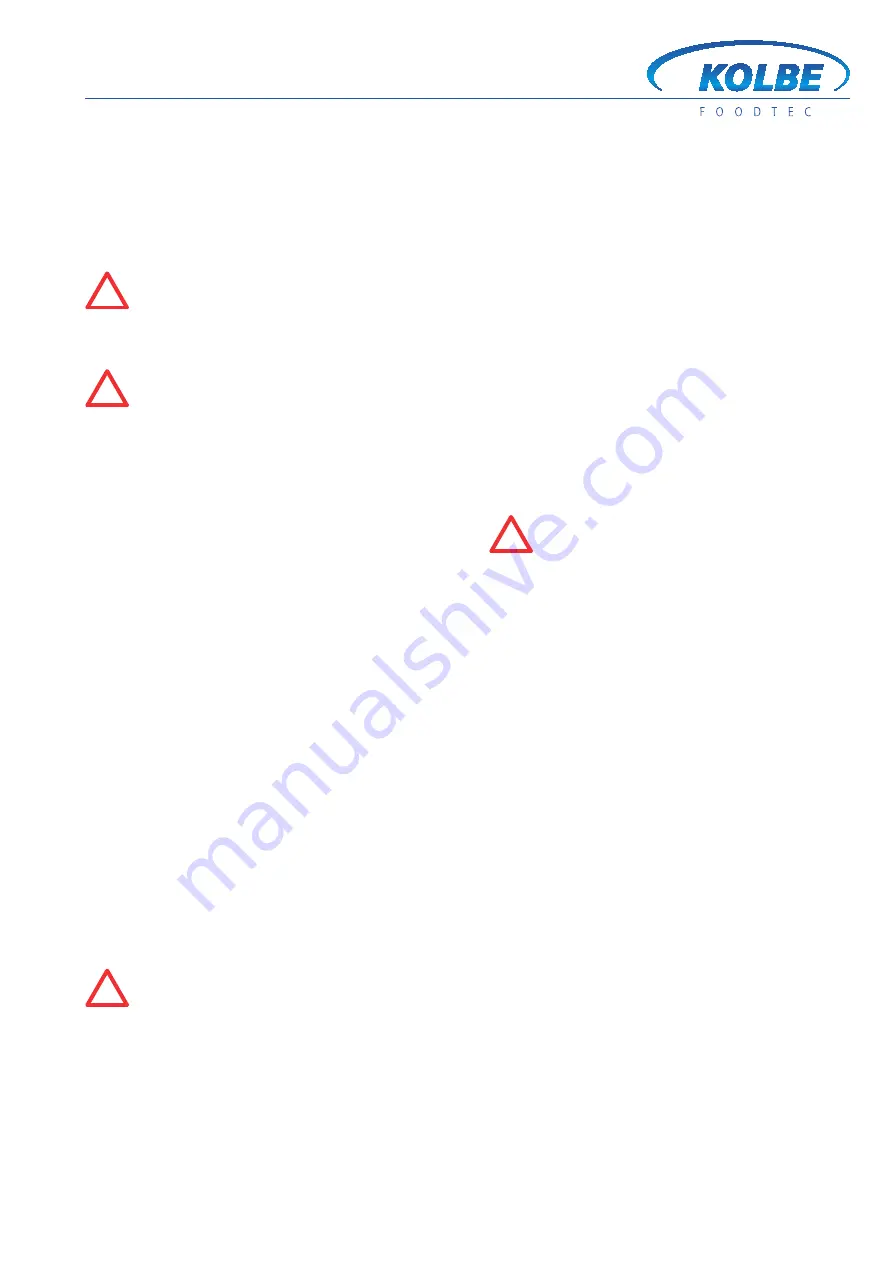
9
mixing blade bracket (36) towards the front while rotating
it slightly to the right and while simultaneously holding the
mixing blade (37) firmly with the other hand.
-
Pull the mixing blade (37) out of the rear attachment and
remove it by tilting it slightly upwards.
-
Installation takes place in the reverse sequence
Ensure the proper assembly and secure
attachment of the mixing blade bracket (36) at
all times!
