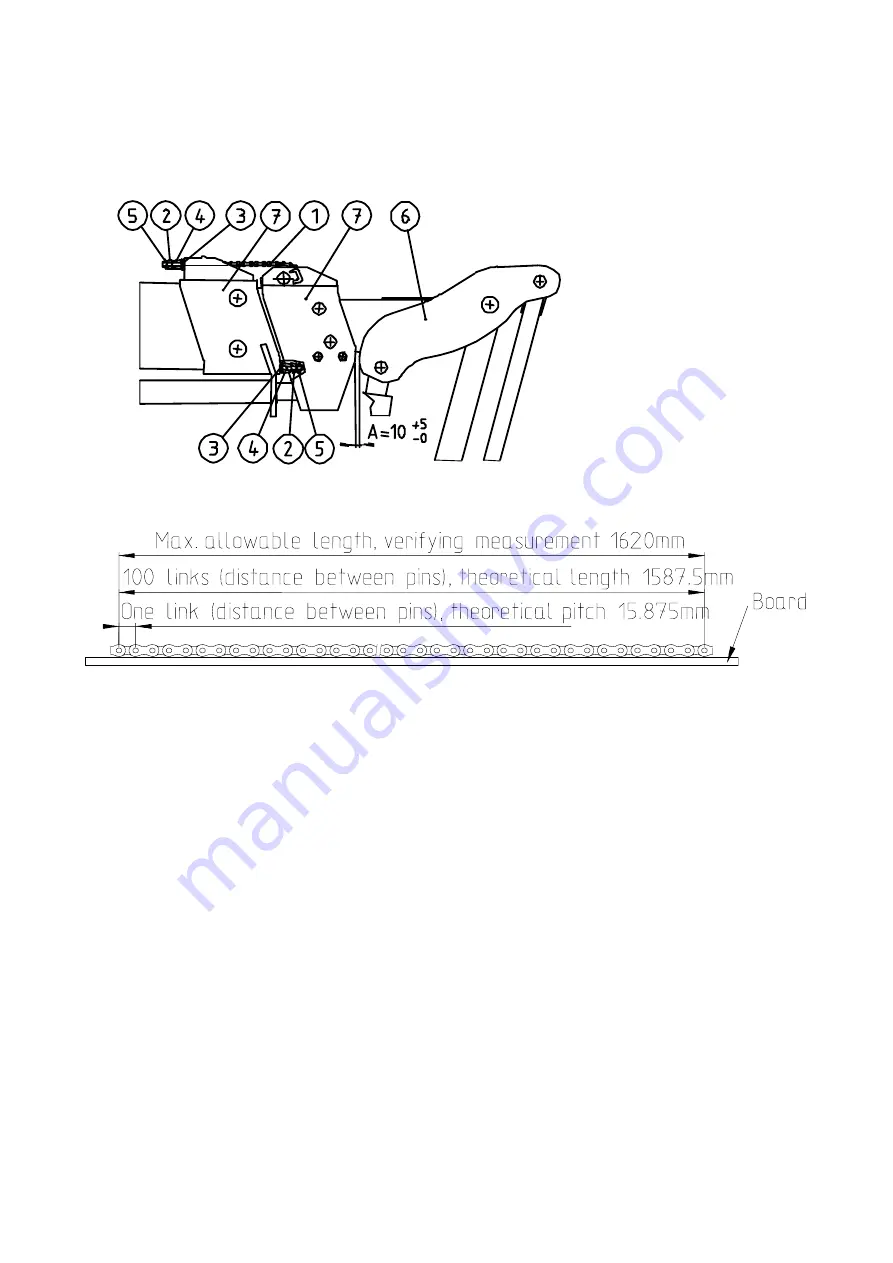
Kesla
®
XS
190
SELF PROPELLED TELESCOPIC PLATFORM
56
3.6 Replace the chains of there is visible wear, cracks or deformed side plates. Check
also the condition of the chain ends.
Adjusting the boom chains
ADJUSTING THE CHAIN TENSION
1.
Support the Access Platform on the outriggers with the wheels slightly off the
ground. Lower the jib completely, and lower the platform on a wheeled carriage (for
instance a pump lifter), and leave the platform.
2.
Extend the boom completely, relieving its weight with the lift cylinder. If the platform
rises from the ground during extending, the lifting radius limiter cuts off both the lowering
and extending movement of the boom. Therefore it is important to relieve part of the load
onto the wheeled carriage.
Retract the boom about 50mm (1.96in) from the maximum reach, and leave the boom in
this position. See illustration, page 57. Note: During extending, no load is allowed on the
platform, observe extreme caution. It is most essential to relieve the boom weight with the
lifting cylinder.
Excessive relieving may make the emergency limit of the load control trigger and
consequently the engine stop.
3.
Adjust the tension of both extensions chains so that with a point load of
8kg(17.6lbs) they just touch the top surface of the boom. The point load should be applied
to the center of the visible part of the chain. There can be 1mm to 3mm (0.039-0.118in)
free play between the chain and the boom.
Summary of Contents for XS 190
Page 1: ...190 SELF PROPELLED TELESCOPIC PLATFORM OPERATION MAINTENANCE ...
Page 6: ...Kesla XS 190 SELF PROPELLED TELESCOPIC PLATFORM 5 TRANSPORT DIMENSIONS ...
Page 8: ...Kesla XS 190 SELF PROPELLED TELESCOPIC PLATFORM 7 SPECIFICATION FRONT ...
Page 83: ...Kesla XS 190 SELF PROPELLED TELESCOPIC PLATFORM 82 ...