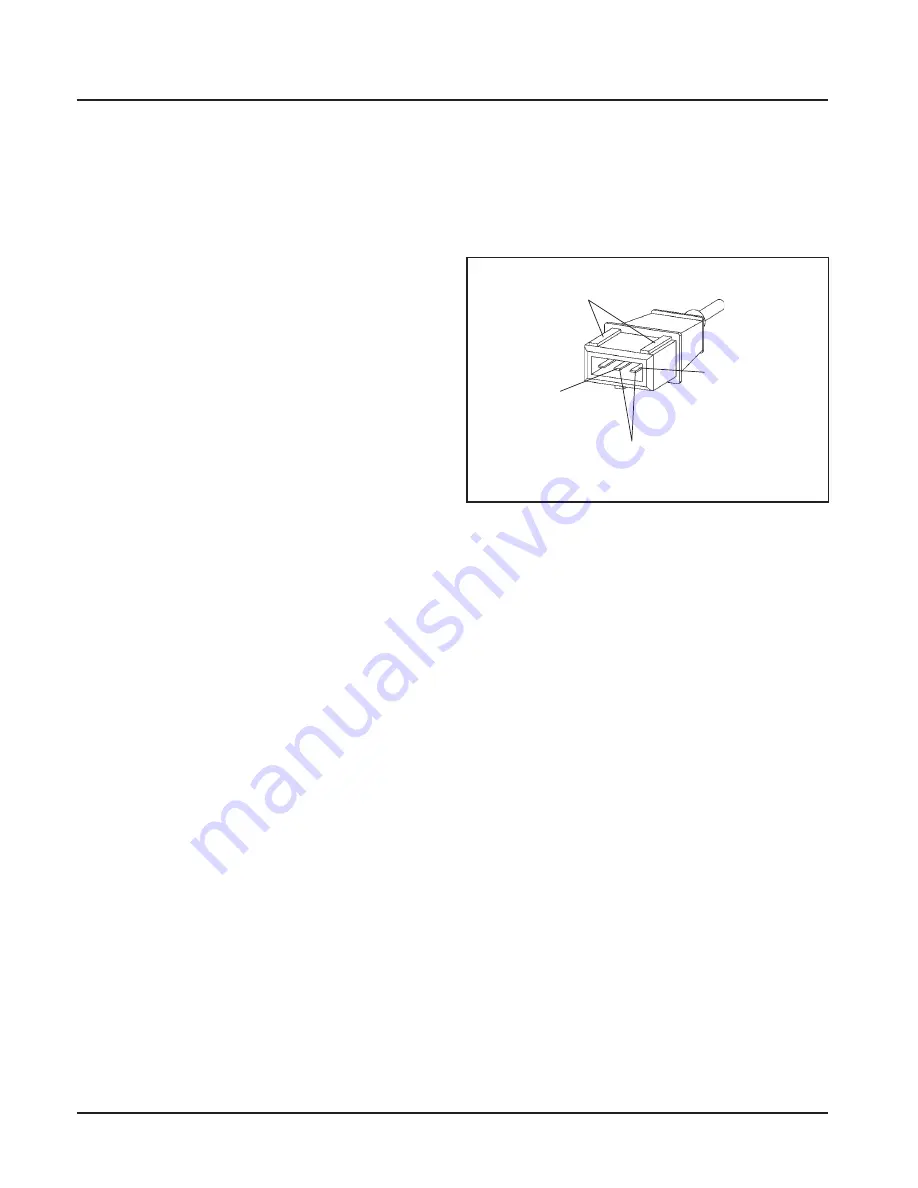
5B.6
Section 5B
EFI Fuel System
General
The engine speed sensor is essential to engine
operation; constantly monitoring the rotational speed
(RPM) of the crankshaft. A ferromagnetic 60-tooth ring
gear with two consecutive teeth missing is mounted on
the flywheel. The inductive speed sensor is mounted
1.5 ± 0.25 mm (0.059 ± 0.010 in.)
away from the ring
gear. During rotation, an AC voltage pulse is created
within the sensor for each passing tooth. The ECU
calculates engine speed from the time interval between
the consecutive pulses. The two-tooth gap creates an
interrupted input signal, corresponding to specific
crankshaft position (84° BTDC) for cylinder #1. This
signal serves as a reference for the control of ignition
timing by the ECU. Synchronization of the inductive
speed pickup and crankshaft position takes place
during the first two revolutions each time the engine is
started. The sensor must be properly connected at all
times. If the sensor becomes disconnected for any
reason, the engine will quit running.
Service
The engine speed sensor is a sealed, non-serviceable
assembly. If “Fault Code” diagnosis indicates a problem
within this area, check and test as follows.
1. Check the mounting and air gap of sensor. It must
be
1.5 mm ± 0.25 mm (0.059 ± 0.010 in.)
.
2. Inspect the wiring and connections for damage or
problems.
3. Make sure the engine has resistor type spark
plugs.
4. Disconnect main harness connector from ECU.
5. Connect an ohmmeter between the designated pin
terminals in the plug:
“35 Pin” (MA 1.7) Metal-Cased ECU:
#3 and #21
pin terminals.
“24 Pin” (MSE 1.0) Plastic-Cased ECU:
#9 and #10
pin terminals.
“32 Pin” (MSE 1.1) Plastic-Cased ECU:
#9 and
#10 pin terminals.
See pages 5B.28-5B.33 according to ECU style. A
resistance value of
750-1000
Ω
Ω
Ω
Ω
Ω
at room
temperature (20°C, 68°F) should be obtained.
If resistance is correct, check the mounting, air gap,
toothed ring gear (damage, runout, etc.), and
flywheel key.
6. Disconnect the speed sensor connector from
wiring harness. It is the connector with one heavy
black lead (see Figure 5B-5). Viewing the
connector as shown (dual aligning rails on top),
test the resistance between the terminals
indicated. A reading of
750-1000
Ω
Ω
Ω
Ω
Ω
should again
be obtained.
Dual Aligning Rails
Test Terminals
Corresponds
To #3 (Metal-
Cased ECU) or #10
(Plastic-Cased
ECU) In Main
Connector.
Corresponds To
#21 (Metal-Cased
ECU) or #9
(Plastic-Cased
ECU) In Main
Connector.
Figure 5B-5. Speed Sensor Connector.
7. a. If the resistance is incorrect, remove the screw
securing the sensor to the mounting bracket
and replace the sensor.
b. If the resistance in step 5 was incorrect, but
the resistance of the sensor alone was correct,
test the main harness circuits between the
sensor connector terminals and the
corresponding pin terminals in the main
connector. Correct any observed problem,
reconnect the sensor, and perform step 5
again.
Summary of Contents for COMMAND CH18
Page 1: ...SERVICE MANUAL HORIZONTAL CRANKSHAFT COMMAND CH18 750...
Page 98: ......
Page 99: ......
Page 102: ......