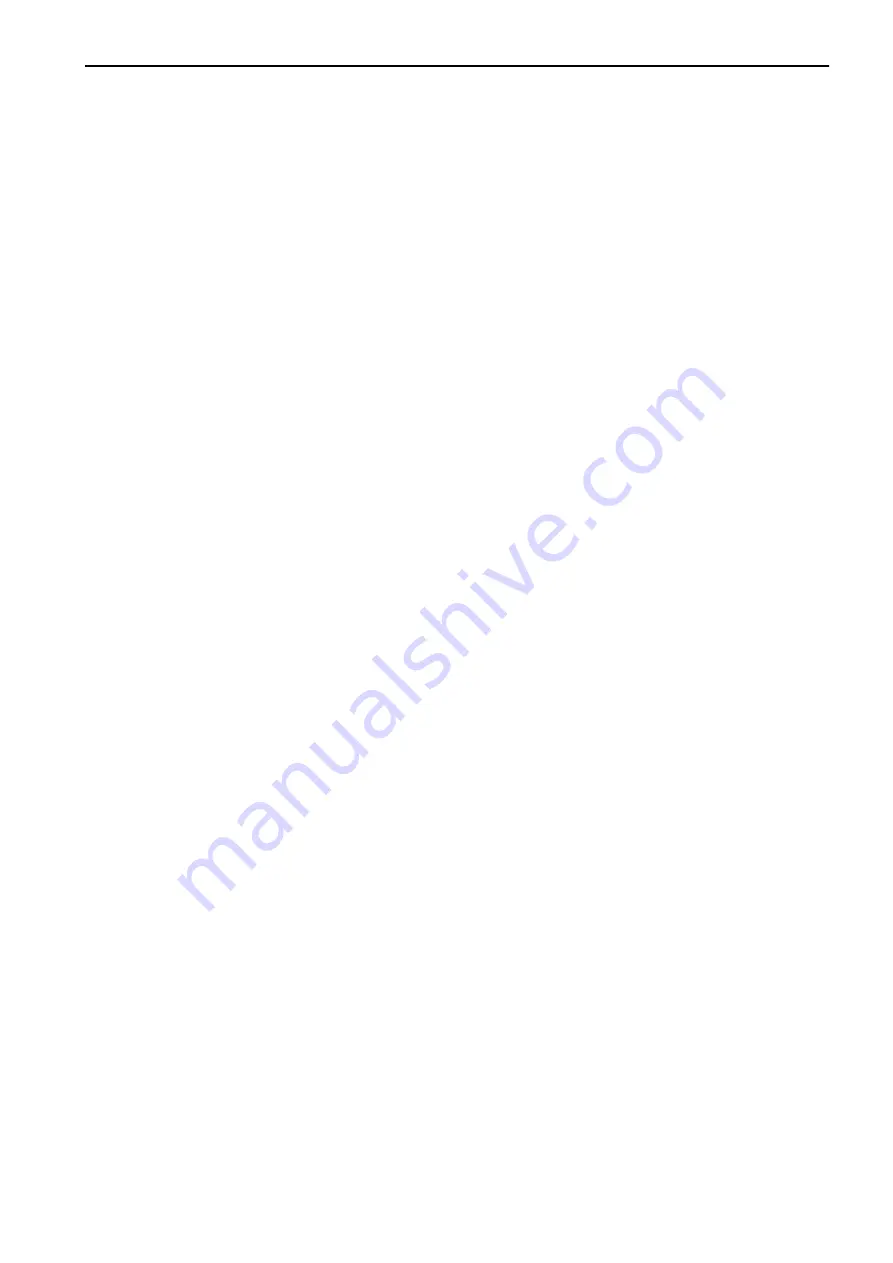
PRECAUTIONS FOR WELDING ....................................................................................................... 4-2
DO NOT DROP THINGS INSIDE MACHINE ..................................................................................... 4-2
DUSTY JOBSITES............................................................................................................................. 4-2
AVOID MIXING OIL............................................................................................................................ 4-3
LOCK INSPECTION COVERS .......................................................................................................... 4-3
BLEED AIR FROM HYDRAULIC CIRCUIT ........................................................................................ 4-3
PRECAUTIONS WHEN INSTALLING HYDRAULIC HOSES ............................................................. 4-3
CHECKS AFTER INSPECTION AND MAINTENANCE...................................................................... 4-3
FUEL AND LUBRICANTS TO MATCH THE AMBIENT TEMPERATURE........................................... 4-3
CLOSE ENGINE HOOD SECURELY................................................................................................. 4-3
OUTLINE OF MAINTENANCE.................................................................................................................. 4-4
HANDLE OIL, FUEL, COOLANT, AND PERFORMING OIL CLINIC .................................................. 4-4
HANDLE ELECTRICAL COMPONENTS ........................................................................................... 4-7
STANDARD TIGHTENING TORQUE FOR BOLTS AND NUTS................................................................ 4-8
MAINTENANCE SCHEDULE.................................................................................................................. 4-10
MAINTENANCE SCHEDULE TABLE............................................................................................... 4-10
MAINTENANCE INTERVAL FOR HYDRAULIC BREAKER ..............................................................4-11
MAINTENANCE PROCEDURE .............................................................................................................. 4-13
INITIAL 50 HOURS MAINTENANCE (ONLY AFTER THE FIRST 50 HOURS) ................................ 4-13
INITIAL 100 HOURS MAINTENANCE (ONLY AFTER THE FIRST 100 HOURS) ............................ 4-13
INITIAL 250 HOURS MAINTENANCE (ONLY AFTER THE FIRST 250 HOURS) ............................ 4-13
INITIAL 500 HOURS MAINTENANCE (ONLY AFTER THE FIRST 500 HOURS) ............................ 4-13
WHEN REQUIRED .......................................................................................................................... 4-13
CHECKS BEFORE STARTING........................................................................................................ 4-35
EVERY 100 HOURS MAINTENANCE ............................................................................................. 4-35
EVERY 250 HOURS MAINTENANCE ............................................................................................. 4-38
EVERY 500 HOURS MAINTENANCE ............................................................................................. 4-45
EVERY 1000 HOURS MAINTENANCE ........................................................................................... 4-59
EVERY 2000 HOURS MAINTENANCE ........................................................................................... 4-67
EVERY 4000 HOURS MAINTENANCE ........................................................................................... 4-78
EVERY 5000 HOURS MAINTENANCE ........................................................................................... 4-80
SPECIFICATIONS ........................................................................................................................................... 5-1
