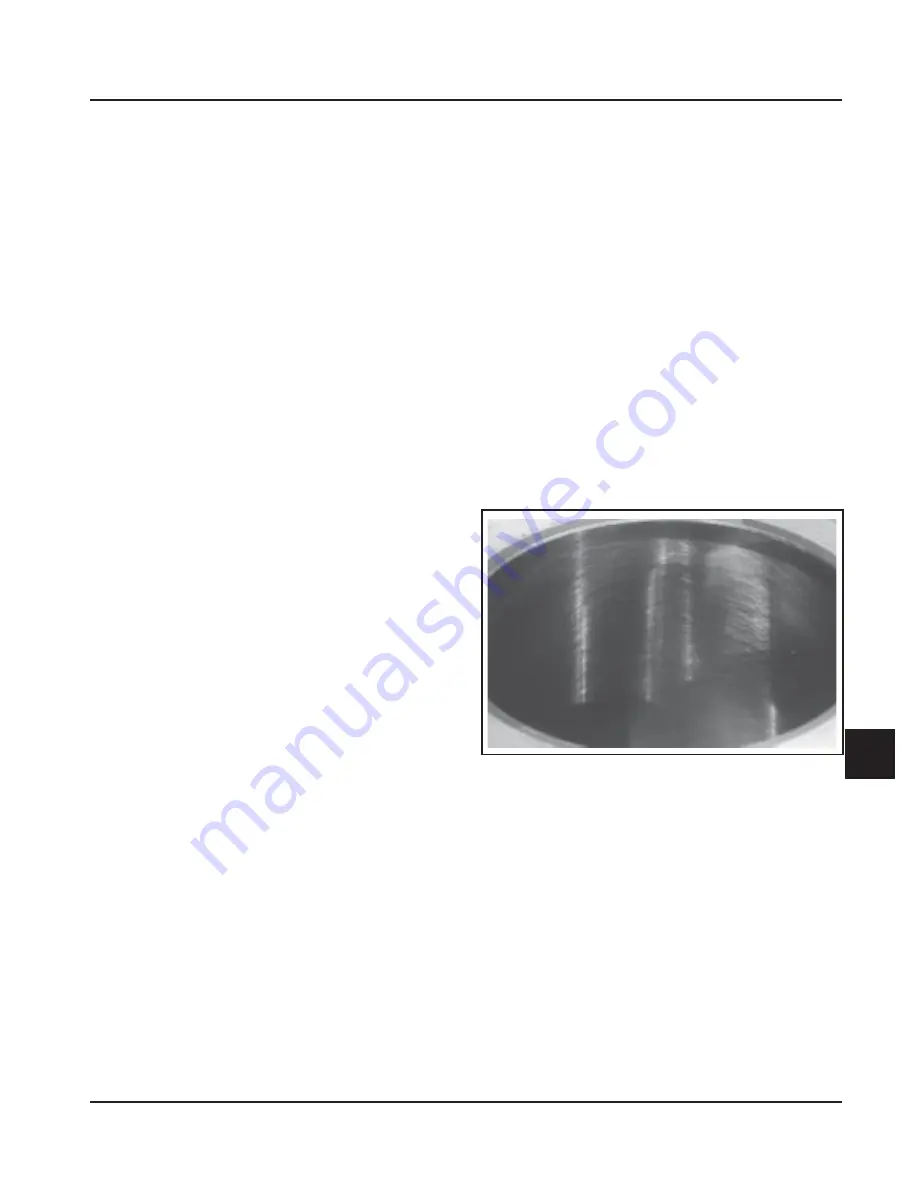
10.3
Section 10
Inspection and Reconditioning
10
Check the cylinder bore wall for scoring. In severe
cases, unburned fuel can cause scuffing and scoring of
the cylinder wall. It washes the necessary lubricating
oils off the piston and cylinder wall. As raw fuel seeps
down the cylinder wall, the piston rings make metal to
metal contact with the wall. Scoring of the cylinder
wall can also be caused by localized hot spots
resulting from blocked cooling fins or from
inadequate or contaminated lubrication.
If the cylinder bore is badly scored, excessively worn,
tapered, or out-of-round, resizing is necessary. Use an
inside micrometer to determine the amount of wear
(refer to the “Specifications, Tolerances, and Special
Torque Values”, in Section 1), then select the nearest
suitable oversize of either
0.25 mm (0.010 in.)
or
0.50 mm (0.020 in.)
. Resizing to one of these oversizes
will allow usage of the available oversize piston and
ring assemblies. First, resize using a boring bar, then
use the following procedures for honing the cylinder.
NOTE: Some CH25-26 engines feature POWER-
BORE
™
cylinders a special patented nickel-
silicone plating process for increased power,
superior oil control, reduced exhaust
emission, and virtually permanent cylinder
life. POWER-BORE™ cylinders cannot be
resized or honed as described in the
following procedure. If a plated cylinder bore
is damaged or out of specification, use a new
miniblock or short block to repair the engine.
Use the following procedure for crankcases
with a cast iron sleeve.
Honing
While most commercially available cylinder hones
can be used with either portable drills or drill
presses, the use of a low speed drill press is preferred
as it facilitates more accurate alignment of the bore in
relation to the crankshaft crossbore. Honing is best
accomplished at a drill speed of about
250 RPM
and
60 strokes
per minute. After installing coarse stones in
hone, proceed as follows:
1. Lower hone into bore and after centering, adjust
so the stones are in contact with the cylinder
wall. Use of a commercial cutting-cooling agent
is recommended.
2. With the lower edge of each stone positioned
even with the lowest edge of the bore, start drill
and honing process. Move the hone up and down
while resizing to prevent the formation of
cutting ridges. Check the size frequently.
Figure 10-3. Cylinder Bore Crosshatch after
Honing.
4. After resizing, check the bore for roundness,
taper, and size. Use an inside micrometer,
telescoping gauge, or bore gauge to take
measurements. The measurements should be
taken at three locations in the cylinder – at the
top, middle, and bottom. Two measurements
should be taken (perpendicular to each other) at
each of the three locations.
Clean Cylinder Bore After Honing
Proper cleaning of the cylinder walls following boring
and/or honing is very critical to a successful overhaul.
Machining grit left in the cylinder bore can destroy an
engine in less than one hour of operation after a
rebuild.
NOTE: Kohler pistons are custom-machined to
exacting tolerances. When oversizing a
cylinder, it should be machined exactly
0.25 mm (0.010 in.)
or
0.50 mm (0.020 in.)
over the new diameter (Section 1). The
corresponding oversize Kohler replacement
piston will then fit correctly.
3. When the bore is within
0.064 mm (0.0025 in.)
of
the desired size, remove the coarse stones and
replace them with burnishing stones. Continue
with the burnishing stones until the bore is
within
0.013 mm (0.0005 in.)
of the desired size
and then use finish stones (220-280 grit) and
polish the bore to its final size. A crosshatch
should be observed if honing is done correctly.
The crosshatch should intersect at approximately
23°-33° off the horizontal. Too flat an angle could
cause the rings to skip and wear excessively, and
too steep an angle will result in high oil
consumption. See Figure 10-3.
Summary of Contents for COMMAND CH18
Page 1: ...SERVICE MANUAL HORIZONTAL CRANKSHAFT COMMAND CH18 750...
Page 98: ......
Page 99: ......
Page 102: ......