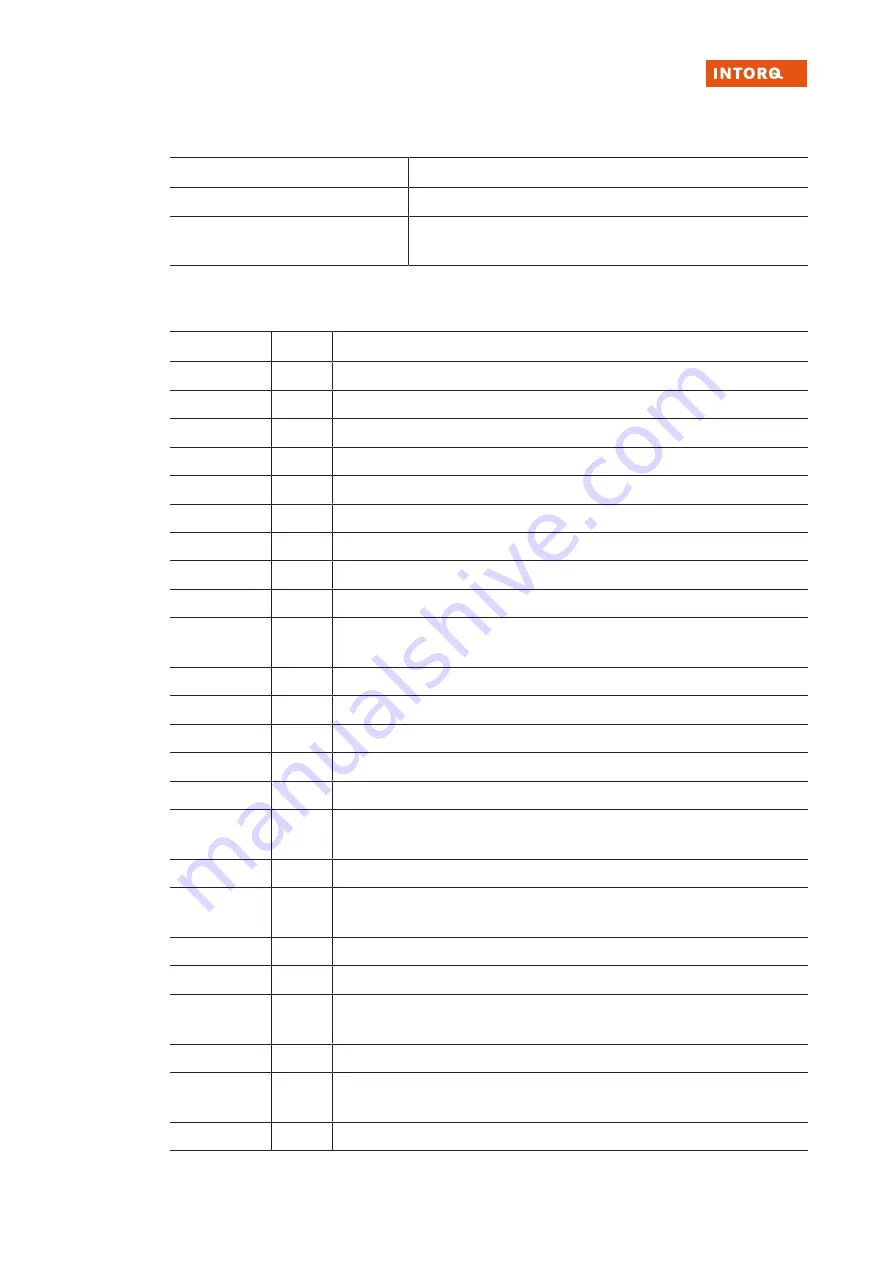
General information
INTORQ | BA 14.0222 | 06/2020
7
1.4
Terminology used
Term
In the following text used for
Servo brake
Electromagnetically released brake
Drive system
Drive systems with spring-applied brakes and other drive compo-
nents
1.5
Abbreviations used
Letter symbol Unit
Designation
F
R
N
Rated frictional force
F
N
Spring force
I
A
Current
I
H
A
Holding current, at 20 °C and holding voltage
I
L
A
Release current, at 20 °C and release voltage
I
N
A
Rated current, at 20 °C and rated voltage
M
4
Nm
Torque that can be transmitted without slippage occurring (DIN VDE 0580)
M
A
Nm
Tightening torque of fastening screws
M
dyn
Nm
Average torque from initial speed to standstill
M
K
Nm
Rated torque of the brake, rated value at a relative speed of rotation of 100
rpm
n
max
rpm
Maximum occurring speed of rotation during the slipping time t
3
P
H
W
Coil power during holding, after voltage change-over and 20 °C
P
L
W
Coil power during release, before voltage change-over and 20 °C
P
N
W
Rated coil power, at rated voltage and 20 °C
Q
J
Quantity of heat/energy
Q
E
J
Max. permissible friction energy for one-time switching, thermal parameter of
the brake
Q
R
J
Braking energy, friction energy
Q
Smax
J
Maximally permissible friction energy for cyclic switching, depending on the
operating frequency
R
N
Ohms
Rated coil resistance at 20 °C
R
z
μm
Averaged surface roughness
S
h
1/h
Operating frequency: the number of switching operations evenly spread over
the time unit
S
hue
1/h
Transition operating frequency, thermal parameter of the brake
S
hmax
1/h
Maximum permissible operating frequency, depending on the friction energy
per switching operation
s
L
mm
Air gap: the lift of the armature plate while the brake is switched