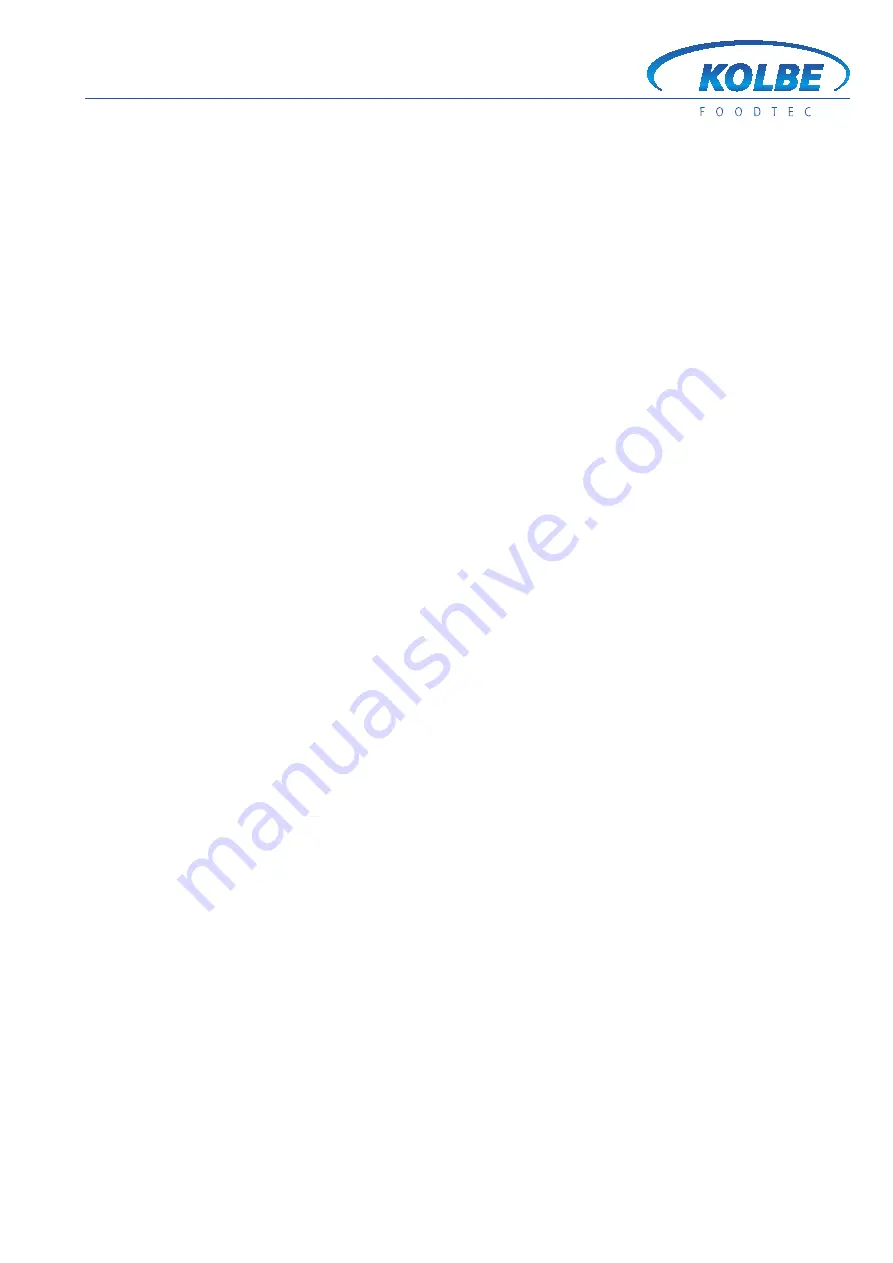
5
• The risk exists of crushing, shearing-off and jamming
of fingers, hands, feet or other body parts when .... or
between .... :
-
Assembling or disassembling cutting set parts
-
Assembling or disassembling the locking nut, mincer feed
screw, mincer housing, splatter guard, housing outlet
protective cover, feeder screw, mixing arm, loosening
shaft, as well as all removable parts
-
Working with the combination hook wrench
-
Closing the hopper cover or hopper attachment
-
The batching trolley and the lift/tilt pylon
-
The batching trolley and a wall or other objects
-
Releasing the locking devices on mobile models
-
Plugging or unplugging CEE plug connections
-
Disassembled parts falling or toppling
-
All moveable and stationary parts
• The risk of jamming or crushing exists due to machine
toppling, in particular on the mobile models.
• The risk of crushing exists between the mobile machine
and walls or other objects, as well as between the floor
and the castors.
• The risk of being drawn in, crushing or shearing-off of
fingers or hands exists during maintenance and inspection
work at the machine drive component intake areas with
opened inspection covers.
2.2 Hazard due to instability
• The risk exists to bodily parts due to impact or crushing,
in particular when the machine is mobile or topples.
Always bear in mind the need for a secure foundation
and stable flooring when installing the machine!
2.3 Electrical hazards
• The risk of injury exists due to direct or indirect contact
with electricity.
• The risk of injury exists due to defective electrical
components or malfunction.
2.4 Noise hazards
Risk of hearing loss due to noise emissions greater than 80
dB(A). With the meat mincers MWK32-45 / MWK114-45,
MWK32-80 / MWK114-80, MW32-80 / MW114-80 the noise
level at idle / sound pressure level has been determined
according to EN ISO 3746:2011 (constant K=4 dB) to be 70
dB(A), and this results in a sound power level of 80 dB(A).
The values set forth are emission values and do not
necessarily represent safe values for the workplace. Although
there is a correlation between emission and immission
levels, a reliable conclusion as to whether additional safety
precautions are necessary according to EN ISO 11690-
1/-2 cannot be drawn. Factors present at the workplace,
which would influence immission levels, could relate to the
peculiarities of the workshop, itself, and other noise sources,
such as the number of machines and neighbouring work
processes, as well as non-standard operating conditions.
The allowable levels at the workplace can vary from country
to country. Nonetheless, this information should help the
user to better estimate the hazards and risks involved.
With a noise level of > 80 dB(A), the operator must take
appropriate precautions for hearing protection, such as
mandating the use of earplugs or other hearing protection
devices.
2.5 Hazards to health
The risk of harm to human health exists due to low ambient
temperatures. Thermal protective clothing should be worn
at ambient temperatures < 7 °C.
2.6 Hazards due to neglect of
hygienic principles and cleaning instructions:
• The risk of harm to human health and unacceptable
change in the foodstuffs being processed, such as:
-
Spoilage of foodstuffs (food poisoning!)
-
Internal chemical burns suffered by the consumer due to
cleaning and disinfectant agent residue in the foodstuffs
-
Internal injuries to the consumer due to a foreign object
-
(e.g. machine parts or parts from other origins)
2.7 Predictable operator error
• Non-compliance with installation instructions
• Non-adherence to operator instructions
• Non-observance of danger notices
• Non-compliance with shutdown procedures
• Non-observance of operating instructions
• Non-observance of cleaning instructions
• Non-compliance with maintenance intervals
• Non-adherence to utilisation according to intended
purpose