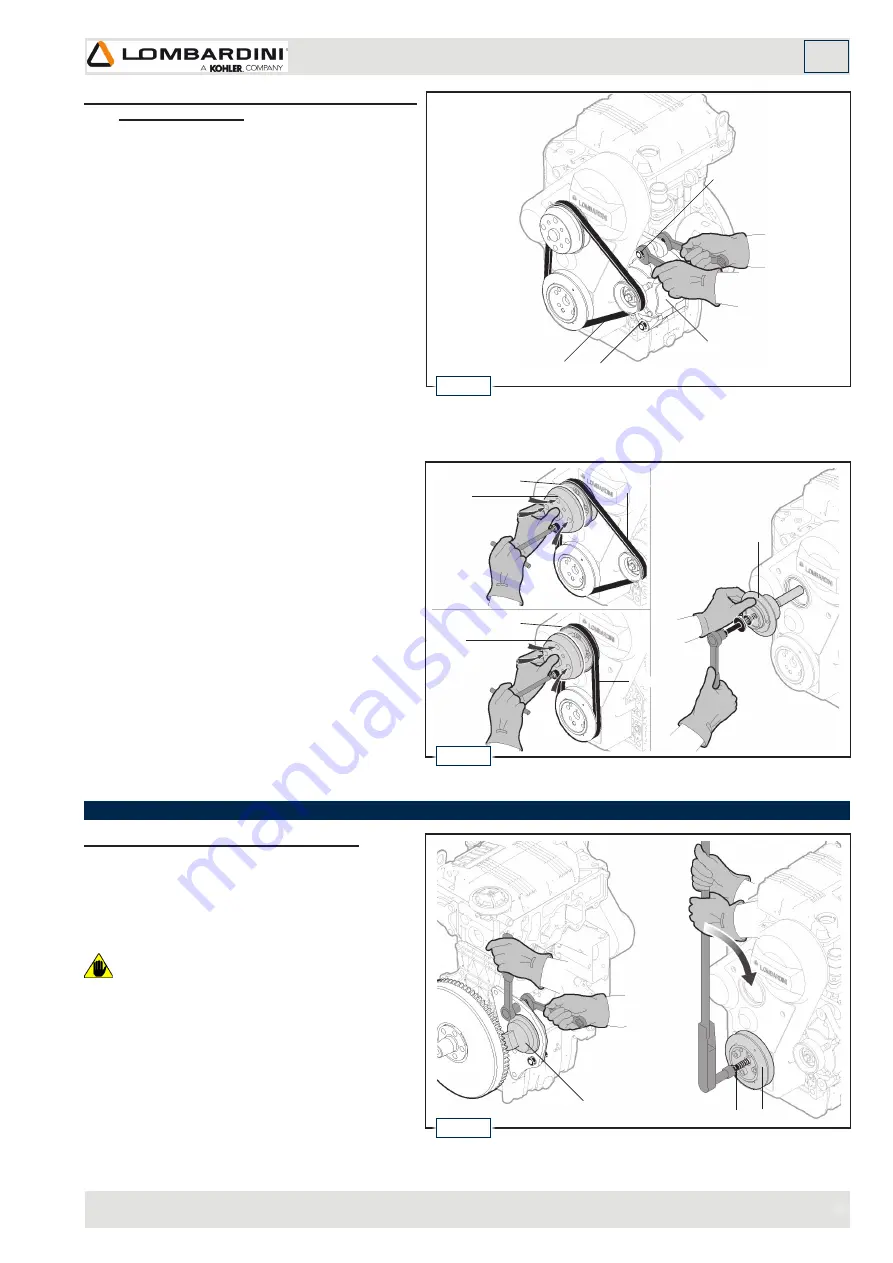
33
D
B
C
B1
G H
D
E
E
F
D
5
19
20
21
Service Manual LDW FOCS 502 automotive _ cod. ED0053027270 - 3° ed_rev. 02
5.4 REMOVING THE TIMING BELT
5.3.1 Disassembling the cooling fan belt (with
external alternator)
1. Loosen the nuts (
B - B1
).
2. Loosen the belt (
D
) by adjusting the alternator (
C
)
manually.
3. Remove the belt (
D
).
5.4.1 Disassembling the timing belt casing
1. Disassemble the starter motor.
2. Install tool “7107-1460-051” to inhibit rotation of the
crankshaft.
3. Loosen the screw (
G
).
Warning
• The screw is left-handed. Turn clockwise to unscrew.
4. Remove the hub (
E
) and flange.
5. Remove the pulley (
F
), washers and spacer.
5.3.2 Disassembling the cooling fan belt (with internal
alternator)
1. Remove the hub (
E
) and flange.
2. Remove the belt (
D
).
3. Remove the pulley (
F
), washers and spacer.
pulley flange
pulley flange
tool 7107-1460-051
REMOVING THE ASSEMBLIES
Summary of Contents for Lombardini LDW FOCS 502 Euro 2
Page 1: ...LDW FOCS 502 Automotive SERVICE MANUAL...
Page 26: ...26 3 Service Manual LDW FOCS 502 automotive _ cod ED0053027270 3 ed_rev 02...
Page 30: ...30 4 Service Manual LDW FOCS 502 automotive _ cod ED0053027270 3 ed_rev 02...
Page 64: ...64 6 Service Manual LDW FOCS 502 automotive _ cod ED0053027270 3 ed_rev 02 Note...
Page 84: ...84 7 Service Manual LDW FOCS 502 automotive _ cod ED0053027270 3 ed_rev 02 Notes...
Page 96: ...96 Service Manual LDW FOCS 502 automotive _ cod ED0053027270 3 ed_rev 02...
Page 97: ...97 Service Manual LDW FOCS 502 automotive _ cod ED0053027270 3 ed_rev 02...
Page 98: ......