SPECIFICATIONS .................................................................................................................................... 5-2
LIFTING CAPACITIES .............................................................................................................................. 5-6
ATTACHMENTS AND OPTIONS ..................................................................................................................... 6-1
PRECAUTIONS WHEN SELECTING ................................................................................................ 6-2
READ THE OPERATION AND MAINTENANCE MANUAL THOROUGHLY....................................... 6-2
PRECAUTIONS WHEN REMOVING AND INSTALLING ................................................................... 6-2
PRECAUTIONS WHEN USING ......................................................................................................... 6-2
QUICK COUPLER SYSTEM..................................................................................................................... 6-4
HANDLING QUICK COUPLER .......................................................................................................... 6-4
HANDLE BUCKET WITH HOOK............................................................................................................... 6-8
PRECAUTIONS FOR OPERATION ................................................................................................... 6-8
HANDLE MACHINE READY FOR INSTALLATION OF ATTACHMENT .................................................... 6-9
EXPLANATION OF COMPONENTS .................................................................................................. 6-9
HYDRAULIC CIRCUIT......................................................................................................................6-11
METHOD FOR REMOVING AND INSTALLING ATTACHMENT .......................................................6-11
METHOD FOR OPERATING ATTACHMENT................................................................................... 6-16
LONG-TERM STORAGE ................................................................................................................. 6-18
SPECIFICATIONS ........................................................................................................................... 6-19
ATTACHMENTS AND OPTIONS ............................................................................................................ 6-20
INSTALL ATTACHMENT.................................................................................................................. 6-20
RECOMMENDED ATTACHMENT OPERATIONS................................................................................... 6-21
HYDRAULIC BREAKER .................................................................................................................. 6-21
REPLACEMENT PARTS.................................................................................................................................. 7-1
PERIODIC REPLACEMENT OF DEFINED LIFE PARTS.......................................................................... 7-2
DEFINED LIFE PARTS LIST.............................................................................................................. 7-3
FOREWORD
TABLE OF CONTENTS
1-17
WENAM00061
Summary of Contents for PW98MR-10
Page 1: ......
Page 2: ......
Page 9: ...Do not repeatedly handle and lift loads FOREWORD VIBRATION LEVELS 1 7 WENAM00061...
Page 68: ...WENAM00061...
Page 73: ...CONTROLS AND GAUGES NAMES OPERATION GENERAL VIEW 3 5 WENAM00061...
Page 157: ...SWITCHES OPERATION EXPLANATION OF COMPONENTS 3 89 WENAM00061...
Page 388: ...WENAM00061...
Page 389: ...SPECIFICATIONS 5 1 WENAM00061...
Page 392: ...RKA55390 SPECIFICATIONS SPECIFICATIONS 5 4 WENAM00061...
Page 402: ...WENAM00061...
Page 428: ...WENAM00061...
Page 429: ...REPLACEMENT PARTS 7 1 WENAM00061...
Page 445: ......
Page 446: ......