6.12 Insertion of the coded cutting set variants
Only outlet-sided perforated discs with a max.
bore hole diameter of 8.0 mm are to be used with
the coded cutting system. For safety reasons,
regrinding of the discs is permissible only to a disc
thickness of 8 mm!
Fault-free operation of the meat mincer is warranted only
when the cutting tools are properly inserted.
(See the pictures on pages 16+17)
Enterprise cutting system, size E 32 - coded
-
Perforated disc with 4 slots and hub (18)
-
Cross knife (19)
The locking nut (6) must be tightened
firmly
using the
combination hook wrench (34) / (38) so the cross knife (19)
lies securely on the perforated disc (18). Only then can a
clean-cut of the minced meat be warranted.
Unger cutting system, size D 114 - coded
-
Pre-cutter (24)
-
Cross knife (27)
-
Perforated disc, coarse incl. 1 slot (25)
-
Cross knife (27)
-
Perforated disc, fine incl. 2 slots (26)
-
Insert ring incl. stub (28 or 29)
Tighten the locking nut (6) by
hand only
so the cross knife
(27) will lie on the perforated discs (24, 25, 26) and cut
without causing excessive abrasion.
The combination hook wrench (34) / (38) must be used
only for opening the Unger locking nut.
6.13 Insertion of the uncoded cutting set variants
Use of the uncoded cutting system is permitted
only in conjunction with the use of a housing
outlet protective cover (10), meaning that outlet-
sided perforated discs with a max. bore hole diameter
of greater than 8.0 mm may also be used. For safety
reasons, regrinding of the discs is permissible only to a
disc thickness of 8 mm!
Fault-free operation of the meat mincer is warranted only
when the cutting tools are properly inserted.
(See the pictures on pages 16+17)
Enterprise cutting system, size E 32
-
Perforated disc with 3 slots and hub (18)
-
Cross knife (19)
The locking nut (6) must be tightened
firmly
using the
combination hook wrench (34) / (38) so the cross knife (19)
lies securely on the perforated disc (18). Only then can a
clean-cut of the minced meat be warranted.
Unger cutting system, size D 114
-
Pre-cutter (24)
-
Cross knife (27)
-
Perforated disc, coarse (25)
-
Cross knife (27)
-
Perforated disc, fine (26)
-
Insert ring (28 or 29)
Tighten the locking nut (6) by
hand only
so the cross knife
(27) will lie on the perforated discs (24, 25, 26) and cut
without causing excessive abrasion.
The combination hook wrench (34) / (38) must be used
only for opening the Unger locking nut.
Please note that the perforated discs and cross
knives are parts subject to wear. They will require
regrinding at time intervals determined by and
adapted to the operating conditions. Only sharp tools
provide a good cut while conserving the knife studs (17
or 23), as well as the overall machine.
6.14 Housing outlet protective cover (optional)
To comply with applicable safety regulations, the use of a
housing outlet protective cover (10) is absolutely essential
when using outlet-sided perforated discs with bore hole
diameters greater than 8.0 mm. It covers the outlet-sided
perforated disc and thereby prevents direct access to the
perforated disc by fingers or hands. A magnetic sensing
safety device on housing outlet protective cover (10)
switches the meat mincer automatically OFF as soon as it is
opened and prevents it from being switched ON unless the
protective outlet cover is closed.
When opened, the housing outlet protective cover can be
removed for cleaning purposes towards the front.
As safety regulations evolve, it is possible that the use
of housing outlet protective covers overall will become
compulsory at some point.
6.15 Motor protection
The machine contactor control is outfitted with overcurrent
relays. In the event of an overload resulting in an inadmissible
increase in current consumption in the motor windings, the
machine will automatically shutdown.
This is the case, for example, with phase failure, insufficient
cooling or machine blockage.
If the automatic overcurrent relays have triggered, they will
reactivate automatically after a cooling-down period.
The machine can then be switched back ON.
If the cause of the overload has not been rectified, however,
the overcurrent relays will trigger once again after a short
period of time.
In the event of frequency converter control of the machine,
!
!
!
!