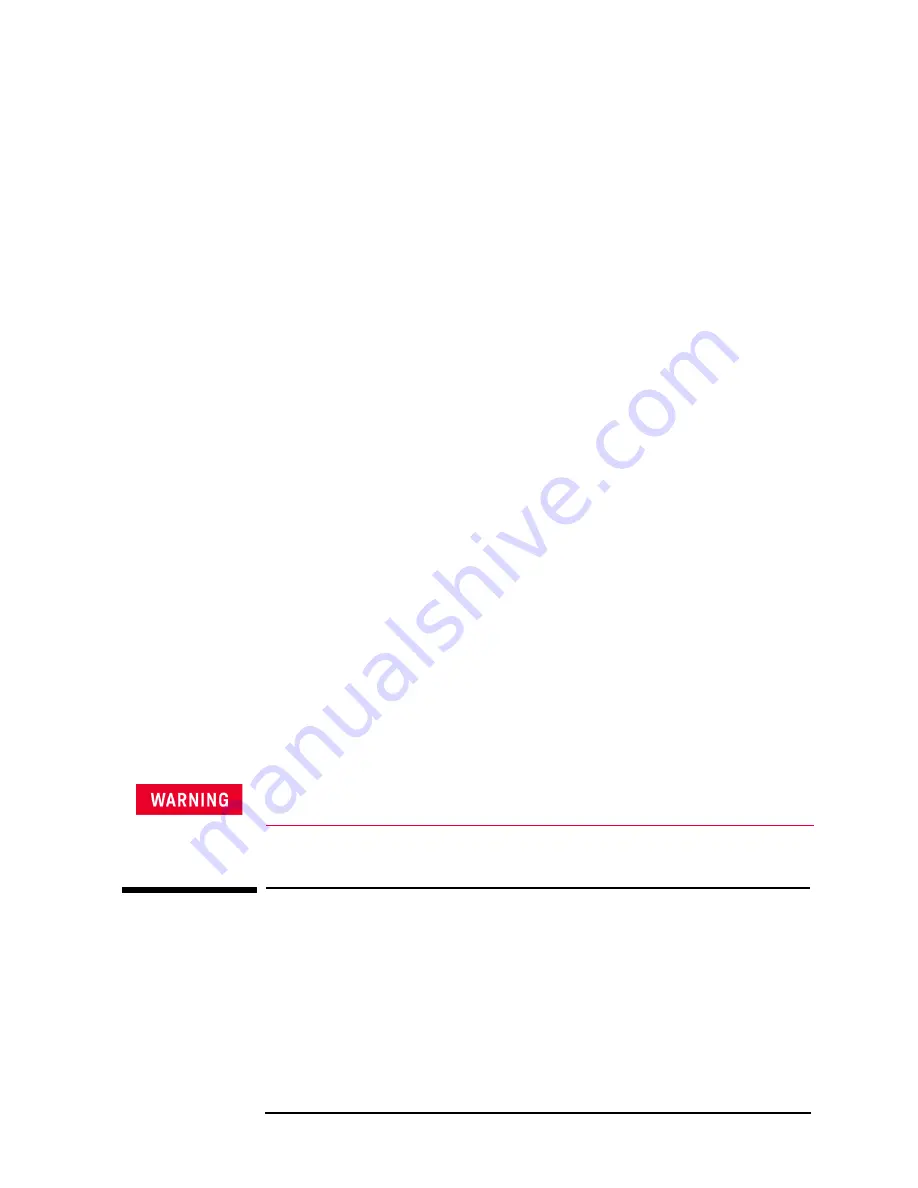
5
• Ground the instrument
To avoid electric shock hazard, the instrument chassis and cabinet must be
grounded by using the supplied power cable’s grounding prong.
• DO NOT operate in an explosive atmosphere
Do not operate the instrument in the presence of flammable gasses or fumes.
Operation of any electrical instrument in such an environment clearly
constitutes a safety hazard.
• Keep away from live circuits
Operators must not remove instrument covers. Component replacement and
internal adjustments must be made by qualified maintenance personnel. Do not
replace components with the power cable connected. Under certain conditions,
dangerous voltages may exist even with the power cable removed. To avoid
injuries, always disconnect power and discharge circuits before touching them.
• DO NOT service or adjust alone
Do not attempt internal service or adjustment unless another person, capable of
rendering first aid and resuscitation, is present.
• DO NOT substitute parts or modify instrument
To avoid the danger of introducing additional hazards, do not install substitute
parts or perform unauthorized modifications to the instrument. Return the
instrument to a Keysight Technologies Sales and Service Office for service and
repair to ensure that safety features are maintained in operational condition.
• Dangerous Procedure Warnings
Warnings, such as the example below, precede potentially dangerous
procedures throughout this manual. Instructions contained in the warnings must
be followed.
Dangerous voltages, capable of causing death, are present in this instrument.
Use extreme caution when handling, testing, or adjusting this instrument.
Certification
Keysight Technologies certifies that this product met its published specifications at
the time of shipment from the factory. Keysight Technologies further certifies that
its calibration measurements are traceable to the United States National Institute of
Standards and Technology, to the extent allowed by the Institution’s calibration
facility, or to the calibration facilities of other International Standards Organization
members.
Summary of Contents for 16034G
Page 1: ...Keysight 16034G Test Fixture Operation Manual...
Page 2: ......
Page 3: ...3...
Page 8: ...8...
Page 10: ...10 Contents...
Page 11: ...1 Overview...