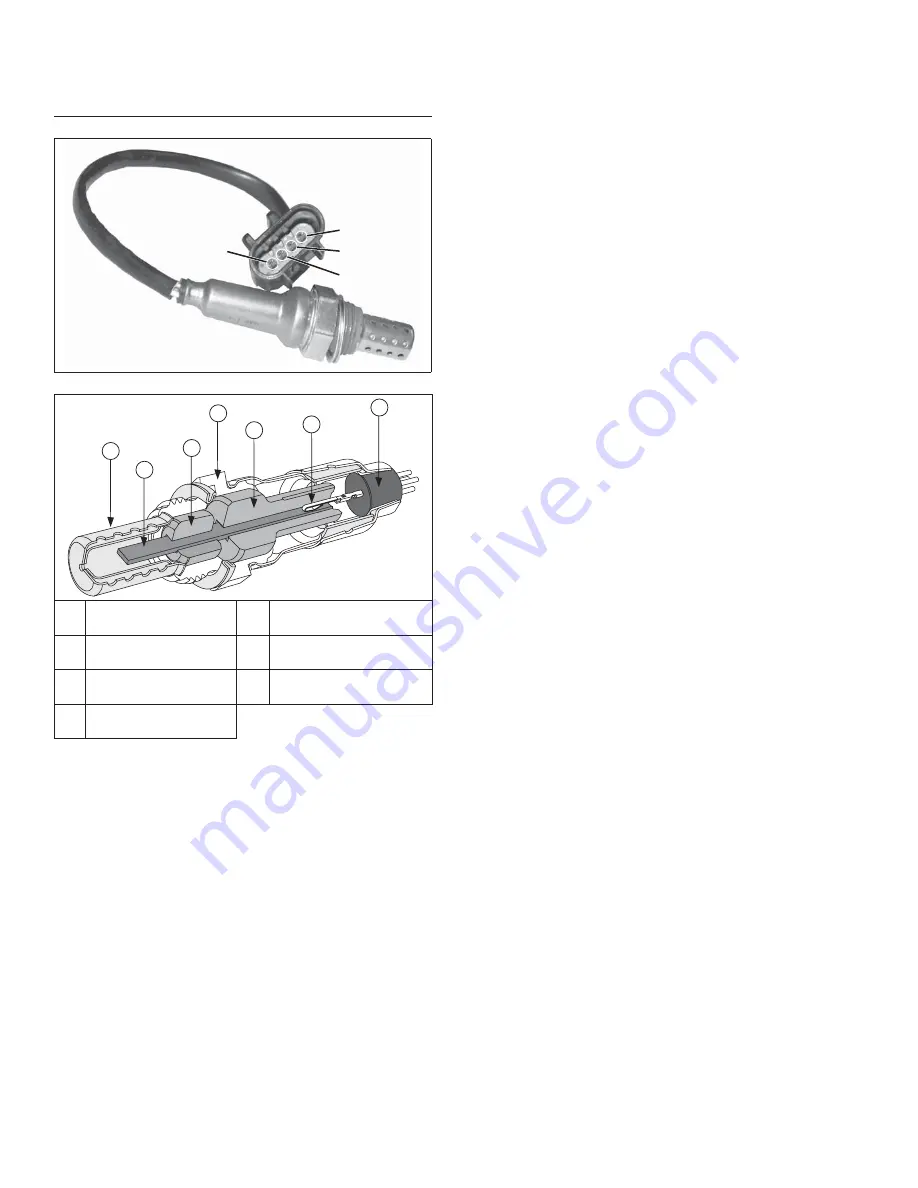
EFI SYSTEM
34
19 690 01 Rev. --
KohlerEngines.com
Oxygen Sensor (O
2
)
Components
Pin D
Pin C
Pin B
Pin A
Cutaway Oxygen Sensor Components (O
2
)
A
B
C
D
E
F
G
A
Protection Shield
B
Planar Element
and Heater
C
Lower Insulator
D
Stainless Steel
Housing
E
Upper Insulator
F
Terminal Connection
to Element
G
High Temp
Water Seal
Temperature must be controlled very accurately and gas
constituents measured to a high degree of accuracy for
absolute sensor measurements. This requires laboratory
equipment to determine a good or bad sensor in
fi
eld.
Furthermore, as with most devices, intermittent problems
are dif
fi
cult to diagnose. Still, with a good understanding
of system and sensor, it is possible to diagnose many
sensor problems in
fi
eld.
Using diagnostic software connected to ECU is a useful
technique for observing sensor performance. However,
user must understand that such software reads a signal
generated by ECU. If there is an ECU or wiring problem,
readings could be misinterpreted as a sensor problem.
Digital nature of signal to software means that it is not
reading continuous output of sensor. A voltmeter can
also be used as an effective tool in diagnosing sensors.
It is advisable to use an electronic meter such as a
digital voltmeter. Simple mechanical meters may place
a heavy electrical load on sensor and cause inaccurate
readings. Since resistance of sensor is highest at
low temperatures, such meters will cause largest
inaccuracies when sensor is in a cool exhaust.
Visual Inspection
1. Look for a damaged or disconnected sensor-to-
engine harness connection.
2. Look for damage to sensor lead wire or associated
engine wiring due to cutting, chaf
fi
ng or melting on a
hot surface.
3. Disconnect sensor connector and look for corrosion
in connector.
4. Try reconnecting sensor and observe if problem has
cleared.
5. Correct any problems found during visual check.
Sensor Signal Observation
NOTE:
Do not cut into or pierce sensor or engine
wiring to make this connection.
Sensor
produces a very small signal. Corrosion or
damage to wiring could lead to an incorrect
signal because of repairs or contamination to
sensor.
1. Using a voltmeter or diagnostic software observe
voltage before engine is started. With key ON,
voltage should read about 1.0 volt. This voltage is
generated by ECU. If it is not present, disconnect
sensor and observe voltage at harness connector. If
voltage is now present, there is a short in sensor or
associated wiring and corrective action should be
taken. If voltage still is not present, there is a
problem with ECU or engine harness.
2. Reconnect sensor and start engine. Run engine at
suf
fi
cient speed to bring sensor up to operating
temperature. Maintain for 1 to 2 minutes to ensure
that engine has gone closed loop. Once in closed
loop, sensor voltage should cycle between about
100 to 250 mv and 700 to 900 mv. If this cycling is
not observed, a determination must be made, if
problem is with engine or sensor.
3. Check engine harness for battery voltage on heater
circuit.
Summary of Contents for Command Pro ECV850
Page 102: ...KohlerEngines com 19 690 01 Rev 102...